Rhinebeck Sweater?
/3 Comments/in Festivals, Frontpage Article, Projects, Spinning/by Guest BloggerI’m leaving for New York in less than a week. It’s the New York State Sheep and Wool Festival. I’m excited to see the festival. I haven’t been able to see the festival on my own terms for years and I’ve written myself a little schedule. I did leave some open spaces in case somebody wants to meet up with me for a snack or something.
Anyway, I’ve been thinking for many months that my favorite sweaters are looking a little ratty. My two favorites have been repaired several times. The one called Hiro has ripped at the neck a coouple of times and I just do a bit of a crocheted edge and put her back together. The one that I made from a Jacob fleece has gotten several holes and so I have started embroidering flowers over the holes; a sort of visible mending.
Those repairs are working but for crying out loud I need a new sweater. Yes I have other sweaters…but another one of my favorites, Tappan Zee, also has a hole that I have yet to repair. Hiro is about 3 years old, the Jacob is probably 4 years old and Tappan Zee is maybe 5 or 6 years old. Even without the holes and things I would still need a new sweater. And it’s not like I haven;t been spinning! Lots! But that’s all for weaving the next skirt.
So, anyway, I was digging around in my stash and I came across a cotton project bg from Cooperative Press. When I looked inside there was a handspun sweater that was well under way! I totally forgot about it. I immediatley remembered why I had put it aside. I was looking for a sweater with certain attributes a couple of years ago and my friend, Amy King, offered to design a sweater just for me. And she did! And so I started knitting but then I was a bit confused about an instruction on the left front…and I stopped.
I called Amy! She found her electronic copy! She answered my question. Now I’m moving forward. The body of the sweater is finished and I’m working on the first sleeve. But I have another issue. The yarn is made from BFL/Silk that was specially dyed for me – also by Amy King (Spunky Eclectic) I have no more to spin and I think the sleeves are going to be tight and I still have edgings to do…
After all of that explanation, here’s the question, if I knit faster, will it make the yarn go further?
Singles on a Sock Machine
/17 Comments/in Frontpage Article, Projects, Spinning/by Guest BloggerGuest blogger Cindy Craft is here to share her experiments with using a Circular Sock Machine to knit single ply socks. She also uses a flatbed machine for color work using singles. If you’ve ever wondered about knitting machines, we think you’ll be very inspired by her post!
——————————————————————————————————–
I’m a hand spinner. I spin every night; it’s the way I wind down at the end of the day. As a result, I make a lot of yarn – there are several blanket chests in my house full of handspun yarn. I knit with my handspun yarn but I spin much faster and much more often than I knit. Several years ago it occurred to me that unless I wanted to die with a small mountain of handspun yarn, I needed to find a way to use my handspun faster.
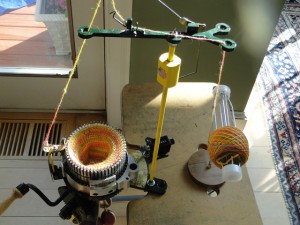
A sock in progress on Cindy’s CSM.
Circular Sock Machines had been on my radar for many years, but I was reluctant to buy an antique as they’re expensive and not always functional, so I had never purchased one. Then one day I was vending at a local sheep shearing show and a vendor a couple of booths down had a CSM that they were demonstrating – and not just any CSM but a new CSM! So I marched down with a small skein of handspun to see if it would knit on the machine. It did, and within a month we had our own CSM and I was happily using it to knit socks out of my vast supply of handspun.
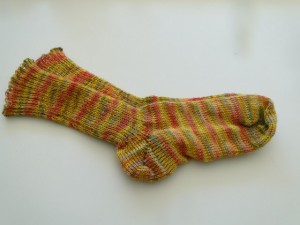
The resulting Navajo Churro socks.
On one of the Ravelry CSM forums I encountered someone who was knitting socks on their CSM from handspun singles. This blew my mind, because I had always been taught to ply my yarn for knitting. I had always thought it might be possible to use singles for weaving but never for knitting – there would just be too much biasing of the knitted fabric. I figured I’d give it a try; even if it was a disaster I wouldn’t have invested more than a couple of hours to make the socks. The resulting socks were just fine. If I looked carefully I could see that the loops were not quite even but the resulting fabric wasn’t twisted or misshapen.
If you look at the photo to the right, you can see that the right side of the knit loops is narrower than the left side but the shape of the socks themselves is even and not twisted. These socks were made from handspun singles of 50% wool of unknown breeding and 50% alpaca that I processed from raw fiber. This photo was before washing.
To the left is a photo of three different pairs of socks I made using singles yarns on the CSM. In this photo you’ll see three socks all made from handspun singles and knit on the sock machine. These are all socks that I have been wearing and washing by hand for at least a few months. The striped sock is made from a BFL x Romney fleece and was dyed – there is almost no biasing of the stitches present in that sample. The blue sock was made from a Dorset x Southdown. It might be 50/50 or 25/75 as it came from a fleece from a local flock but I don’t know which sheep. There’s lots of biasing in this sock to the point where you can actually see the stitches twist on the sock. The third sock is undyed Romney with a bit of sparkle blended in. This is the oldest of the three socks and you can see some of the wear in the right hand corner. This pair is starting its third year. I spun and knitted these socks in very similar ways – the only real difference is the wool type used.
When I started using singles for socks it got me thinking about using singles for other knitting projects. At the same time, using the CSM got me thinking about using a flatbed knitting machine to speed up my knitting. I’ve been knitting singles on a flatbed for the past couple of years now, and I have found the biasing to be nearly imperceptible. Below are a couple of photos of items knit on the flatbed.
The black and white hat is made from a black Shetland fleece, and I think the white is probably some of the Dorset/Southdown cross fleeces I got in 2014. I am hard pressed to see any biasing in this knitting. The blue and white mittens are made from the 2015 Dorset/Southdown cross fleeces, and the biasing is more visible in this knitting. Perhaps the all over pattern in the black and white hat helps to disguise any biasing that may be present.
Do you knit with singles? Have you ever used them on a knitting machine? What have your experiences been?
Meet Cindy: Spinning is at the core of what I do but yarn is not a finished object so I’m always exploring new ways and tools to use my yarn. You can see more of the ways I use my yarn at our website, www.subitofarm.com.
Spinning for Something Big
/6 Comments/in Frontpage Article, Projects, Spinning/by Guest BloggerSo I’m in the midst of this big project that I brought on myself. I probably have at least another year of spinning and weaving before I finish the original plan and since I began I’ve thought of new questions and experiments I want to look into.
The thing is there are many smaller projects inside the big project but the smaller projects aren”t even that small. You’ve probably heard that I’m spinning for weaving. I’m weaving yardage for skirts. The original plan has 7 skirts.
There are 4 blog posts about this project on my website starting here http://bethsmithspinning.com/the-great-skirt-project/
The Schacht Blog followed Jillian and I throough a weaving project. http://schachtspindle.com/smith-and-moreno-take-on-weaving/ There are 8 total posts there.
Now here’s the thing; each skirt needs a minimum of 5000 yards of 2 ply yarn. That’s 10,000 yards of singles. For the yarns I’m spinning for this skirts each bobbin takes 9 to 10 hours to fill. And I’d actually like to spin the next one a bit finer.
Please don’t misunderstand. I make my share of hats and scarves and cowls. They take a little less planning. But I’ve always like to go big. Big bags, big baskets and big projects.
See the card on top of the wool and bobbins and yarn? That’s my control card. It has singles wrapped around it and a 2 ply and 3 ply sample attached. See how it’s all bent up? By the time of this photo I had spun about 3000 yards of 2 ply plus those 3 bobbins of singles. So the card had been through a lot of handling. That’s how I make the same yarn over a long time.
But that’s not really what I’m here to talk about. Many, many people have asked me how I can spin that much yarn that is the same. Same size, same color, same everything. There’s no real secret. But I’ll tell yoou what I know now that I’ve finished three skirts and I’m spinning for the 4th.
After the first bobbin, the yarn begins to be something I can spin without a lot of thought. I’m not switching back and forth between projects too much so it’s not difficult to get back in the groove from one day to the next. I try to spin every day for at least an hour and usually 2 to 3 hours when I can. Practice makes perfect.
Also, I watch a lot of TV. I DVR plenty of things and there are also several series on Netflix that I watch. Since the yarn gets to be something I don’t have to think about I can watch the TV and spin at the same time. Lou is often amazed at that.
I’m very goal oriented. I like to set goals, and set a date for accomplishing that goal. Sometimes I am a bit late – ask Jacey! But usually I get there.
And finally, I like to spin. Come on, you can’t fool me. You have a favorite yarn size that you spin the most. So here’s what i would recommend if you have the desire to spin for a larger project such as a sweater…or crocheted pants. Begin with your favorite yarn. Once you finish the project, I promise you’ll want to do it all over again.
Want help planning your project? Let me know. Need moral support? I’m a great cheerleader!
Spinning “Lopi” Singles
/7 Comments/in Frontpage Article, Projects, Spinning/by Guest BloggerGuest blogger Beth Abbott is here to share with us her experiences spinning “Lopi” style singles yarns and using them in her knitting. Follow along with her exploration of the history of these yarns and her efforts to engineer a way to spin them for herself.
———————————————————————————————-
When I started my study on Icelandic fleece, one of the first things I learned was that although traditionally the fleece had been separated into the two coats, thel (undercoat) and tog (long hairy outer coat), currently in Iceland, to my knowledge, there was/is no one spinning the coats separately. The two coats are now spun combined into several styles of singles yarns.
Lopi in History
In the late 1980’s there was “Lopi” under the brand name of Alafoss and a yarn that was mostly used in Iceland called “eingirni” meaning “singles”, a fine fairly firmly twisted yarn used in lace knitting. In early 2000 there were two more yarns added to the collection called Lett (light) Lopi (about half the diameter of the original Lopi) and a Heavy Lopi which was about twice the diameter of the regular Lopi. The company has undergone a reorganization and is now Istex.
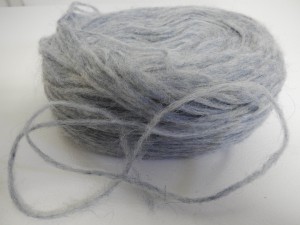
A lopi plate showing the size of the strand – note the lack of twist.
The word lopi means roving in Icelandic and the plötulopi plates that the Icelanders use for knitting their popular patterned yoked sweaters are actually just the last roving step in the process of spinning the fine “eingirni.” Usually three strands of this roving are worked together and the result is a very bulky but very light airy sweater, very warm, because the air is trapped in the yarn. The Lopi yarn was developed for the export market because they thought it would be easier for non-Icelanders to knit.
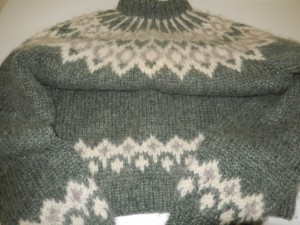
a hand knit sweater from real lopi plates
An interesting point is that those yoked sweaters have only been a tradition in Iceland since the 1920s, when a creative spinner decided to try to knit on her knitting machine with the rovings as they came from the mill, without spinning them. When she found this was possible, it opened up a whole new area of knitting for the hand knitter as well as the machine knitter.
Re-creating a Lopi style yarn
The original Lopi yarn has about one twist per inch and a twist angle of 15º. The diameter is about 8 – 10 wraps per inch. As many of you will know, it is difficult to spin a yarn this soft and thick consistently, and with some air to prevent it from being dense and heavy. I found that preparation was key to success in spinning a Lopi style yarn.
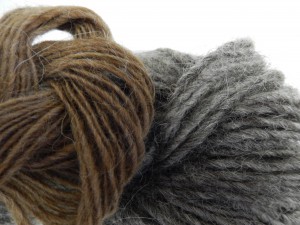
handspun Lett lopi and regular lopi style yarns
To prepare an Icelandic fleece: wash, dry and then carefully tease out the locks, paying special attention to the butt ends which tend to clump together during the washing. It is worth noting that the “thel” or undercoat is extremely fine and short and felts very easily, so that care is also needed in the washing process – NO playing with your hands – while the fleece is in the hot soapy water. Carefully lift the fleece from the slightly cooled water to empty the tub and fill with rinse water. Try to keep the temperature of the rinse water close to that of the slightly cooled wash water. Again – no movement while it is rinsing. Carefully lift out of the rinse water and either roll in a towel and dry flat or put in the washer on JUST SPIN – no rinsing process – to take out the excess water. Then lay flat on towels to dry. Once the fleece is dry, the teasing is fairly easy, though time consuming. However, the time spent in this part of the process will save time and agony later.
After carefully teasing out the locks I put them through my drum carder. I usually use a Louet drum carder for Icelandic as it has longer and finer teeth and will take the loft of the combined coats more successfully than many other carders. Usually I put the fleece through at least twice, splitting the first batt into two lengthwise and then putting each through again. I hold the batt up to the light and see if there are neps and lumps that need further carding.
Once the fleece is well carded, I split the batt into narrow strips and predraft these into a sort of roving form. These I spin on a Louet wheel, because of its larger orifice and bobbins. Using the lowest bobbin/flyer ratio you have, work slowly to draft a bulky yarn, as consistent as possible. Any lumps often tend to drift to the outside of the yarn and can be picked off. Aim for one twist per inch. If need be, because you have only a high ratio wheel, you can put the yarn through the wheel again in the opposite direction to remove a little of the twist.
It is not easy for the hand spinner to create the roving style of Lopi but, by using my fingers to fan the fibres and letting the twist pick up the fibres, I am able to create a very light and airy, softly spun singles yarn. If I put in a little more twist, I can ply two strands together and get a Lopi diameter yarn that is airier than the original Lopi yarn, and one I like better.
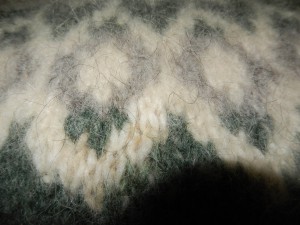
closeup of hand knit real lopi sweater – purchased in iceland – long hairy look is due to the long tog fibres in the yarn
The next time someone tells you that you must cut the fibres to be the same length for blending, or that fibres should be compatible for blending, remind them that the Icelandic fleece, with its strong outer coat like a long Lincoln and its fine under coat, more like the finest, shortest Merino, are regularly blended and spun in Iceland.
Beth Abbott has been spinning since 1975 and earned her Master Spinner Certificate from Georgian College, Owen Sound Ontario, in 1990. Her in-depth study is now in print as a book. Beth teaches in the Spinning Certificate Course at Haliburton School of Art on a regular basis. For more information on the Icelandic Fleece, consult her book “The Icelandic Fleece – a Fibre for All Reasons”. It is available from Beth and Ron Abbott – contact elizabethandronabbott@gmail.com
Scouring
/10 Comments/in Frontpage Article, Projects, Spinning/by Guest BloggerIt’s January and around my house that usually means a lot of wool washing is going to happen. I have 8 teaching appointments this year and almost everyone chooses classes that require unprocessed wool. That’s because around 75% of my class list consists of classes that are about processing wool from raw. I love it. I think the yanr you get when you do your own processing is better than the yarn you spin from mill processed stuff – that’s not to say that i don’t spin plenty of mill process wool. It’s like thinking about cakes. The completely home made from scratch cake will always be better than the box mix but that box mix surely has its place on my shelf.
Anyway, when I get to scouring I usually wash about 60 to 80 pounds per week. This year my list has 21 breeds that need a good dunk in the hot water. That will take me about 3 weeks to complete.
Everyone has their favorite method for scouring raw fleece and I thought I’d talk about mine today.
I’ve read every article that has come in my view about scouring and talked to other spinners who love raw fleece and from all of them I developed the method that works best for me and my space. I tried doing the whole fleece in the bath tub and I hated it. I ended up wet from my shoulders to my waist. Plus all that getting down onto the floor made me sad.
I tried it in the washing machine tub but I hated it because at first it was too scary and then it was just too much moving the wet wool in and out of the tub. as the water filled and drained.
I haven’t tried the fermented suint method because I need to get the wool washed now and it takes too long…plus it stinks.
In addition, I have tried most of the wool scouring products plus Dawn and Orvus and found that my favorite is Unicorn Power Scour. One of the main reasons I love it is because there is no need to boil water to get the temperature high enough to melt the lanolin. There is some kind of magic ingredient that makes that not necessary and since I wash wool in my laundry room on the second floor, heating water would make me crazy.
So after all that, what do I do? I have 4 tubs that I use. I got them from the people at Soak. They call the ones I use Phil. You can get them from the Soak website or your local shop that sells Soak products. These basins hold between 1.5 and 2 pounds of wool depending on the breed and how fluffy it is. That’s why I have 4. If I have a fleece that weighs 8 pounds I can almost always wash the whole thing all at one time.
So, I line the basins up using my washer and dryer as a counter top. I have a utility sink next to the washer and I have a cut off garden hose attached to the faucet. This way I can direct the water to the tub that is furthest away without having to move it an extra time. (ignore the messy stuff around the sink, please.)
I turn on the hot water and let it run a bit until it is as hot as it will get. We have our hot water heater set to 120 degrees F. (Unicorn recommends 140 but this temp works for me.) Then I start filling the buckets until they are a little over 3/4 full. It seems like a lot when you are going to put the wool in but the wool soaks up some water and often I have to top them off a bit after the wool is in.
But before I add the wool I add the wool wash. The Power Scour works sort of like dye as far as how you determine the amount to use. It is based on the weight of the wool you want to wash. For these basins when I am washing about 2 pounds I add around 2 to 3 tablespoons in the first soak.
When I add the wool I push it down into the water. I have a couple of paint stirrers on the shelf for this purpose.
I soak the wool in the hot water and scour for at least 15 minutes. It’s important to not forget about the wool at this point because if the water cools and the lanolin sets back onto the wool it can be much more difficult to remove.
So, after 15 minutes I take the basin to the sink and dump it out. I squeeze out a bit of the water and refill the basin with hot water. At this point I add half as much of the scour to the basin. After all 4 have been emptied and refilled I let them soak for another 15 minutes.
I repeat the process 2 more times but with only clear water. So that’s 2 washes and 2 rinses. After the last soak the water may not be clear. There may still be some dirt showing but I don’t worry about it. There are several more opportunities to get the last bit of dirt out.
At this point when i dump out the basin in the sink, I transfer the wool into lingerie bags. I used to just squeeze out as much water as I could and then roll the wool in towels but I like to spin it out in the washer now. It gets out more water and I don’t have as many sopping wet towels laying around.
One bag will hold all of the wool from one basin.
I let it go through the whole spin cycle. Make sure that your washer doesn’t spray water during the spin. If it does, you can turn off the water going to the washer during this part.
And finally I take the wool to the drying racks. These are just sweater drying racks that are stackable. I have several of them and if I run out of space i move to the floor. I wash wool until there is no more space and then I may need to take a a day or off while the fleeces dry and some space is available. I make sure to write the breed on a card and place it next to the wool. Sometimes if you have several white fleeces drying next to each other it can be a little confusing so the labels are important.
All of this takes about 90 minutes from start to finish and I feel pretty accomplished.
Do yu have any special things you do to wash your fleece?
If you are interested in playing with the fleeces i’m scouring now, come and see me in Boulder Colorado! I’ll be ther in February. Here’s the link for registration. http://www.handweaversofboulder.org/explore/forms/HGBBethSmithRegistration.pdf
Use Your Yarn
/25 Comments/in Frontpage Article, News, Projects, Spinning/by Guest BloggerI teach a lot of classes and I am always surprised at how many spinners I meet who don’t use their handspun yarns for projects. They give me lots of reasons for it. (1) They don’t think they have enough yarn for a project or (2) they don’t have enough matching skeins or (3) they think their yarn is crappy or (4) they don’t really know how to use it or (5) they sell it.
I have answers for all of this and I hope if you are a person who doesn’t use their hand spun yarn that I can help you change your mind. Let’s go through the reasons one at a time.
Number 1: Not enough yarn for a project.
For this problem, if you are a knitter or crocheter, I love Ravelry. If you go to the Patterns section you can search based on yarn size and yardage for projects and you would be amazed at how many projects there are available for small amounts of yarn. I just finished this Lucky Cowl designed by Amy King with a teeny tiny skein.
Number 2: Not enough Matching Skeins
It’s funny how we all have some kind of color scheme that we stick to when we buy fiber. what that means is that most of your fiber will coordinate. It doesn’t need to matche exactly to make a project. In addition, this shawl was made with 3 different thicknesses of yarn. and it worked and it’s warm and I love it. This shawl was made using the Knitting Lace Triangle Shawls book by Evelyn Clark
Number 3: The Yarn isn’t Good Enough
This is a terrible excuse! Here’s the great thing about using your yarn – The lumps get hidden in the fabric or make a nice texture. See the yarn on the right? It’s Columbia, three ply, spun with a long draw which is less consistent than short draw. It also is a roving that has a lot of neps in it so that adds to the texture. I used it for the Hiro Sweater which was designed by Julia Farwell Clay. But check ouot the finished sweater! All of those lumps disappear!
I wear this sweater all the time! You can even see the dirt stains in this photo because I don’t want to take it off long enough to clean it. I love it so much I’m thinking of making another one. Probably with lumpy yarn, too.
I used the same fiber for a weaving project I’m working on. I made the yarn a bit thinner but it still is not very consistent but I made a beautiful skirt from the woven fabric! (Ignore maggie’s messy room behind me.)
Number 4: Not Sure What to Do With It
This is where sampling or trying things or just swatching comes in. Maybe you need a beginning knitting/crochet/weaving lesson. Maybe you need to find a group of people who are also interested in yarn. Maybe you should pick out a project from a Ply Magazine issue and work on it.Most of us are spinning smooth yarns and the magazine reflects that but there are plenty of articles, the current issue and a couple of issues coming up that will inspire those of you who love textured yarns.
Number 5: Sell The Yarn
Here is where I will climb atop my very tall soap box. And these words go for even those who don’t sell their yarn but aren’t using it. How can you know how to improve your yarn if it isn’t being used in any projects or swatches? How do you know that it even works as intended? Please, please, please! Use your yarn. See how it acts in the fabric. See if it softens or gets more firm. check if the plying is too tight or too loose. Make sure it doesn’t fall apart or begin to pill before the skein is even used up. These things will make you a better spinner.
If you don’t know how to weave/knit/crochet, ask a friend to try some out and give you feedback. You can always use these samples and swatches to help sell future yarns.
Yarn is not a finished object.
What are you working on with your handspun yarn? Let me know!
And the Winner Is!
Thank you so much for all of you who took the time to review the Texture Issue of Ply. The winner of the batts is Christina Bowers!
Arm Knitting with Textured Yarns
/1 Comment/in Frontpage Article, Projects/by Guest BloggerRegular PLY contributor Maja Siska is here to show you how to turn your skein of textured bulky yarn into a wearable piece in less than 30 minutes. Take it away, Maja!
——————————————————————————————————–
Arm knitting works well for that special skein that is too beautiful to knit regularly, or just the latest crazy yarn off your wheel looking for a life of its own. Yes, you could wear the skein around your neck – but if you want something more “finished,” this is a good way to go.
How do you do it? Just use your arms instead of knitting needles. It makes gigantic stitches, which open into loops that show all the glory of your yarn.
It is child´s play – literally: I have taught it to a 7 and 10 year old and within half an hour they were proudly wearing their scarves.
I love arm knitting because it is quick and easy, it makes a proper item that you can wear multiple ways, you do not need a lot of yardage, and last but not least it allows your textured yarn to be seen in all its beauty.
Adapting Arm Knitting for Handspun
Depending on the length of the skein, I have begun with anything from 5 stitches for a long thin scarf to 12 stitches for a wider one. If you knit it and it is too wide and too short or the reverse, just rip it back and change the number of stitches; it will only cost you another 20 minutes or so.
For a cowl, I found the best way to close the loop is to make a scarf and then knot the two ends together into every other stitch or so with a bit of left over yarn. I leave about 2 inches of tails on these knots and they become a feature – rather than trying desperately to hide the seam.
An example: approximately 35 yards (32m) of yarn, arm knitted across 9 stitches = 4 ft (120 cm) length, which works for a cowl.
And the most important rule: HAVE FUN!
For more information …
Here is just one video demonstrating this technique:
https://www.youtube.com/watch?v=YPer3Xv2QSM
Trained as an architect Maja is also a designer, artist, knitter and spinner. Anything wool is high on her list. She lives in Iceland on a farm with an array of animals. https://www.facebook.com/Icelandisfullofwool/
On ravelry: majasiska.