Lofty Yarn Spun from Finger-Opened Locks
words and photos by Donna Kay
I love preparing fiber – whether it is handcombing lustrous locks or carding puffy rolags. But sometimes we forget about the oldest tools of all: our hands. Consider getting “back to the sheep” and spinning hand-prepared (literally) locks into a rustic lofty yarn. It is a fitting and extremely satisfying method of preparing and spinning a primitive-type fleece. There’s something special about the way the individual character of the two coats can be highlighted in one yarn.
Choosing a fleece
Dual-coated sheep produce fleeces with amazing variation in character and color. Breeds I have had the pleasure to work with include Icelandic, Shetland, and Norwegian Spelsau, and each has something wonderful to offer. When choosing a fleece to spin from the lock, I consider the qualities I want for my project. Locks with more undercoat than outercoat spin up into a soft, lofty yarn. Locks with dominant or long outercoat produce a thinner and denser yarn.
Spinning from the lock also allows for random or controlled color placement. I can choose a solid color or a variation since the inner and outer coats are often different. For an article of clothing, I look for open, VM-free locks with dense, fluffy undercoat and relatively silky and flexible outercoat. Fleeces with a coarse outercoat are wonderful but better used for rugs and other hardwearing pieces. (Note: the longest and coarsest outercoat fibers can easily be removed when preparing the locks for spinning.)
Primitive sheep exhibit wide variations of length and diameter within the fleece, so I sort the fleece into sections of similar locks to achieve a consistent yarn. The sides and shoulder will often be the closest in length and diameter and often the softest outercoat. The neck, back, and britch areas tend to be shorter and/or coarser and are set aside for other uses. Locks with excess sun damage, scurf, kemp and imbedded VM are discarded.
Preparation
A freshly shorn fleece can be prepared and spun in the grease. Locks from a fleece that has been stored unwashed will not open as easily and the drafting will be uneven. To prepare a low-grease fleece, I often use a cold water soak to remove the dirt and suint. Dual-coated fleeces wash easily and often require only one wash. I am careful not to use too much detergent or the fiber can feel harsh and dried out. Locks are placed in plastic mesh baskets, maintaining lock formation, and then washed and rinsed in hot water. Felting happens easily with primitive fleeces, so keep handling to a minimum.
I use my fingers to open up the cut ends of the locks and remove any loose or felted bits. These can resemble second cuts but usually are the immature beginning of the next year’s fleece if the shearing took place after the coats natural rise in the spring. For smoother, consistent yarns, I keep the lock formation intact, leaving the tip as is. Another option is to open the locks completely into a cloud of fibers.
Spinning
My Majacraft Suzie is put to good use for spinning this yarn. It is equipped with a delta orifice, a large open ceramic hook, and scotch tension. There is nothing for errant tails to get snagged on, and the scotch tension allows me to quickly adjust the take up so the yarn winds on smoothly. For yarns with a soft twist, I want 1-1/2 to 2-1/2 twists per inch with a twist angle between 10 and 20 degrees. For the yarns shown in the photos, I used a of 4.5:1 ratio with a light take up. A rhythm of drafting 1x per treadle gave me the amount of twist I wanted. The low angle of twist ensures that the finished yarns will be light but strong thanks to the longer outercoat fibers acting like glue holding everything together. These worsted to bulky weight yarns contain a good mix of both outercoat and undercoat.
To spin from the lock I hold a small handful lightly in my fiber hand and draft from the cut end using a backwards woolen draft. I pinch the end of the twist with my forward hand as I draft back half the length of the undercoat with my fiber hand. My fingers open, releasing the twist to capture the newly drafted fibers. When a small amount of undercoat remains in my hand, I add a new supply of locks, joining undercoat to undercoat so as to maintain the mix of fibers and diameter. This method affords me some control and consistency, but these yarns certainly display individual character! For the smoothest yarn I draft both coats together as evenly as possible. If I want texture in the form of “tails” I concentrate on drafting the undercoat, allowing the outercoat to slip through my fingers and wrap around the outside of the drafted fibers. It is important to relax and let go, allowing the lumps and bumps to enter the yarn. If at any point drafting becomes difficult, I make sure I am not holding the fiber too firmly.
When spinning from the cloud, it is a little harder to maintain consistency. I use a short backward or a supported long draw. Holding a good-sized handful of fiber gives me the best results. The yarn has a lot of variation in size and texture and works well for a rustic knit item or as weft in a woven piece.
A worsted draft creates a denser yarn because the fibers are smoothed and compressed as they are drafted. It seems counterintuitive, but this draft actually accentuates the lumps, creating a noticeably thick and thin yarn that has a firmer hand. I usually do not use this draft unless it is to be used as warp yarn.
After spinning a few locks, I stop and create a plyback sample by pulling a length of yarn off the side of the bobbin and letting it ply back on itself. Am I happy with the diameter and amount of twist? If so, I spin enough to make a small sample of my intended yarn whether single or plied and finish it before evaluating. Do I want to change something? My options include tweaking my drafting method, the ratio of the wheel or the amount of fiber I have in my hand.
Finishing
I soak the skeins with a small amount of detergent in warm water, gently squeeze out the water, “whuz” it, and lay it flat to dry. I prefer not to agitate, use hot/cold rinses, or “thwack” since these methods diminish the loft of the undercoat. As the final step, I use steam to set the twist and stabilize the yarn. These yarns transform when washed! Held in place by the outercoat with a low amount of twist, the disorganized crimp of the undercoat has room to bloom, creating a contrast to the smoother outercoat. The finished diameter of the yarn will vary from fleece to fleece depending on the percentage of undercoat vs. outercoat in the locks. Yarns with a higher percentage of undercoat will be thicker with more loft.
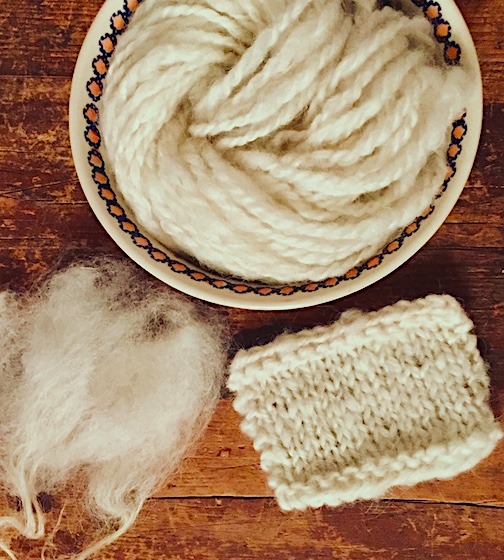
The white yarn contains a larger percent of undercoat that bloomed and shortened as the yarn dried.
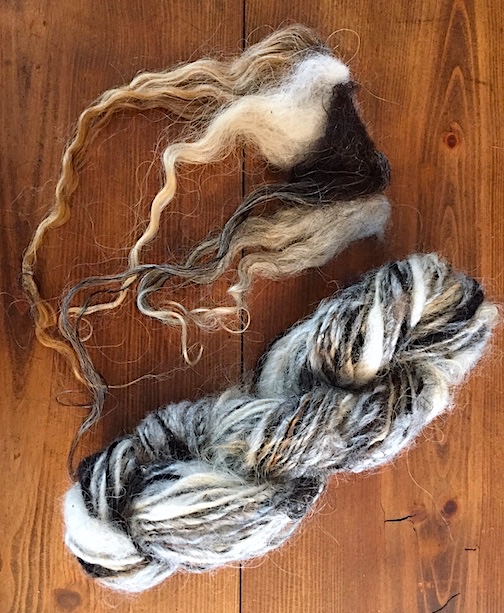
The long outercoat of the natural-colored locks was spun into a low-twist singles yarn that showcased the color variations. As the amount of outercoat increases, the denser the yarn will be. Yarns spun from the lock are individual and are a true reflection of these unique fleeces!
Donna Kay is a knitter, spinner, designer, instructor, and shepherd, often all in the same day. Her home is a farm in New Hampshire that she shares with her husband and an assortment of livestock. She spins as much as she can, teaches here and there, and designs for her company, Tree of Life Designs. You can find her on Ravelry as treeoflife.
PLY Magazine believes that Black lives matter, as well as LBGTQI+ lives. Those most vulnerable and persecuted in our communities deserve our love and support. Please be good to each other.
Leave a Reply
Want to join the discussion?Feel free to contribute!