Rose Gray Alpaca Fiber Study
Rose gray is one of the most mysterious colors present in the alpaca fleece color range. It is a color comprising three shades – light, medium, and dark – which can be imagined as coffee with varying amounts of cream added. The hint of rose is most noticeable in medium rose gray but is a magical characteristic of all three shades. Let’s unravel a bit of this alpaca color mystery with a fiber study!
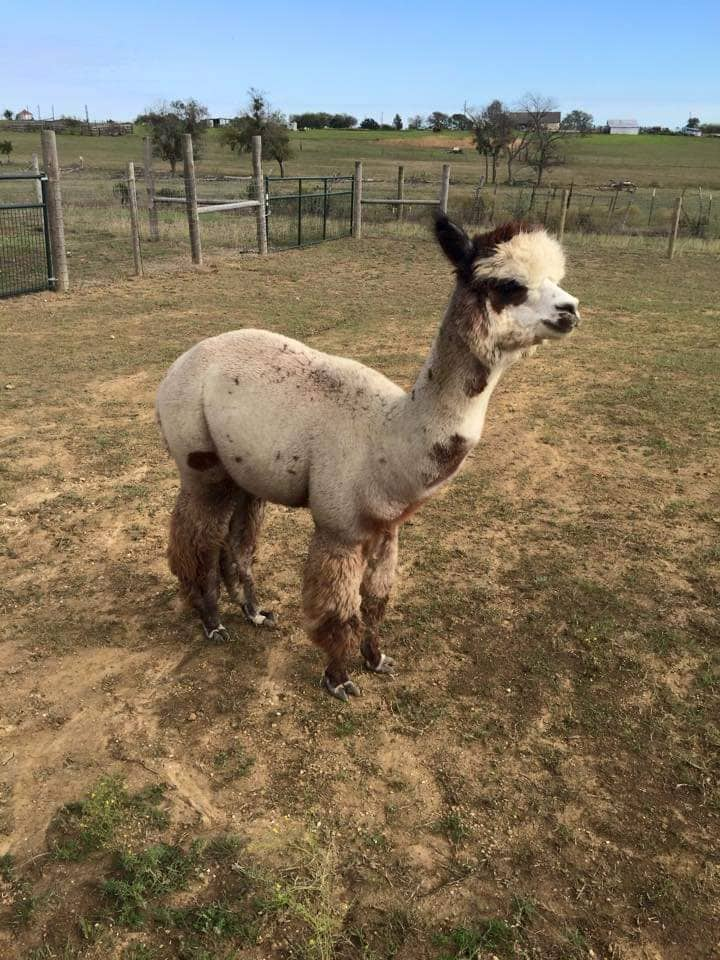
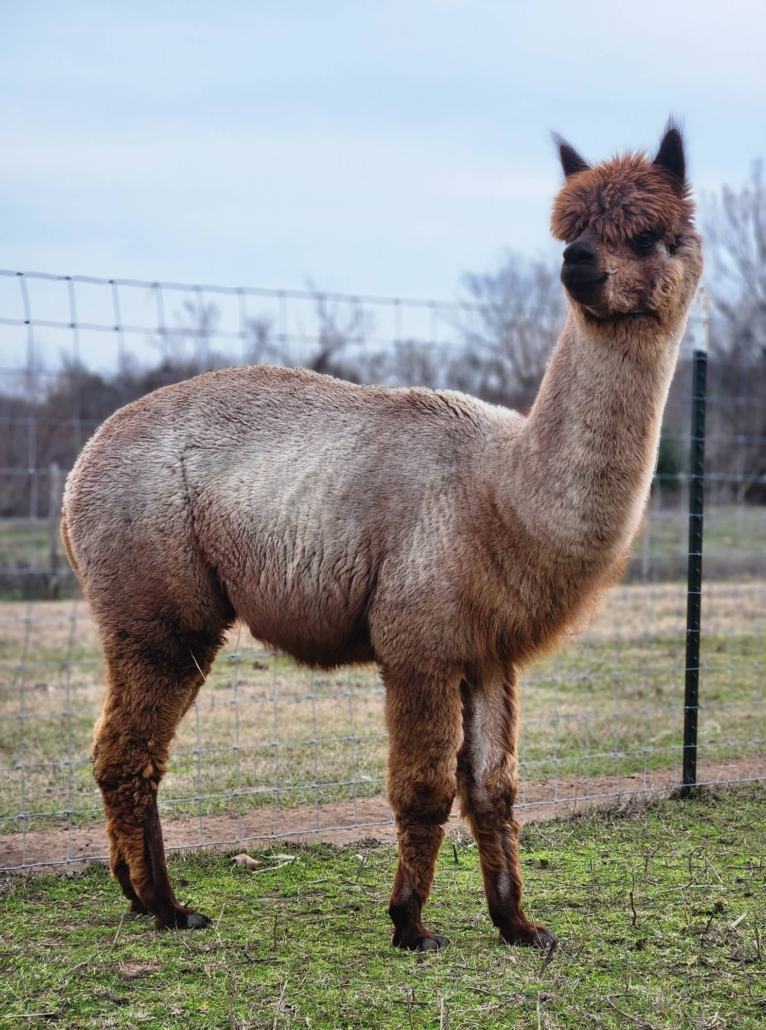
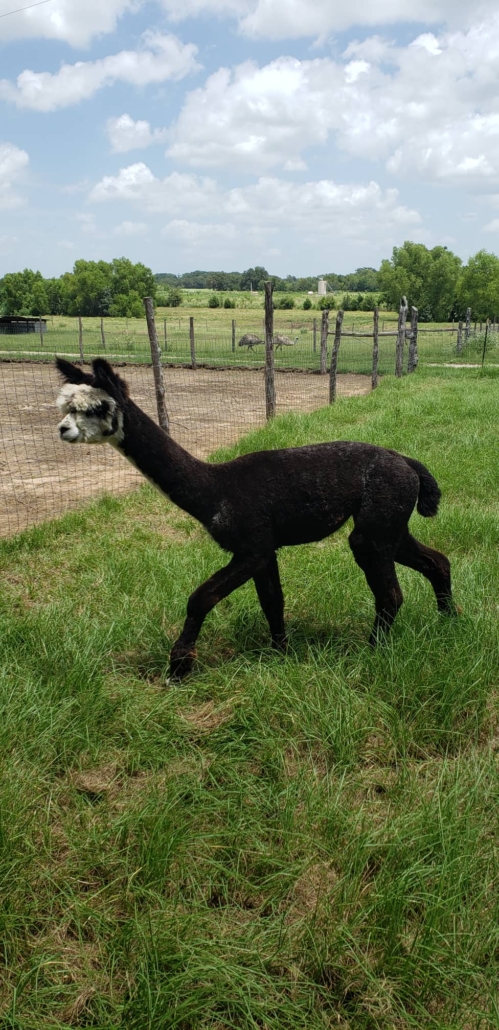
Light rose gray
Gray predominates in light rose gray. It reminds you of fog or of a ghost, with an otherworldly pink hue. On the animal, it looks like a rusty gray cloud until you open the fleece. When spun into yarn it looks slightly darker, but not in a heavy or unpleasant way.
Medium rose gray
Jaw-droppingly beautiful, medium rose gray is the pinkest shade of rose gray. The pink blush only becomes more pronounced when spun. Alpacas with medium rose gray fiber often have adorable faces with brown eye patches and gray-white bodies frosted with brown. As a yarn, medium rose gray fiber stands out with an ethereal look.
Dark rose gray
Dark rose gray is the moodiest and darkest of the rose grays. It has lots of black fibers with sun-kissed tips. On the alpaca, it reminds you of a chocolate truffle, lightly dusted with powdered chocolate on the outside but a midnight black on the inside. Because of its depth, this fiber likes to be the star of its own show as a yarn.
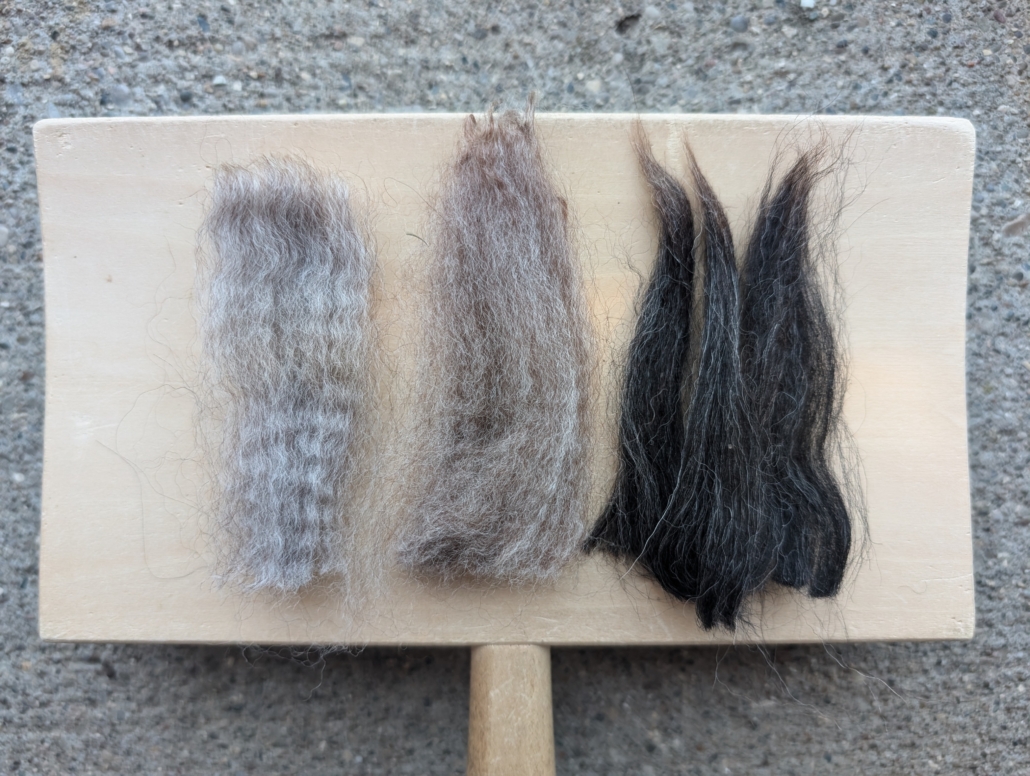
Prep tips
If you get a whole alpaca fleece, the color is usually not uniform throughout the fleece, and this is especially true of rose gray. Do not be afraid to lay out the entire fleece and break it apart according to like colors. You then have more options on blending those portions for your desired outcome. Furthermore, it should be noted that any of the rose grays are easily confused with dark silver gray, but a true rose gray will have brown, white, and black fibers. Dark silver gray will have gray, black, and white, but no brown fibers.
Can you determine softness by color?
Unfortunately, color does not determine softness. Softness comes from age, genetics, feed, and environmental factors. You cannot trust your eyes when evaluating a fleece for softness. When in doubt, spin a small sample. Test that sample against tender areas of skin, such as wrists or neck. Keep in mind that what may be soft and comfortable for you as yarn may strike someone else differently.
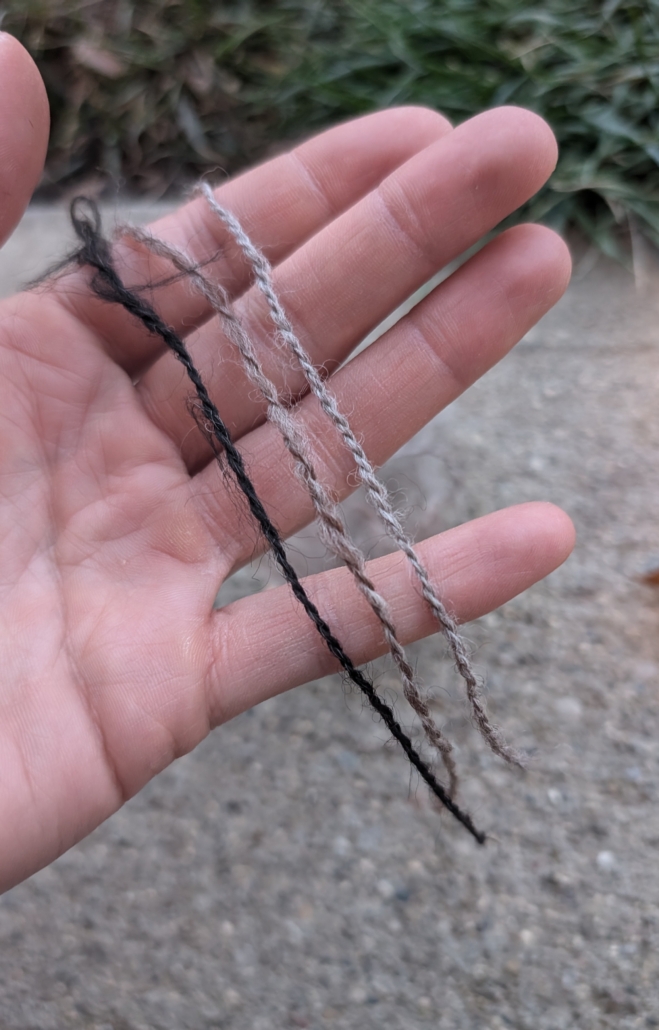
Blending tips
Not only can you blend any or all of the three shades of rose gray together, you can also blend in any other alpaca fiber color to lighten or darken the shade. Because rose grays are so rare, think twice before shifting colors by blending. To brighten your rose gray, add white or brown. To achieve the opposite effect, add gray or black. I always recommend blending in small increments before committing to making a large batch.
Dyeing tips
Of the three shades of rose gray, light and medium are the most suitable for dyeing. The higher percentage of black fibers in dark rose gray causes colors to be absorbed rather than highlighted. The results are dull, muddy shades. In contrast, light and medium rose gray pop with color and richness when dyed due to the presence of white and brown fibers. Imagine jewel tones, and you will understand how dyeing medium rose gray will look.
Spinning tips
It is worth diving into all three of the rose gray shades. As with any handspinning colorway, be sure to buy enough for your project. Even if the rose gray comes from the same farm, the shade will vary from animal to animal and year to year.
Jacqueline Harp is a freelance writer and multimedia fiber artist who spins, felts, weaves, crochets, and knits in every spare moment possible. She is also a former certified Master Sorter of Wool Fibers through the SUNY Cobleskill Sorter-Grader-Classer program. Her Instagram is @foreverfiberarts.
Sending a special thank you to the folks at Camelid Corner, LLC (https://camelidcorner.etsy.com) for providing fiber samples and beautiful rose gray alpaca pictures for this article. Their dedication and care for alpacas is incredible.