Comfort Fiber
words by Sylvia Smith
I write this while enjoying a cornucopia of natural offerings brought on by changing seasons. These seasonal changes have caused me to shift my focus from outdoor activities back to my fiber arts pursuits. My link to emotional quietude has been through fiber. Specifically, I am working through the home study (PLAR) option of Master Spinner Level 2 offered through Olds College. I completed Level 1 in September 2020 and elected to immediately dive into Level 2 as a positive focus for my energy during a pandemic-altered winter. The homework for both Level 1 and Level 2 of the Olds College Master Spinner program requires the student to spin specific fibers, as well as to spin fibers using specific methods and to recommended specifications.
I received a beautiful Athena Capricorn wheel for Christmas and an Electric Eel Nano for my birthday in January. I also recently bought a Dundas wheel from an old friend. Each of these spinning wheels operates differently from my Lendrum double-treadle wheel, on which I have treadled hundreds of hours to produce many miles of yarn. Upon receipt of each of these new spinning machines, I wanted to explore their unique traits without worrying about the quality of yarn that I would initially produce. I dove into my fiber stash and emerged with a bump of my good ole’ comfort fiber.
My comfort fiber is the result of purchasing a fleece produced by a dark colored mixed-breed sheep that I saw in a field about 25 years ago when I was still an inexperienced and solitary spinner living in central Idaho. After the owners sheared the sheep and sold me its huge dark-colored (possibly) Rambouillet cross fleece, I attempted to scour it and then sent it to a mill in north Idaho that processed it into thick pencil roving. This comfort fiber represents the very first raw fleece I ever purchased, and I have used this wool in countless public spinning demonstrations. I include inspirational amounts of this roving when I send aspiring new spinners out into the world with their own spindles featuring whorls made of either CDs or popsicle sticks.
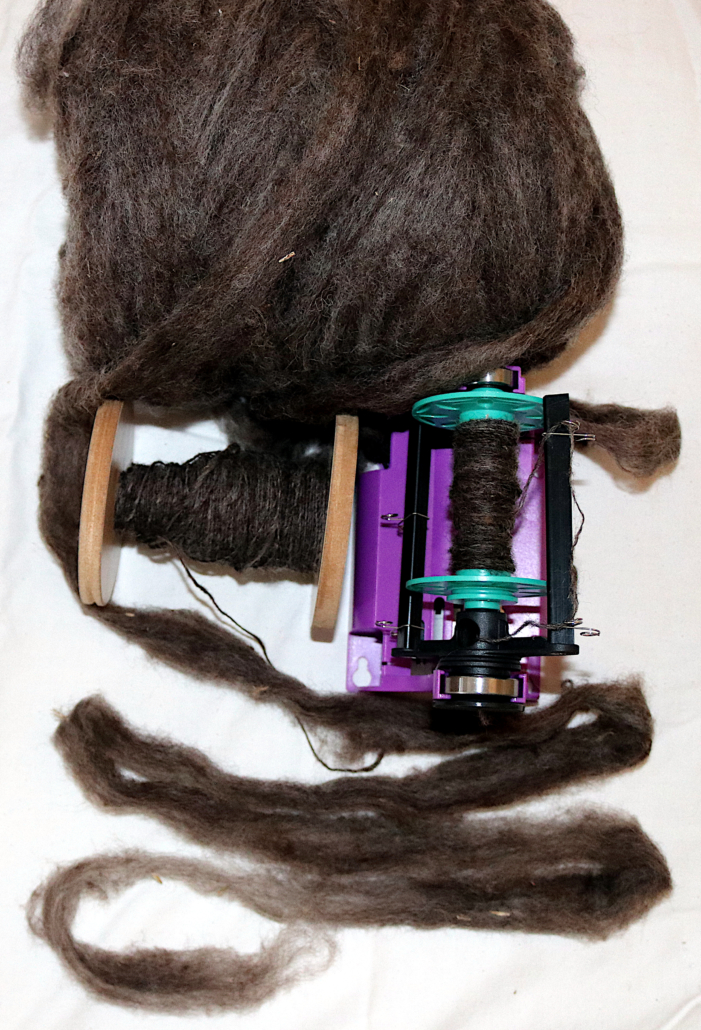
I am much more experienced and discerning about raw fleeces than I was when I purchased that first fleece. I now know I did not do an excellent job scouring the fleece and the fleece likely had second cuts and possibly a break in the fiber. The mill did a fine job processing what I now recognize was a mediocre fiber product
This comfort wool was the perfect fiber for me to use to acquaint myself with my new spinning wheels. Since I have spun a lot of this roving in different circumstances and for various purposes over the years, I have become quite familiar with its woolen and somewhat slubby characteristics. I understand that I will never produce a completely smooth and uniform worsted yarn with it. By using my comfort fiber that will never produce a perfect worsted yarn, I felt free to just play with my new wheels and become familiar with their unique personalities. I relaxed into the spinning process while drafting my imperfect comfort fiber and gained confidence in my techniques with each wheel without judging the yarn as it formed on the bobbin.
I compare my bond with my comfort fiber to our society’s gusto for such foods as baked macaroni and cheese, ice cream, or burgers and fries. We know that a steady diet of these foods will not contribute to a state of optimal health, just as spinning my comfort fiber will not produce perfect yarn. However, the aromas, textures and flavors of our comfort foods remind us of pleasant memories and link us to experiential traditions. It is a good thing to occasionally give our spirits and bellies a moderate dose of such treats, though we may choose to partake more regularly in other foods in order to promote well-being. Similarly, I have learned over many years to be quite discerning about the types of fiber and method of preparation if I spin a yarn for a specific use. When I sat down to a brand new spinning wheel in a world that has been so changed by the pandemic, it felt so very reassuring to smell, touch, and spin my good ole’ comfort fiber because it elicited great memories and validated the knowledge I have gained since I first acquired that fleece. As I drafted my comfort fiber into yarn on my new wheel, I felt like I was spinning threads of possibility for more fun fiber adventures and learning opportunities.
Sylvia Smith learned to spin in 1994 while living in Challis, ID, and was a solitary spinner in that small and remote community. She and her husband now live in Kalispell, MT, where Sylvia has many friends in the fiber arts world and is active in the Alpine Weavers and Spinners Guild.

PLY Magazine believes that Black lives matter, as well as LBGTQI+ lives. Those most vulnerable and persecuted in our communities deserve our love and support. Please be good to each other.
Did you know we also have a monthly PLY newsletter? Sign up here!
Did you know we also have a monthly PLY newsletter? Sign up here!