Mixing Things up for a Sweater
words and photos by: Johanna Carter
I always admire those who are able to spin mountains of yarn for a big project, ready to knit a wonderful sweater or cardigan. It is a satisfying feeling when you finish all that work, especially if you started with washing and combing the wool or even raising your own sheep.
Mixing spinning and knitting
The typical way to work through a larger project is to spin all the singles first and ply them in a particular order so you get the yarn even throughout the whole project. I don’t have so many bobbins, but my bigger problem is that I am quite impatient and want to get on with knitting once I have an idea. And normally, my brain is full of ideas for fibre work and the limit is the time, as I am a musician and teacher. I can’t sit at the spinning wheel for a long time if I’m not on holiday, so during the school year I mostly knit, and during the holidays I can dye, spin, use my drum carder, and do lots of fibre work. The only time I was able to produce bigger quantities of yarn before I knitted them up was during the Tour de Fleece in the two years during the pandemic, when we did not go on holiday at the beginning of July.
I like to finish knitting one big project like a sweater or cardigan before I start the next one, or at least until I can’t carry it in my bag easily anymore, so I have an excuse to begin the next one. Sometimes it is good to have a second project on the go – I call it mindless knitting, where I don’t have to look very much – which I can keep my hands busy during Zoom or other meetings, which helps me listen.
Mixing colours and fibres
Usually I dye my yarn with plants which I collect in the woods or get from garden flowers. I also use cochineal and indigo, which I buy, to get lots of different colours. I really love the greens and blues I get from dyeing with indigo. I have lots of dyed wool, and all those colours give me inspiration for further projects.
Blending the wool on the drum carder I can get even more shades. I like to blend with fibres like silk, alpaca, or plant fibres, and I love sari silk, to get those little bits of colour in my yarn.
When I have an idea for the next sweater, I start carding, and then I can begin to spin. Once I have spun enough yarn – say, for one day – I cast on and start knitting, usually top down, so I don’t have to decide too much in advance about length and width.
When I spin on my wheel, I have to sit at home, but while spinning I can read a book or talk to others during online meetings. I also like to spin on my spindles, and that works on a walk, or a museum visit. I take them on holiday as they don’t need much space, and when I spin for a lace shawl, I don’t even need much wool either. At home there are spindles all over the place; I can spin when I am waiting for the kettle to boil, when the computer is slow, when I am cooking. Like that I can make good use of a short time and the yarn still grows.
I can take my knitting almost everywhere, which is why I don’t want to wait to get started until I have spun all the yarn for a whole sweater. I knit at home, on the bus or train. The only thing I have to make sure of is to be one step ahead with the yarn.
I love to knit Fair Isle sweaters. My favourite method is to use only one bobbin, which I don’t even fill, because I need smaller quantities of lots of colours. Then I wind a ply ball and ply it on itself. For that I put my thumb through the ball, so I can tension the two singles with my fingers and they don’t get tangled, as long as my thumb (or a cardboard roll or a pencil) stays in the middle. I don’t have any leftovers from plying, and it is quick when I suddenly need more yarn.
I have never had problems with the yarn not being consistent enough throughout a project. I just know what yarn I want and my fingers seem to remember what to do. I am sure it is good advice to have a little card tied to the spinning wheel with a bit of the singles you are aiming for, so you can check and make sure you are spinning a consistent yarn.
Mixing breeds
There are so many different breeds, but some of my favourites are Shetland, BFL, and Jämtland – a Swedish breed. After dyeing them, I often forget what I have used, so when I do a new project it often turns out that I have used different breeds and fibres just to get the right colour. For the Fair Isle knitting I want to juggle lots of colours, which is more important to me than making a sweater out of only one breed.
Recently I made a pullover for my husband using about 12 different breeds and colours, even mixing short and long draw. For me it was a breed experiment and a way to use up lots of smaller quantities of wool I had in my stash. For that sweater I used combed top without blending.
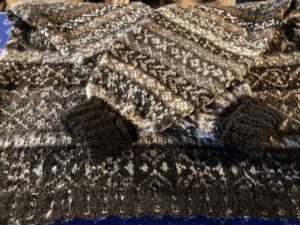
Mixing in knitting during the spinning process is a wonderful way for a spinner to avoid being overwhelmed during a sweater project.
My feeling is that some people don’t dare to start spinning for a bigger project because they get overwhelmed by the quantity they have to spin and then all the knitting there is to do, especially when you want to spin the yarn entirely on spindles. Mixing the spinning and knitting for the same project is more interesting; you get more variety and more freedom to choose what you want to do next as long as you don’t run out of yarn. It breaks the project down into smaller, less daunting parts. The only thing you might want to plan is to have enough fibre at the start, but even that is not necessary, there is always a sheep growing more wool.
Mix Tape for the Modern Urban Spinner
by Andrea Deck
In 2020, we mixed up the fiber festival to become more accessible, more community driven, and more modern than we’d ever been before. Working with social media in new ways, shepherds, dyers, vendors, and spinners alike had to create a new mix of a truly ancient craft and a modern, uber-connected world. Many of us hunkered down from our in-person fiber festivals and started to think about what it would look like to connect digitally.
Come Together (The Beatles)
While the social nature of fiber farming and making beautiful fiber creations is deftly woven into the story, so many of those relationships are based on proximity.
Welcome to the Internet (Bo Burnham)
This transition to the online space was far from new, but many of the most adept at Ravelry and social media were far removed from the production side of the fiber experience. Many small businesses, shepherdesses, and farmers operated entirely in person, selling at small fiber festivals in their area. As you may know, this missing link in the supply chain led to quality wool producers around the world converting beautiful fleeces to fertilizer or trash throughout the pandemic. When Maryland Sheep and Wool, PLYAway and other big national festivals shuttered their physical doors in 2020 to weather the storm, business owners and fiber artists alike flocked to social media. Facebook groups and Ravelry threads were lighting up in new ways to combat isolation and fear but also to ask the very real question “what now?”
Empire State of Mind (Jay-Z)
Living as a City Mouse in a postage stamp of an apartment has a few major drawbacks: price, space, and all my local supplies of yarn or goodies are either very corporate or very expensive. If I was looking for a full fleece or anything that still smelled like a barn, I was headed out to fiber festivals hours from my home. I already had experience scouring the internet for economical resources and shops I’d heard of or seen on festival websites. I was adept at buying hand-dyed yarn from websites older than I was with terrible color photos and worse descriptions, then waiting weeks or months for my squishy mail to arrive.
So by the time the pandemic hit, I was in the right place (already working remotely and adept at finding fiber online) at the right time (my city and work changed dramatically and quickly) to be a part of reimagining the festivals online. I went from the fringe of the fiber community, with no space for sheep or capacity to design new things, to building documents and best practices for transitioning that community online. What lighting were we using for professional social media videos? What network capabilities were needed to live stream? How do you deal with taxes and shipping around the country?
The communal aspect of the craft came to the fore early: join an online festival as a vendor and be welcomed into a league of small businesses learning to survive online. Places like VirtuWool and Wool and Fiber Arts groups offered mentors, weekly check-ins, and volunteers to help run live sales, as well as feedback on your web platform and performance. Need a few hours of professional help? Head to the group to find a contractor who also happens to love wool. Community groups developed codes of conduct, new folks were welcomed by moderators, and excitement buzzed long before and after any individual sale.
As webinars on ad words and stabilizing rural Wi-Fi popped up alongside new online fiber festivals, sales, classes, and more, a whole new audience also emerged. As accessibility into these spaces grew, so did the diversity of both the buyers and sellers. Folks continued to show up: new and older generations of crafters, people facing isolation for a wide variety of reasons, the “fiber curious” who had only bought a ball of yarn at Target. If there is one big takeaway from this crazy time, it’s this: the lowering of all sorts of barriers has made our fiber festivals, and our community, stronger, more creative, and more diverse.
Re-emergence: As we re-emerge, let’s take a look at what we’ve learned and how we’ve connected to create a new mix tape of our favorite tunes. For my personal jams, I’m trying new songs to use my distance from the sheep in the field to develop new tools to engage with the fiber community and using my personal, introverted hobby to connect more broadly across the world.
See You Again (Carrie Underwood)
Return to in person festivals can’t mean an abandonment of the online groups and communities we’ve found so much value in over the past two years. These novel ways to engage in the things we’ve done for centuries is part and parcel of the future and history of fiber craft. My biggest fear is after building infrastructure and community in new online spaces for over two years they (and we) will be abandoned for the in-person meet ups again.
Meet Me Halfway (Kenny Loggins)
How to hybrid? For me, I’m about to embark on a shlep back to my favorite festival, and while I’m so excited to be back in person, I’m also feeling very alone. This is the first festival where not one of my Ravelry or online groups is getting together. The stitch marker swap that has happened for years has fallen apart. It is up to us as artists, community members, festival organizers and attendees, and voices across our fiber community to take the best songs we learned during COVID and keep playing them. The in-person event space has long asked questions about what it means to feel welcomed or to feel like we belong, and there’s a ton we learned as strangers online that we can bring with us! There’s room for all of us and more at these festivals and in our community, because it’s an awesome place to be.
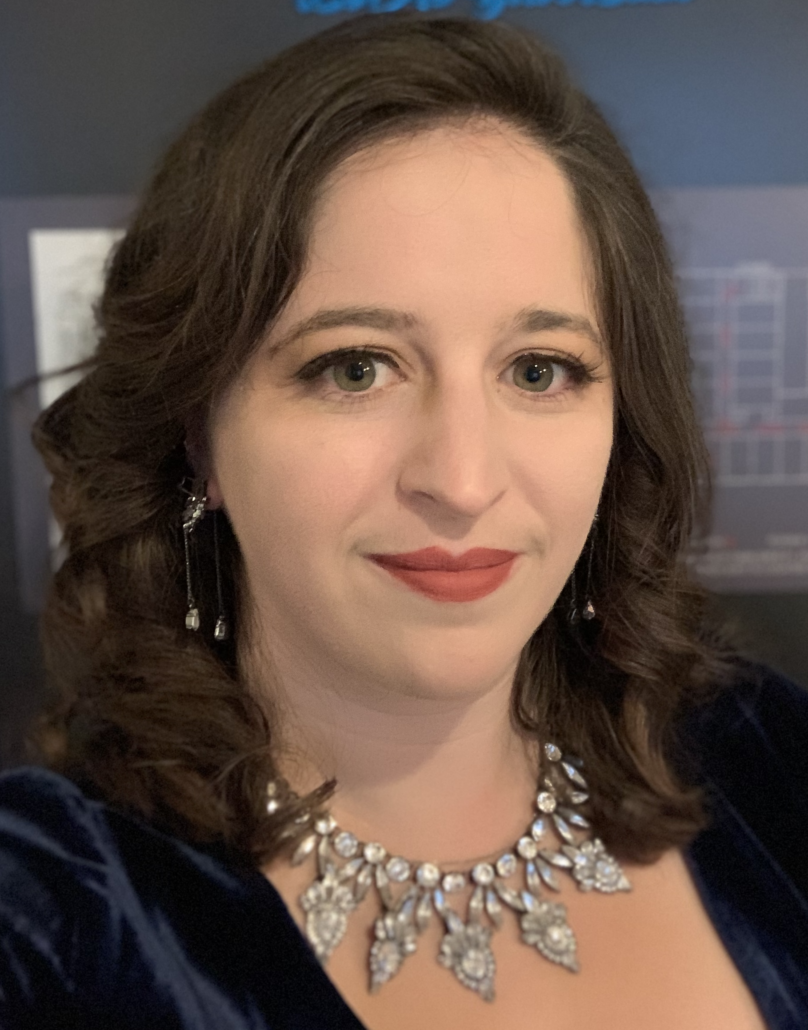
Andrea Deck (@craftondeck) is a spinner, weaver, knitter, and lover of fiber living in the heart of DC with her husband and huge yarn stash. Professionally, she is a community builder specializing in engagement of young adults, couples, and you.
PLY Magazine believes that Black lives matter, as well as LBGTQI+ lives. Those most vulnerable and persecuted in our communities deserve our love and support. Please be good to each other.
Did you know we also have a monthly PLY newsletter? Sign up here!
Did you know we also have a monthly PLY newsletter? Sign up here!
A Knitter’s Tour of British Breeds
words by Karen Robinson | photos by Karen Robinson unless otherwise credited
I have been on the most wonderful adventure – a tour through the southwest of England focused on various sheep breeds in the area. The tour was hosted through Rowan Tree Travel, and for over 10 days, a group of 16 travelers plus 2 tour guides and 1 bus driver explored many delightful paths and sites.
Almost all of our group arrived a day early, which we spent in Bath at a hotel near Bath Abbey. We were on our own this day, so I walked around the city and explored some of the historical sites as well as the shops (including several bookshops).
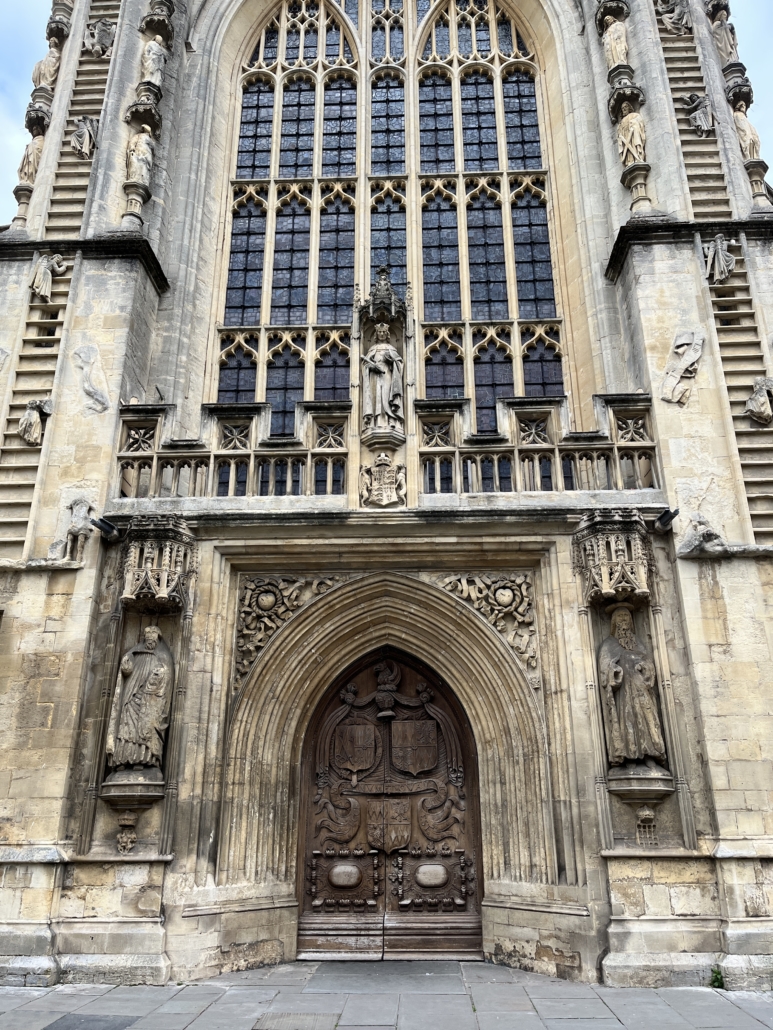
The next day we were on our way bright and early to our next destination, Pickwell Manor Farm, where we were going to stay for three nights as we explored that area in Devon. Along the way, we had a brief stop at Hestercombe House & Gardens to stretch our legs through the gorgeous grounds.
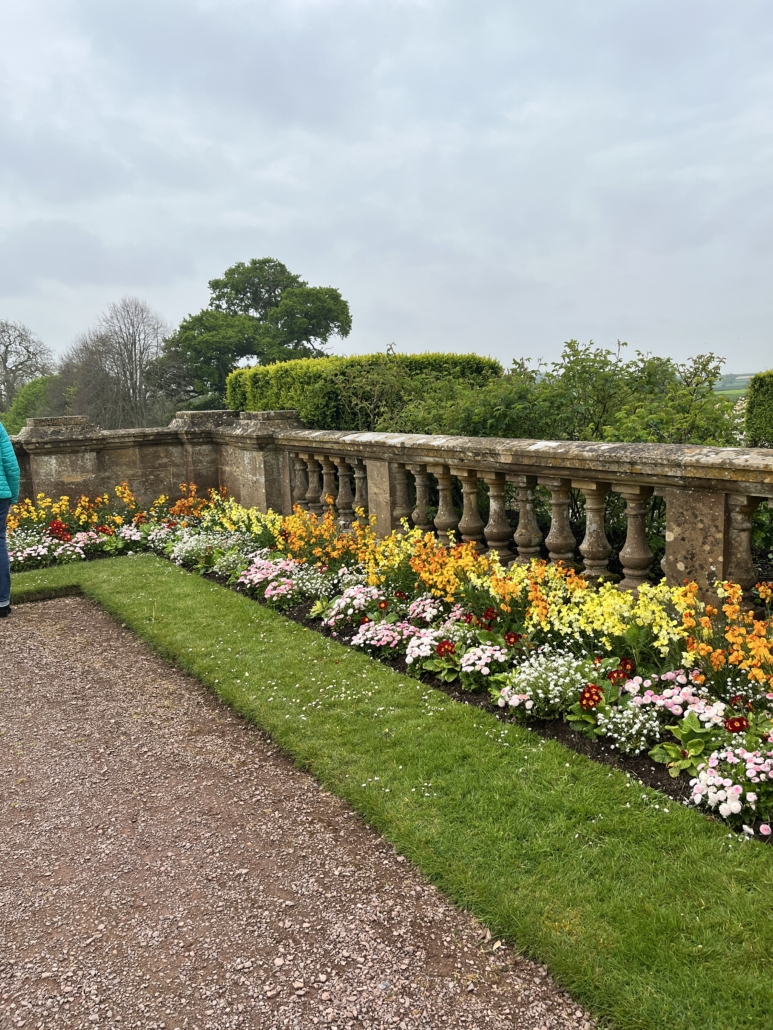
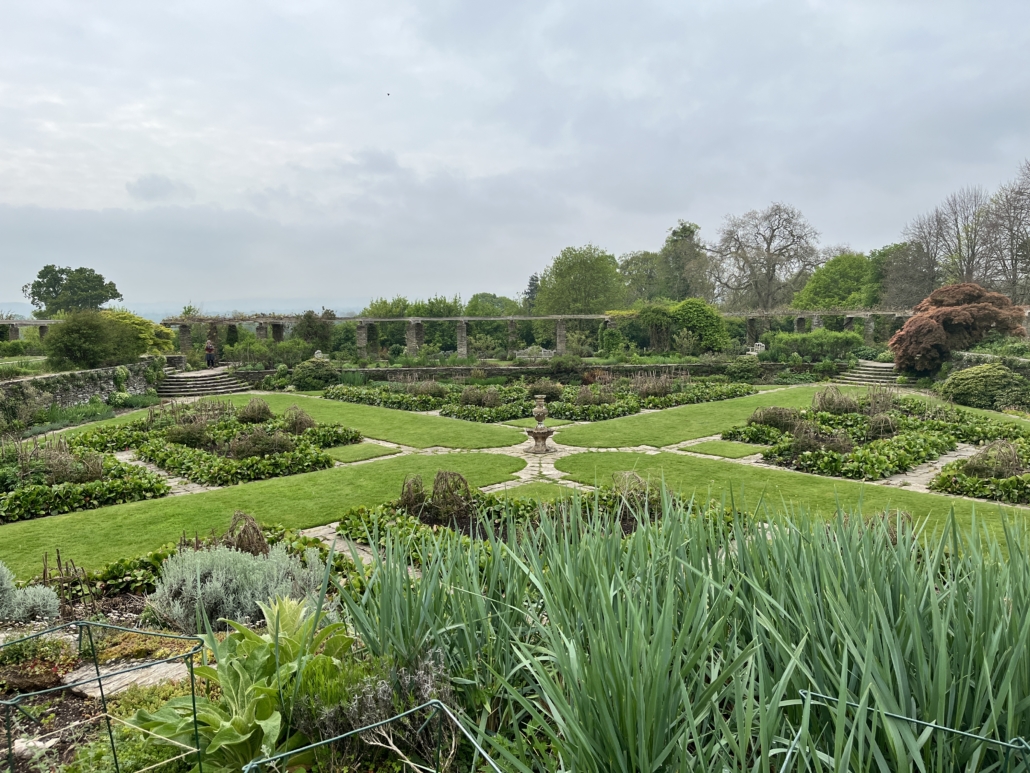
Once we reached Pickwell Manor, we jumped right into our first workshop on British breeds and learned how to felt. Our project: a sheep of course! And we got to use some of those breeds we had been talking about. It was a lot of fun to see all of our creations come to life and to get to know one another through the course of the workshop.
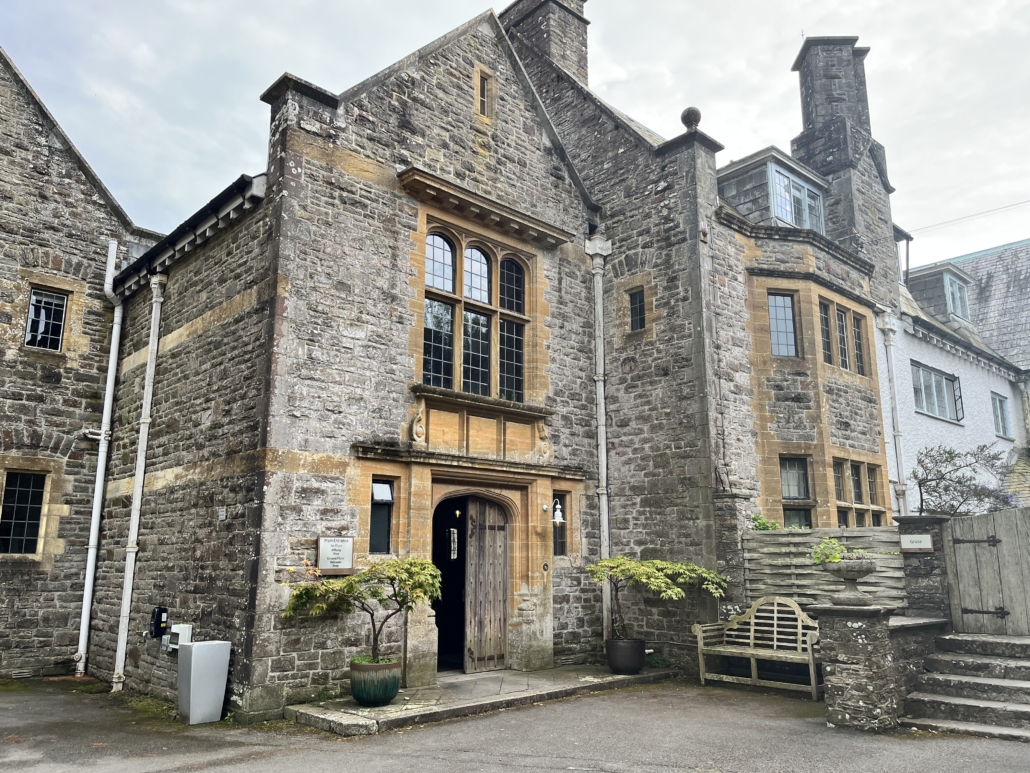
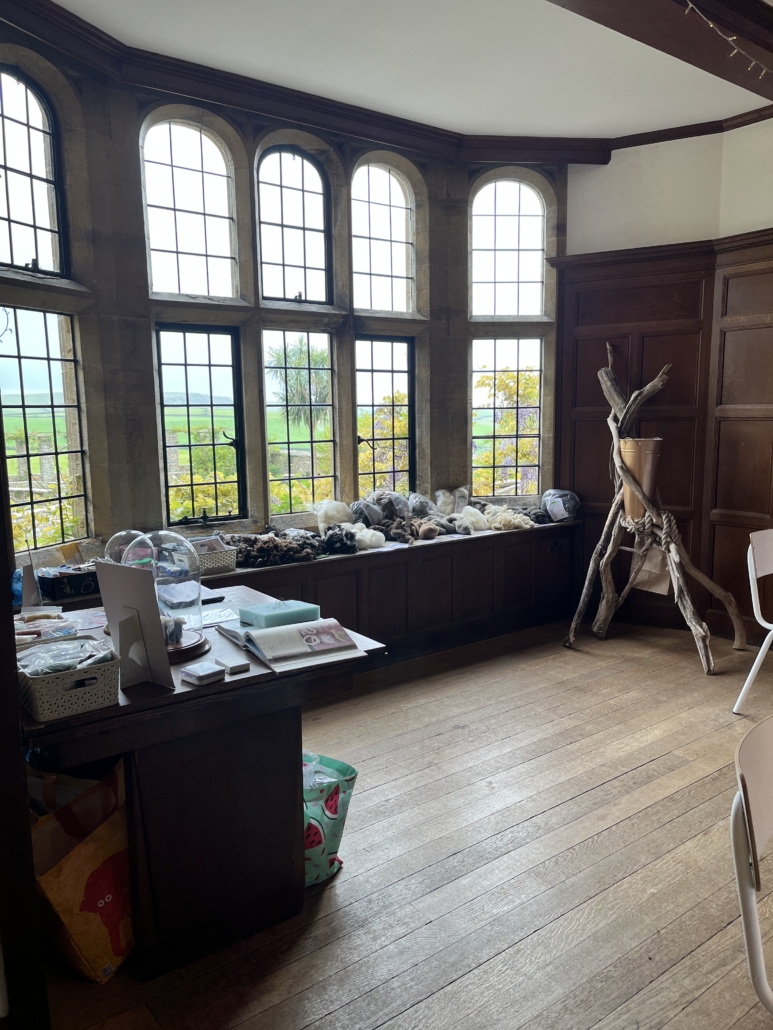
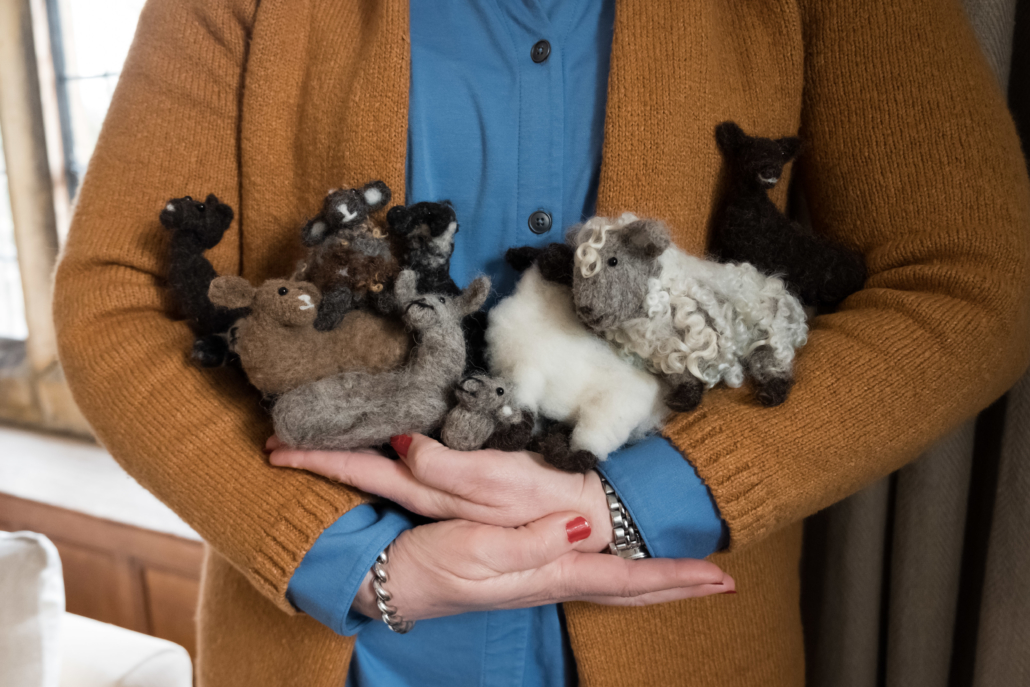
The next day included a morning talk about various sheep breeds as well as a walk along the beach near Woolacombe and stops in a couple of small seaside villages. That evening, we had a special treat: a sheep dog demonstration and headland walk with David Kennard and his Border Collies. First, he had one of his dogs work the sheep in an enclosed area, and then we walked out and up (it was quite a climb!) and watched two of his dogs work the sheep down below us. I was amazed at how well the dogs could hear the whistle and commands even though they were so far away.
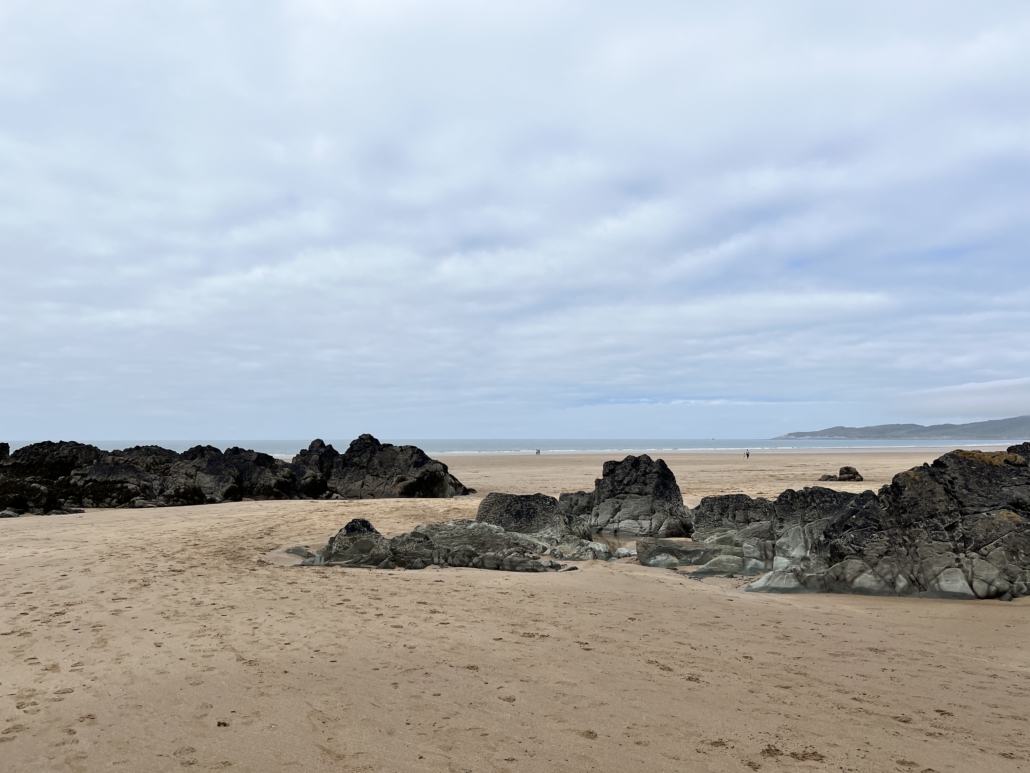
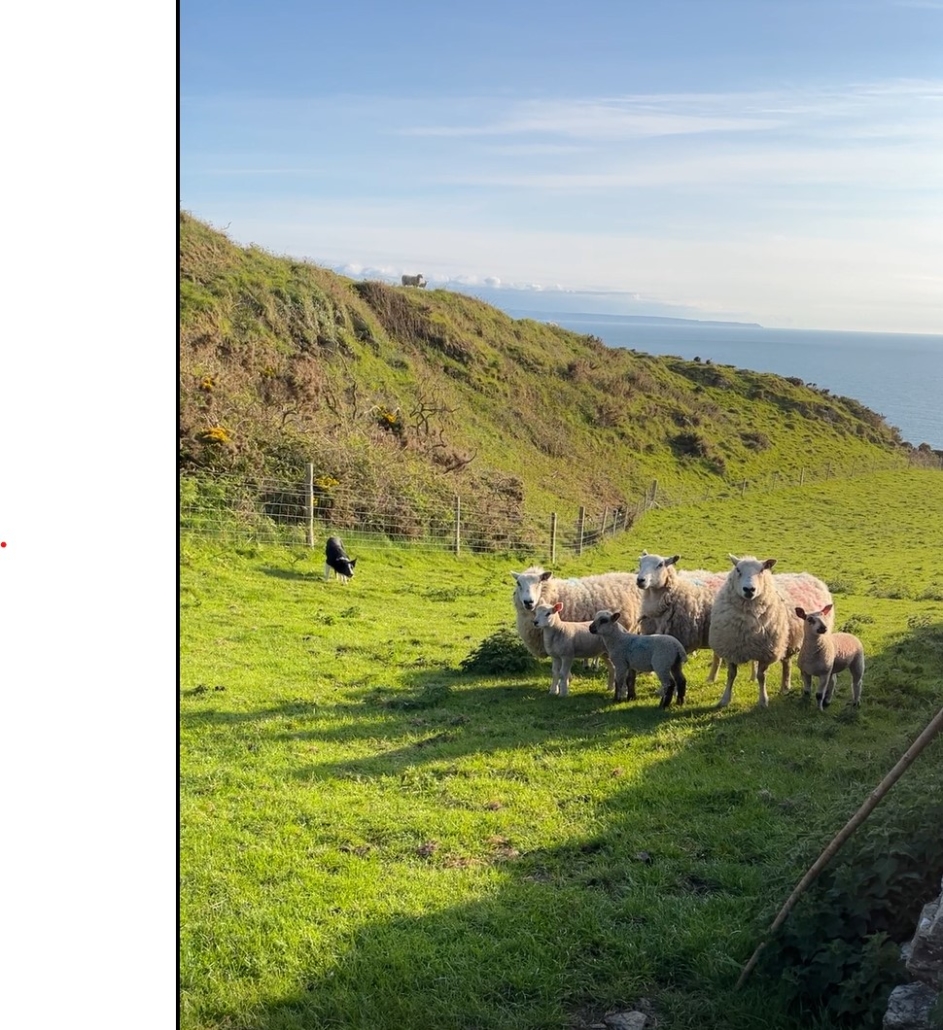
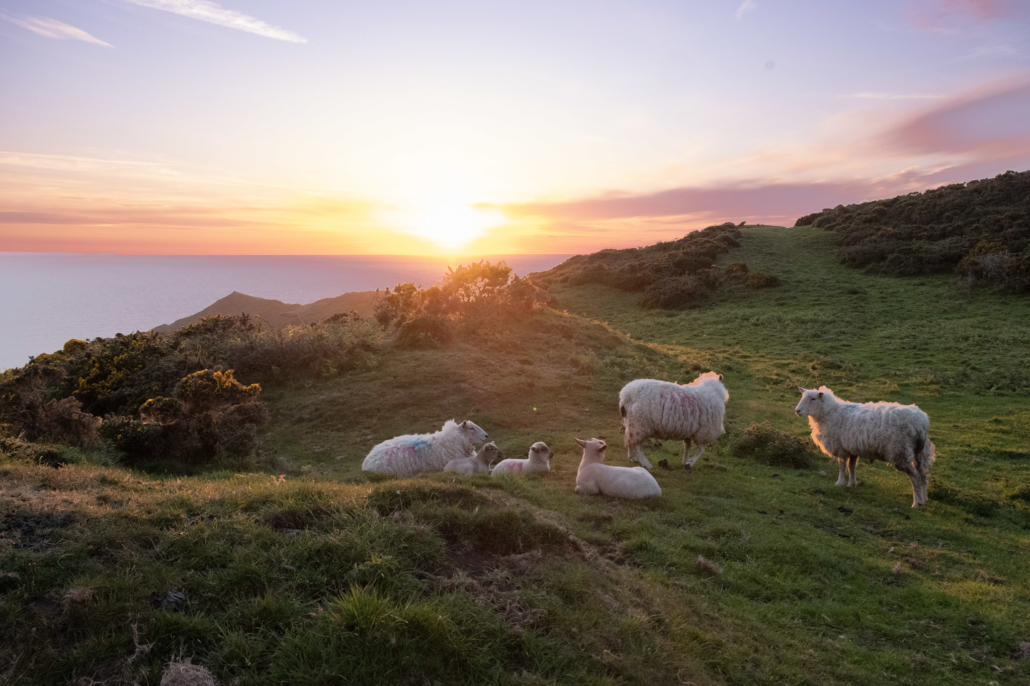
We spent the next morning driving to the towns of Lynmouth and Lynton, stopping along the way for a lovely walk through the woods in search of bluebells (which we found only a few but found wild garlic aplenty!). We got to take a railway car up the cliff and at the top had cream tea and scones (delicious!).
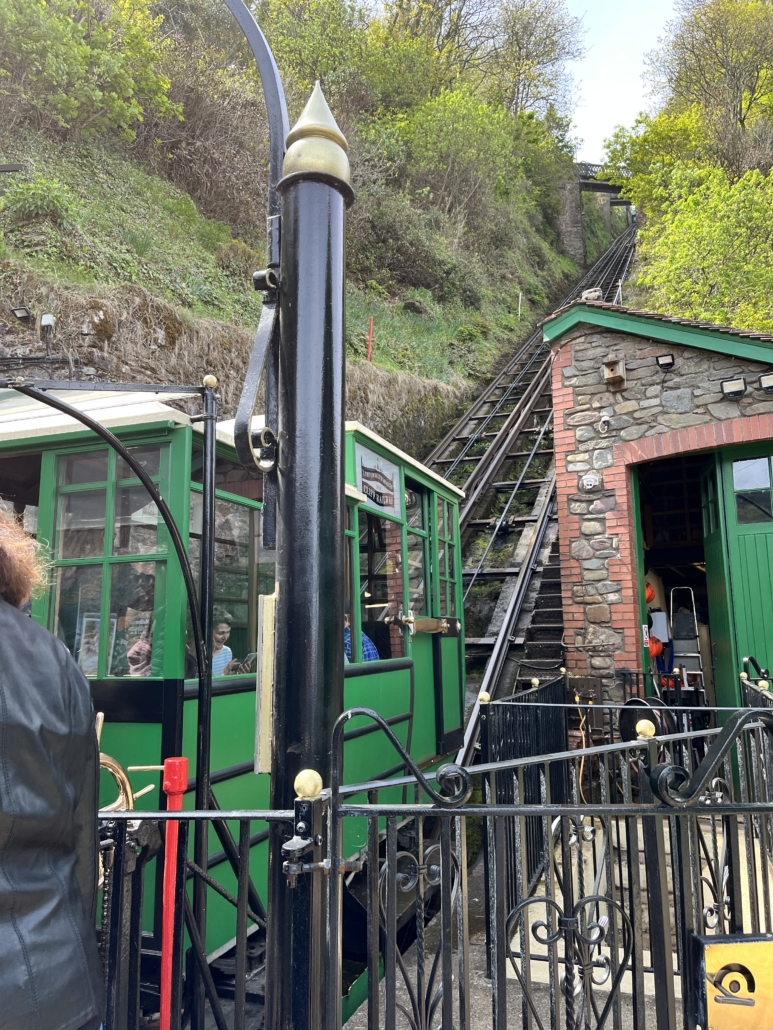
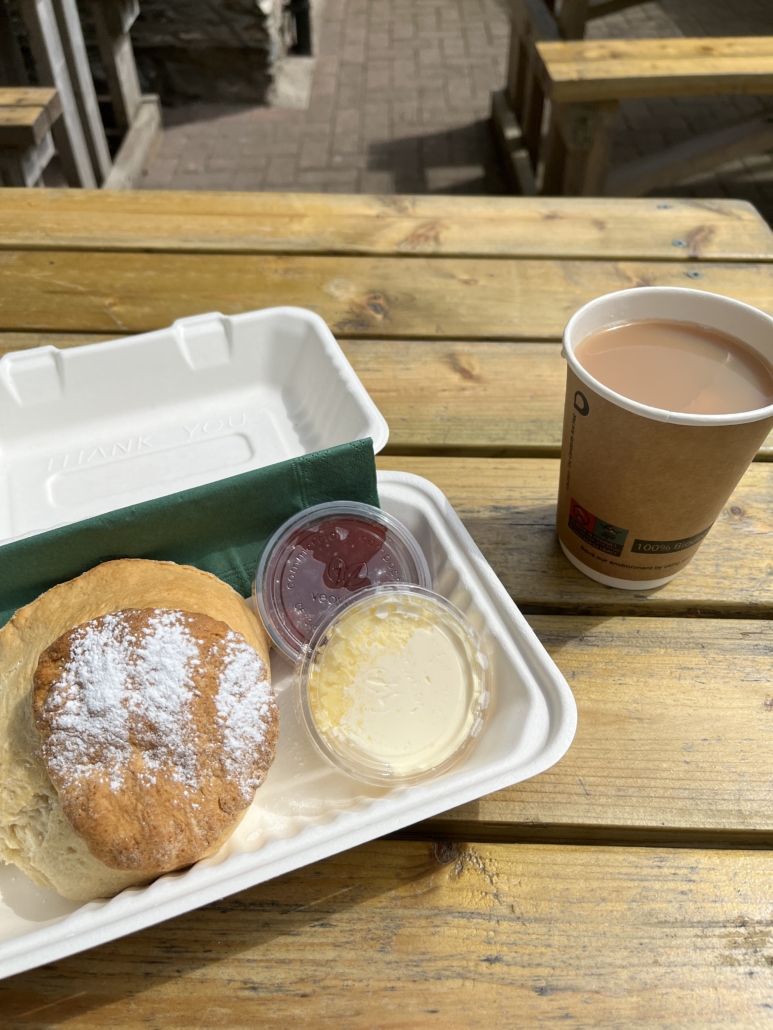
That afternoon contained a truly wonderful experience. We got to go to the John Arbon Textiles Mill and meet John Arbon and his team, take a tour through the mill to see the whole process they go through in making fiber and yarn, and do some shopping! The fiber content available was so different from what I’ve experienced before so I, of course, had to take some yarn home (I won’t admit how much!). For example, the Devonia yarn contains Exmoor Blueface, Devon Bluefaced Leicester, and Devon Wensleydale. Or the Exmoor Sock Yarn, which is a blend of Exmoor Blueface, Corriedale, Devon Zwartbles, and nylon. Although it was a great experience to see the mill and yarn, even better was the true enthusiasm from John and his staff for using local British wool and creating gorgeous yarn and fiber.
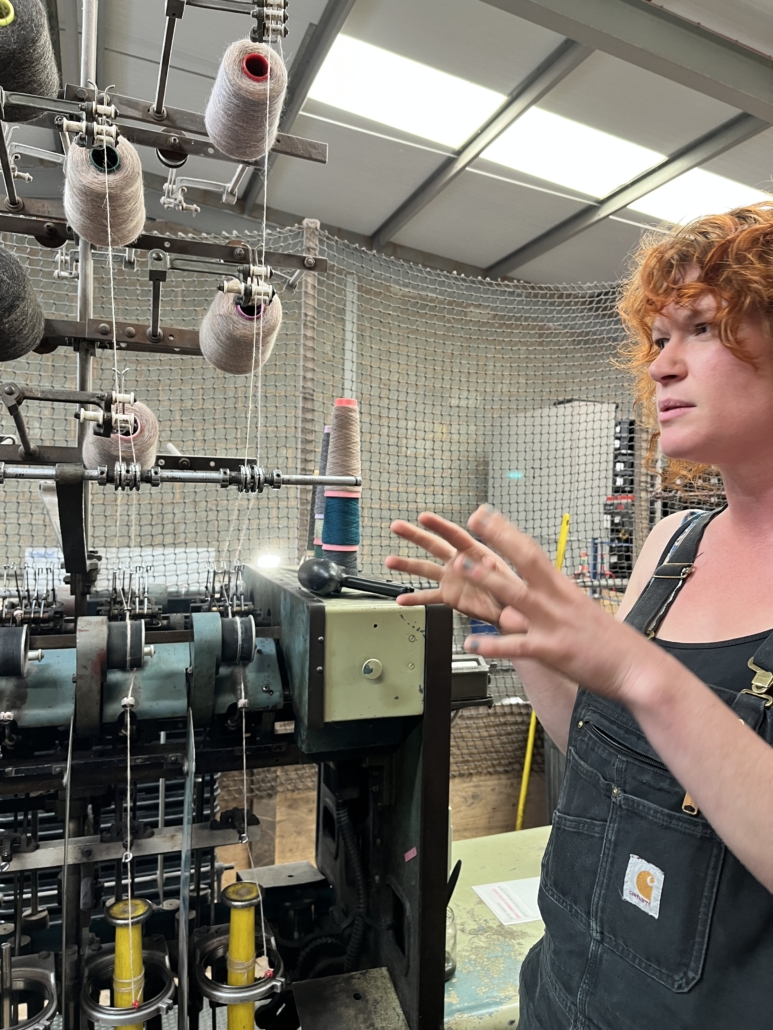
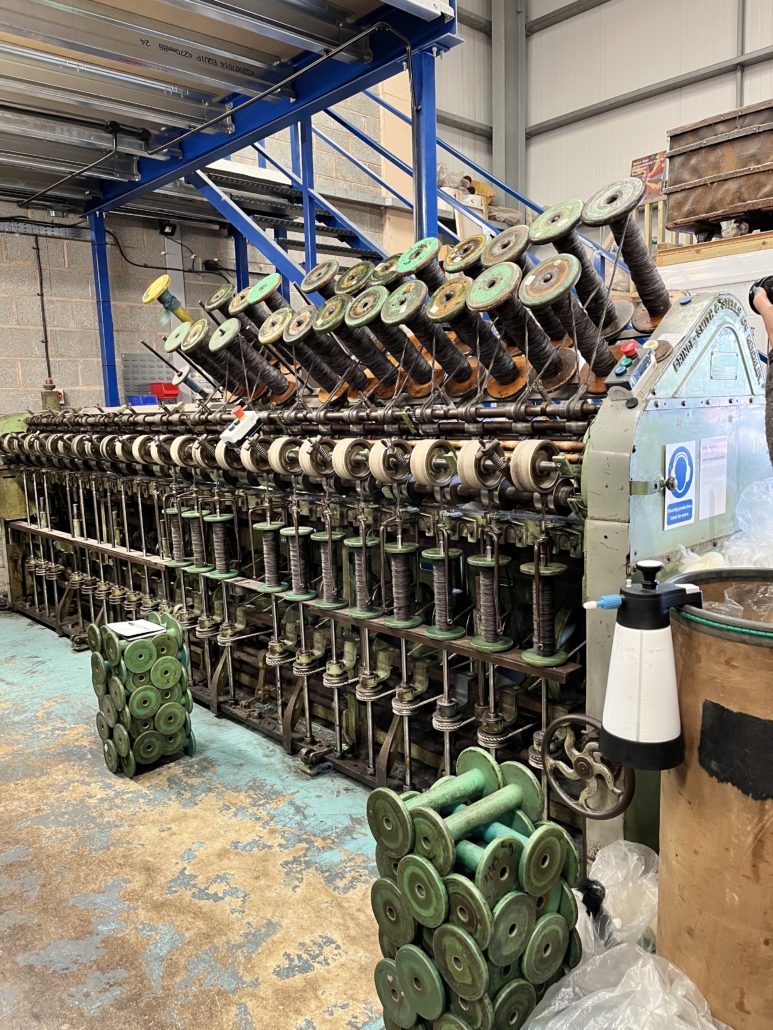
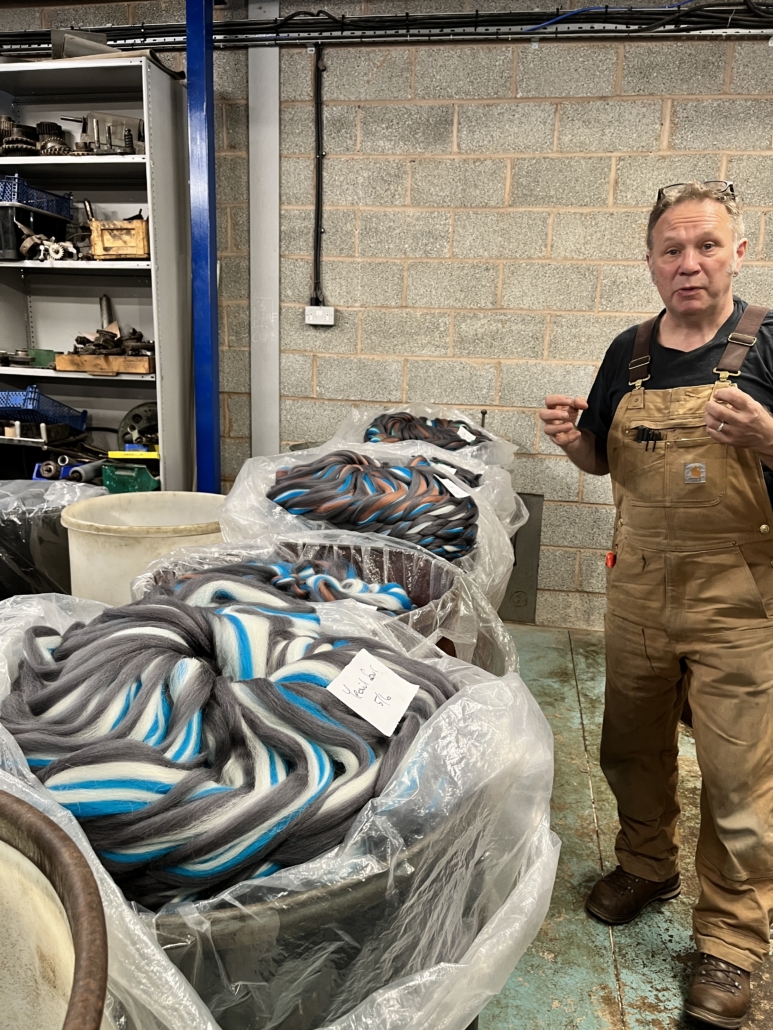
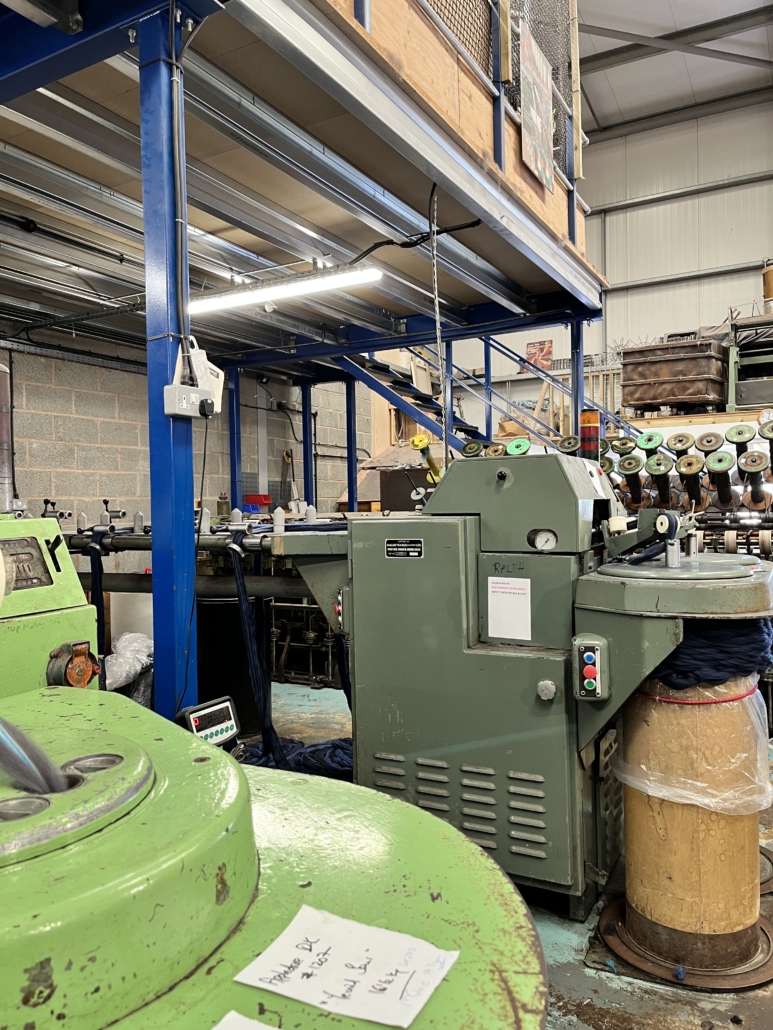
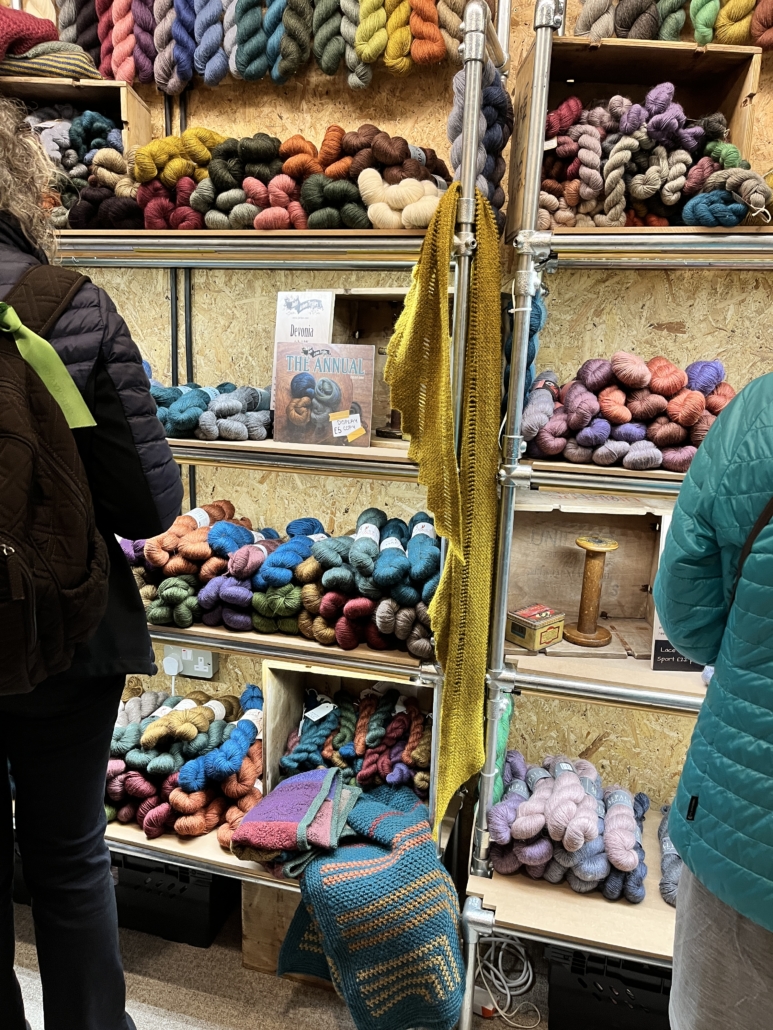
The following day was one of my personal favorites as I got to check off a bucket list item: visiting the ruins of Tintagel Castle. (My background is in Arthurian literature, and it’s the place in the stories where Arthur was conceived.) We got to climb through the ruins with a breathtaking view of the sea all around, an experience I will never forget.
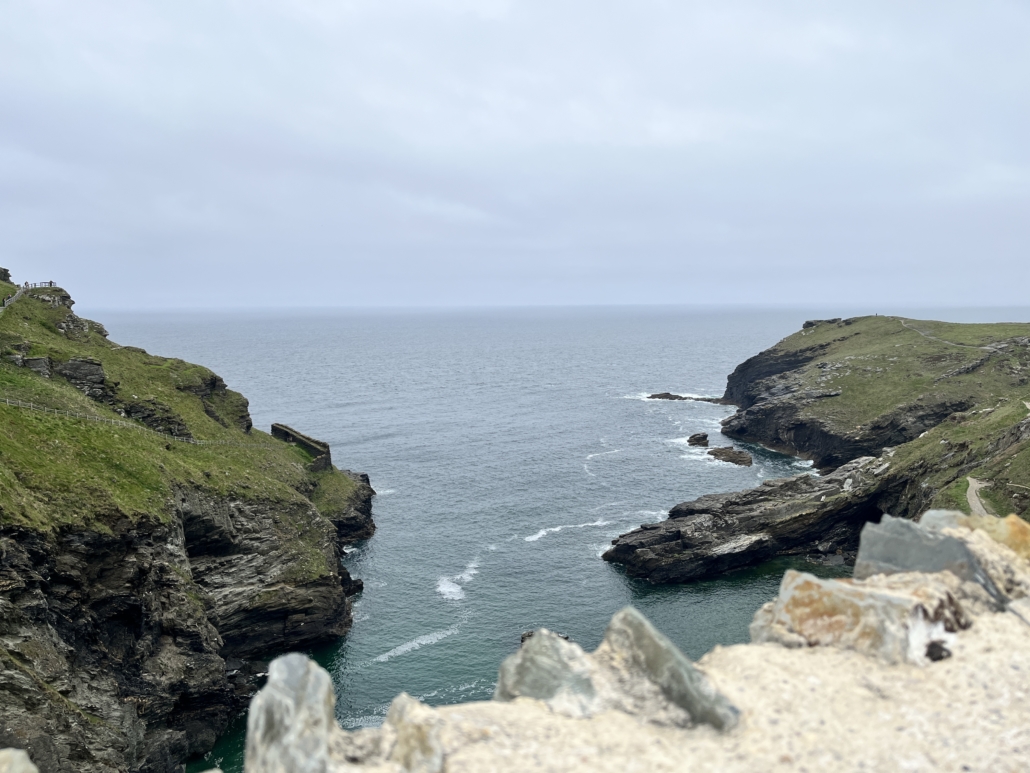
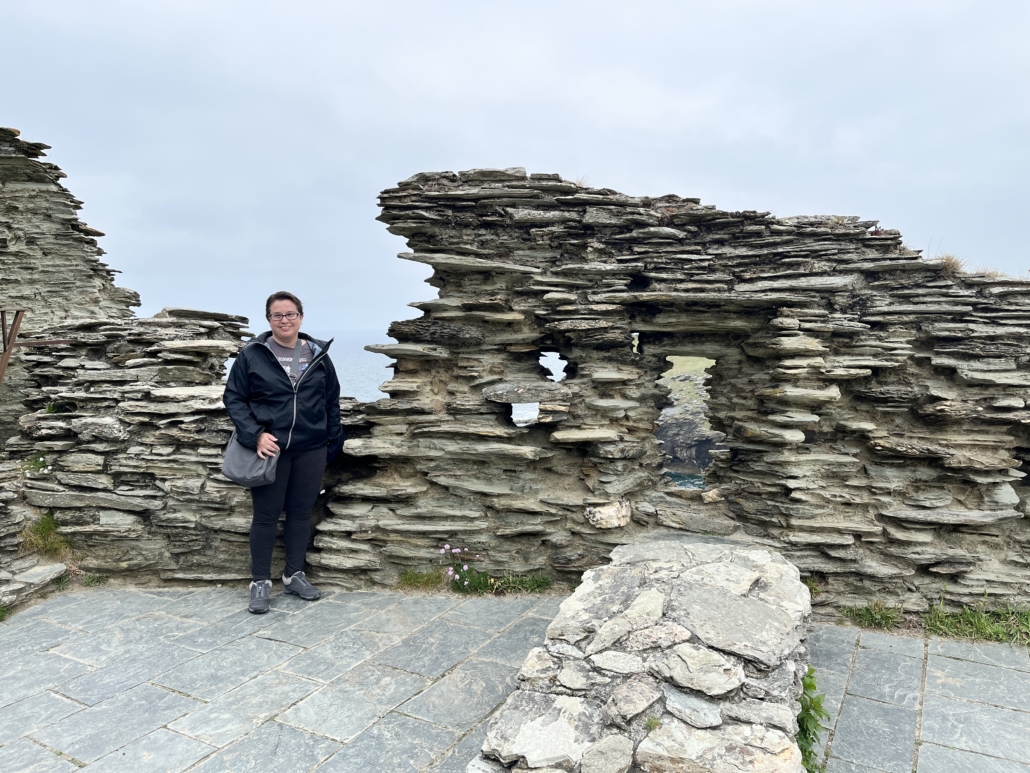
That afternoon took us to Saint Michael’s Mount, which is on a stretch of land that becomes an island at high tide (so we had to walk back across the causeway before the tide changed!). Once again, it was quite a climb to get to the castle, but it was worth it. And my room in the hotel (where we stayed two nights) had a perfect view of the castle and I enjoyed listening to the sea as I fell asleep both nights.
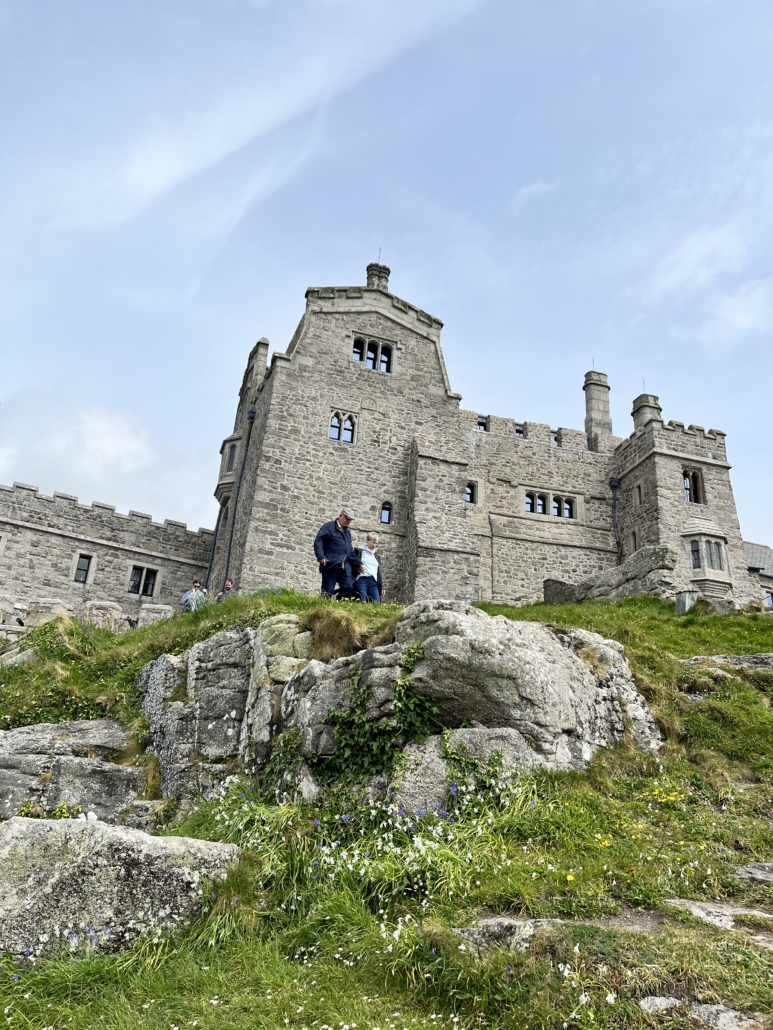
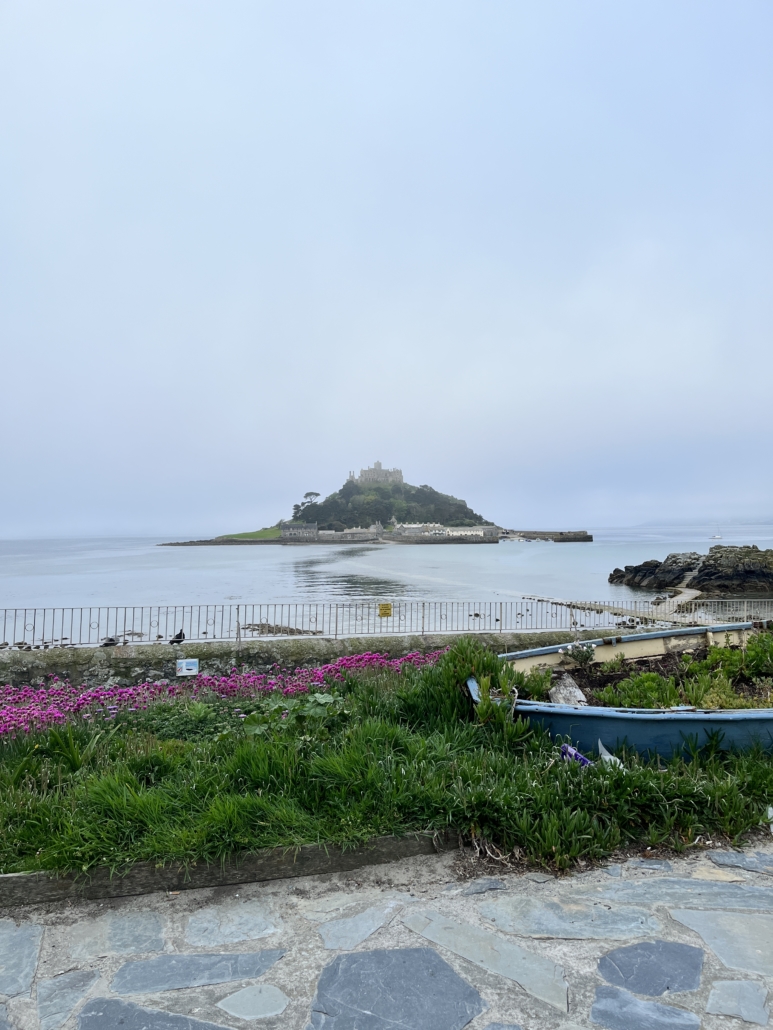
Another workshop on the next day, this one on the history of gansey knitting as well as a trunk show of Frangipani yarns and naturally dyed yarns from Caroline Bawn (daughter of the owners of Frangipani).
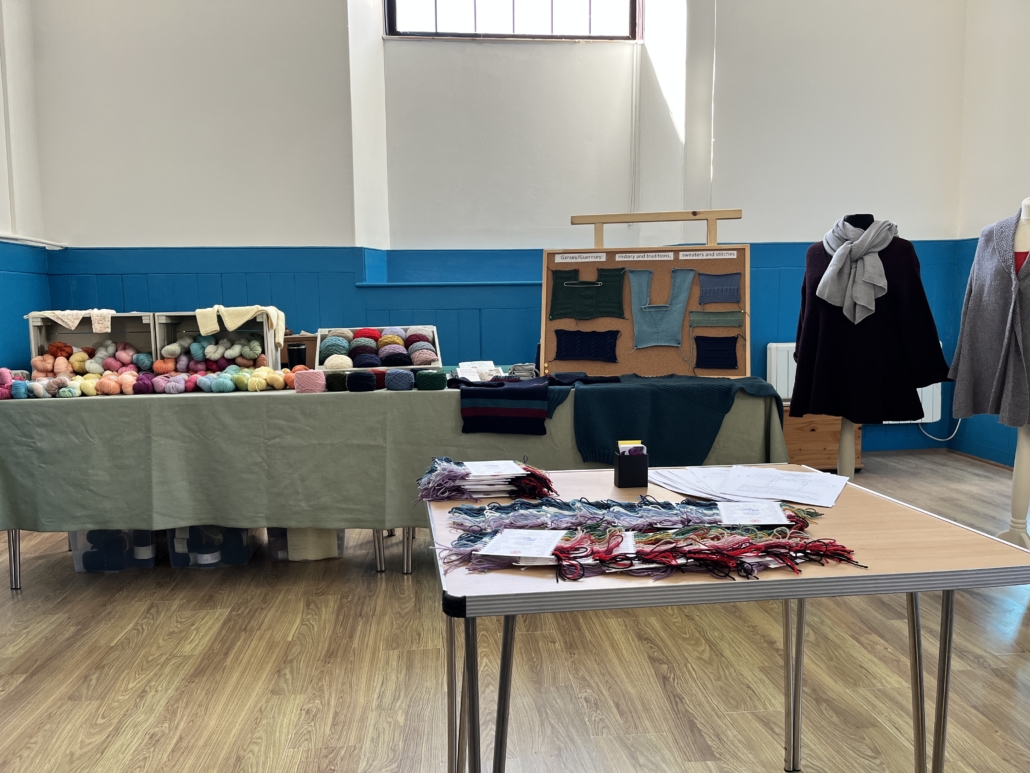
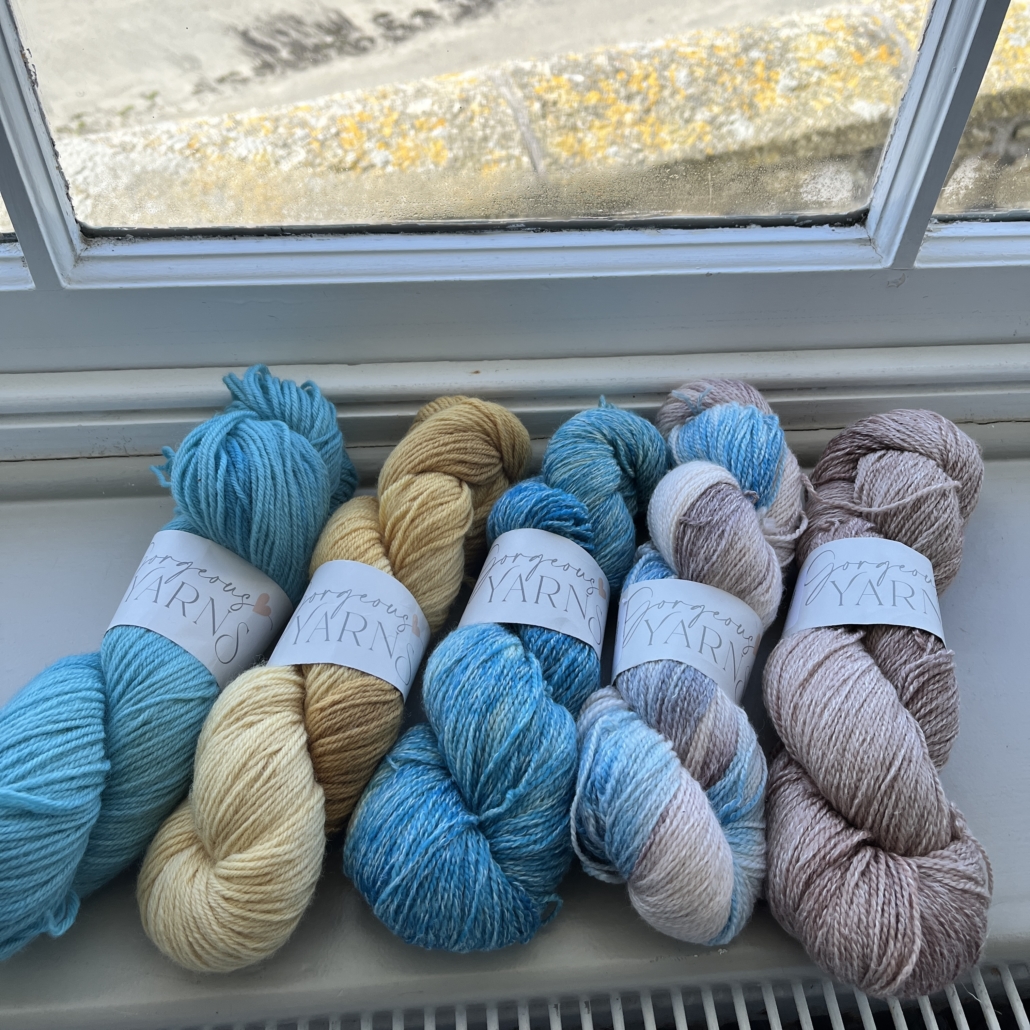
That afternoon we went to the seaside town of St. Ives where I had a delicious Cornish pasty and did some shopping. We even found a small yarn shop! We did some more sightseeing on the way to our evening destination, stopping at the ruins of a Romano-British village called Carn Euny and a stone circle called the Merry Maidens.
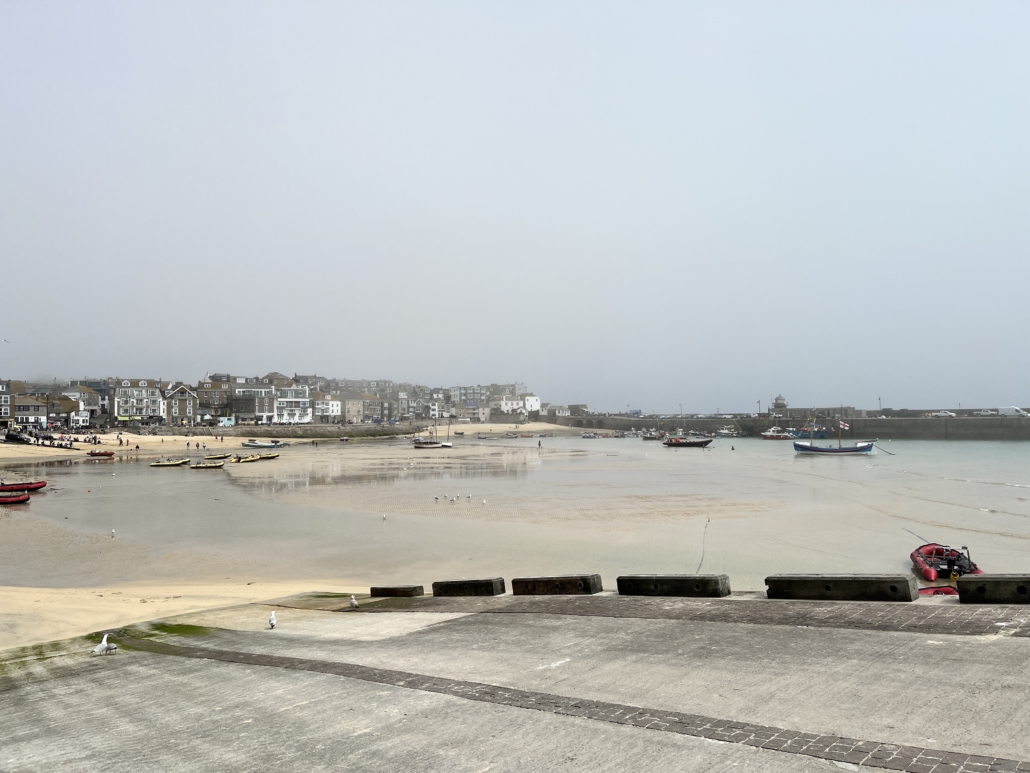
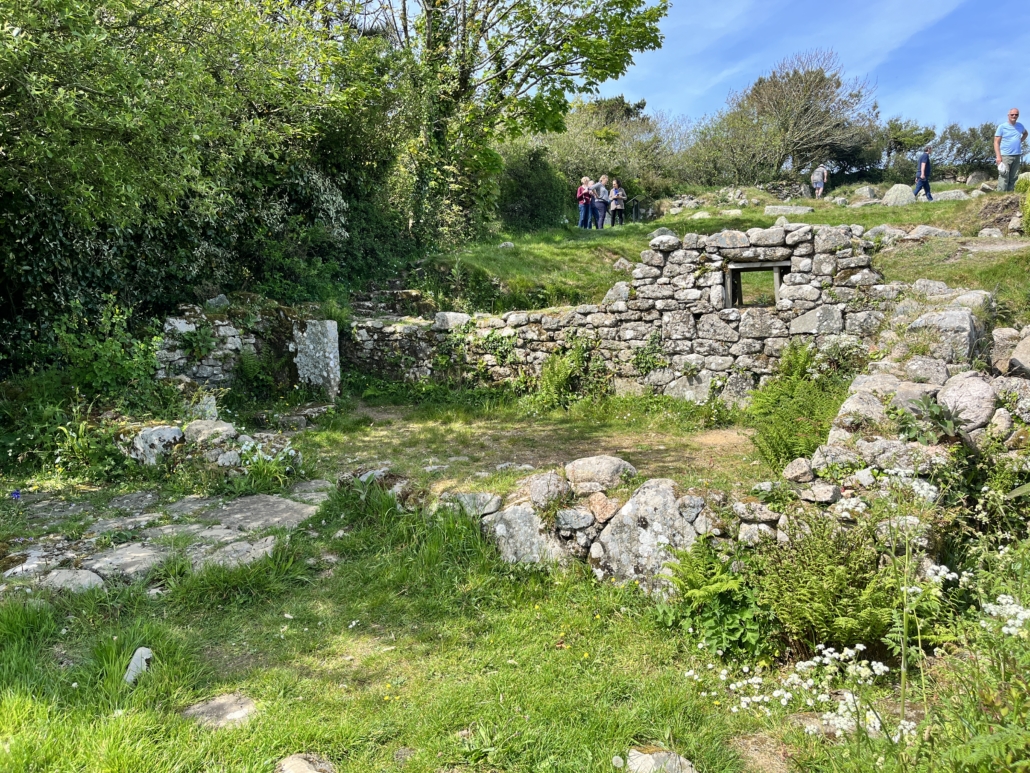
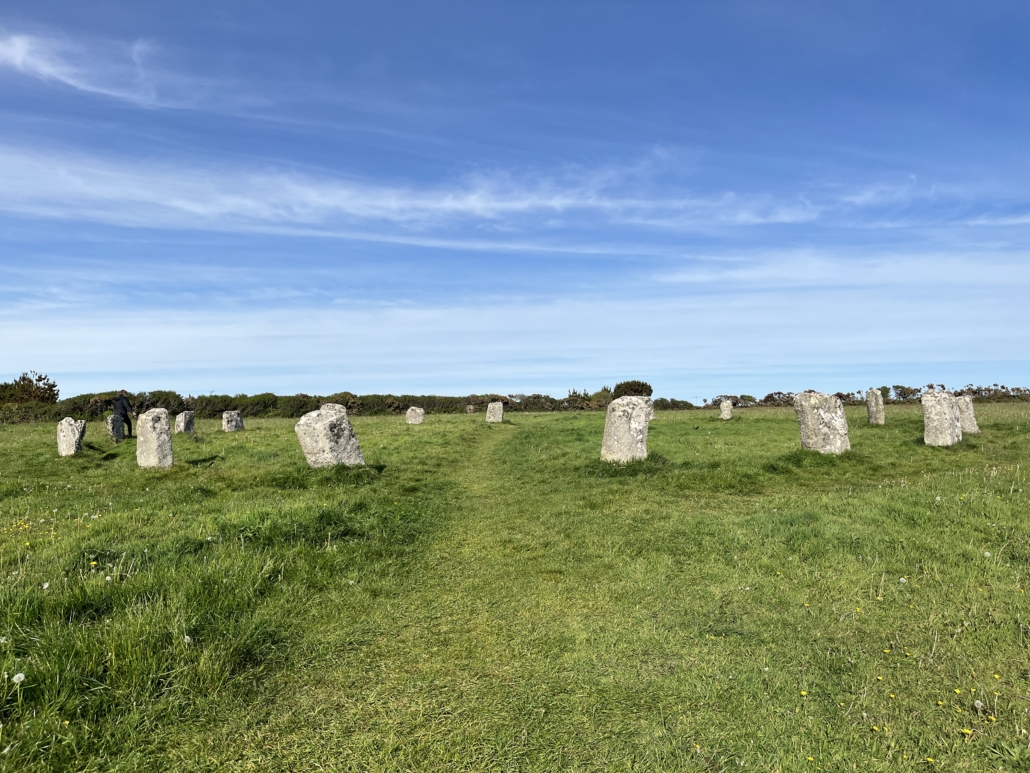
That evening, we went to the Minack Theatre, which is on the edge of the sea and features stone benches and grass terraces, to hear a women’s choir perform.
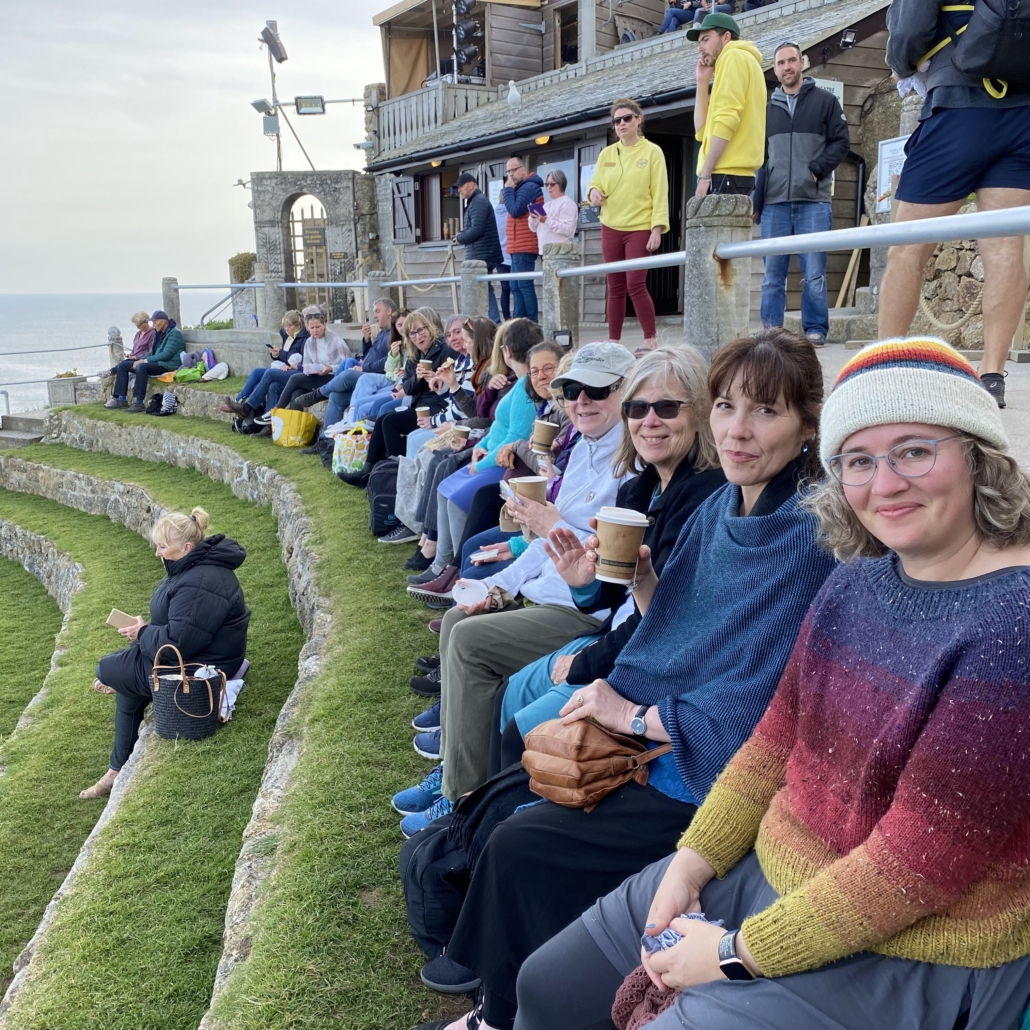
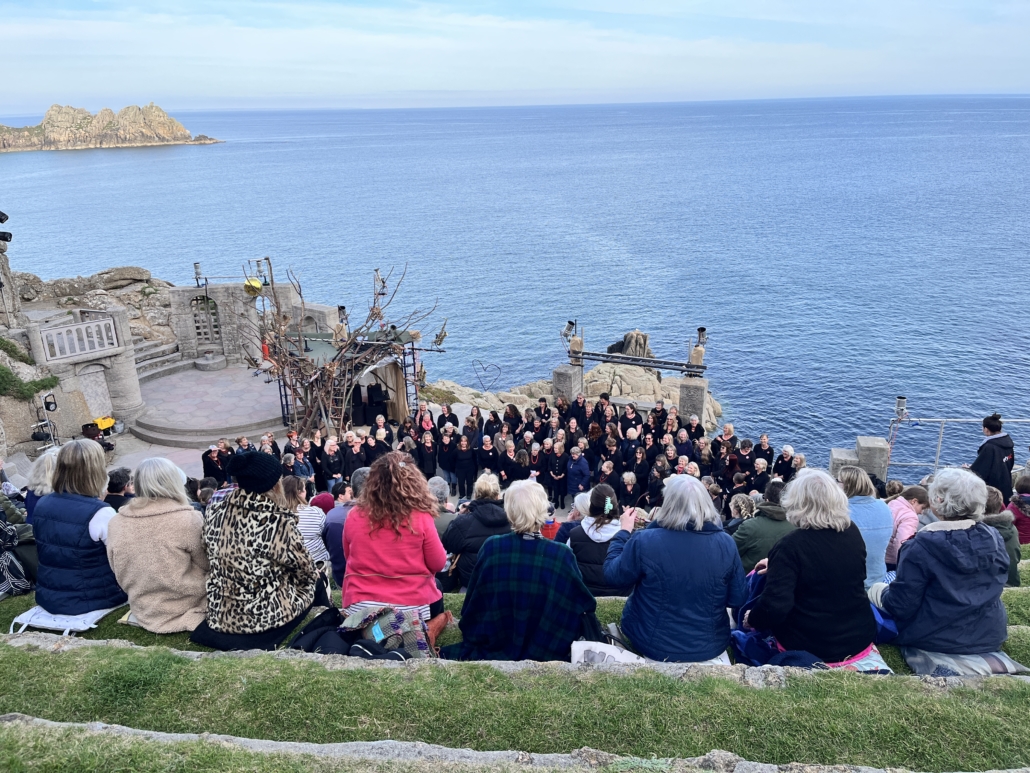
Off to the Lost Gardens of Heligan and the country home of Agatha Christie the following day. The gardens were incredible. They had been forgotten after World War II and went undiscovered for about 80 years before they were cared for again. The plants and trees, including tropical varieties which thrive in that particular climate, were huge.
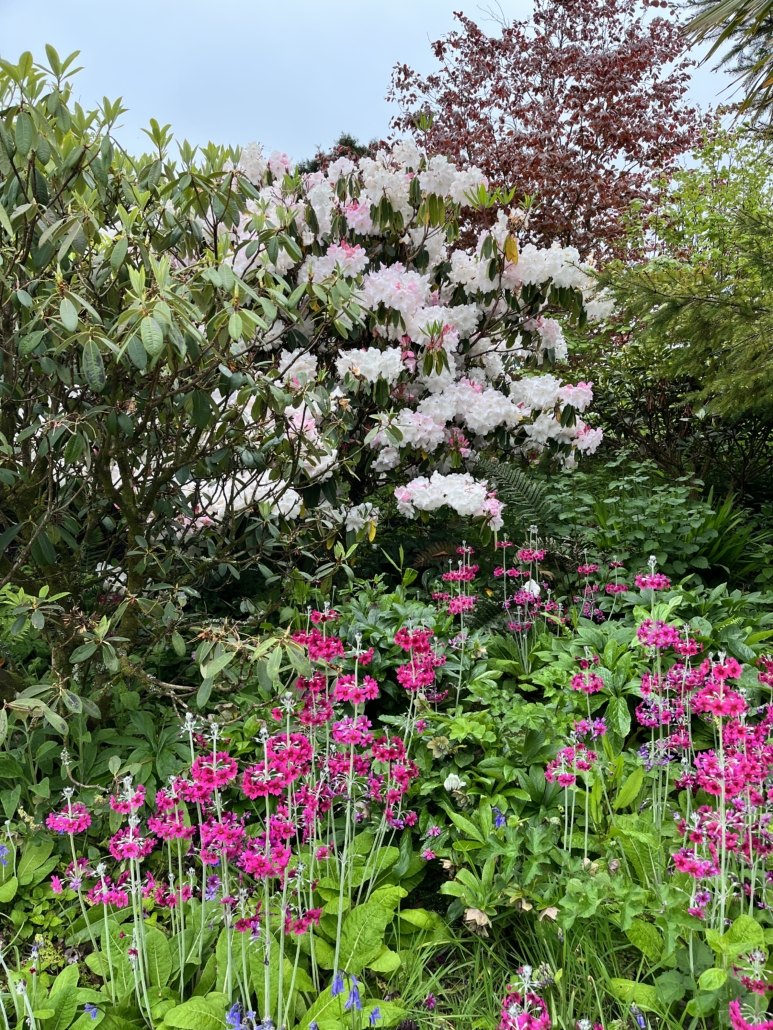
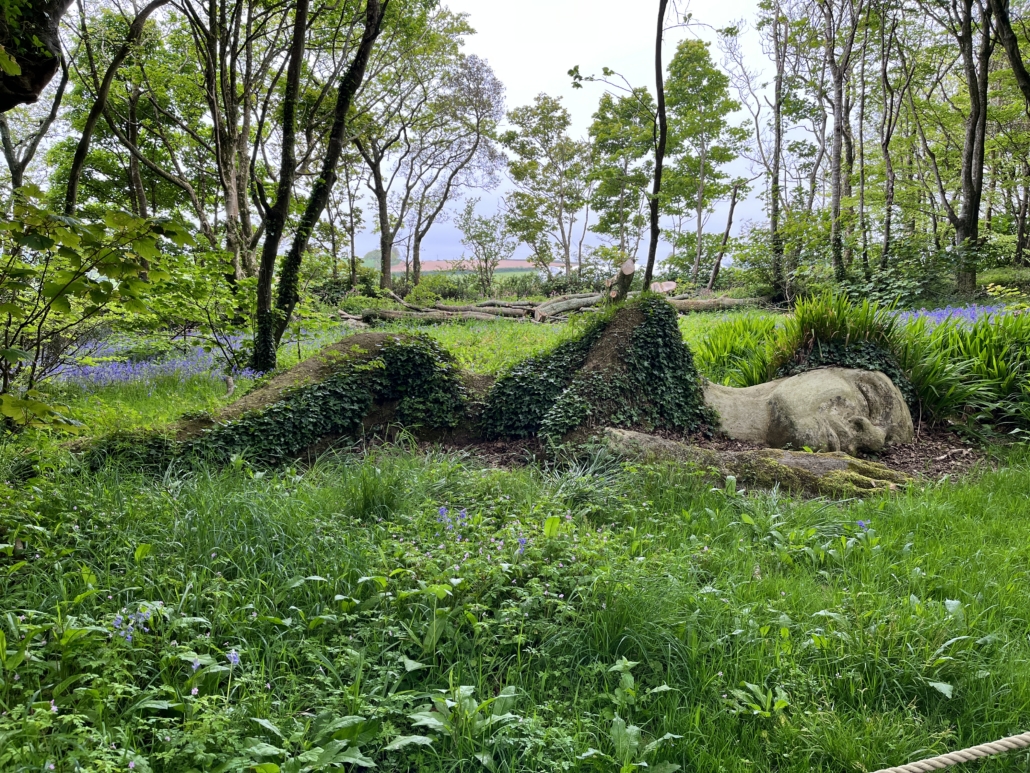
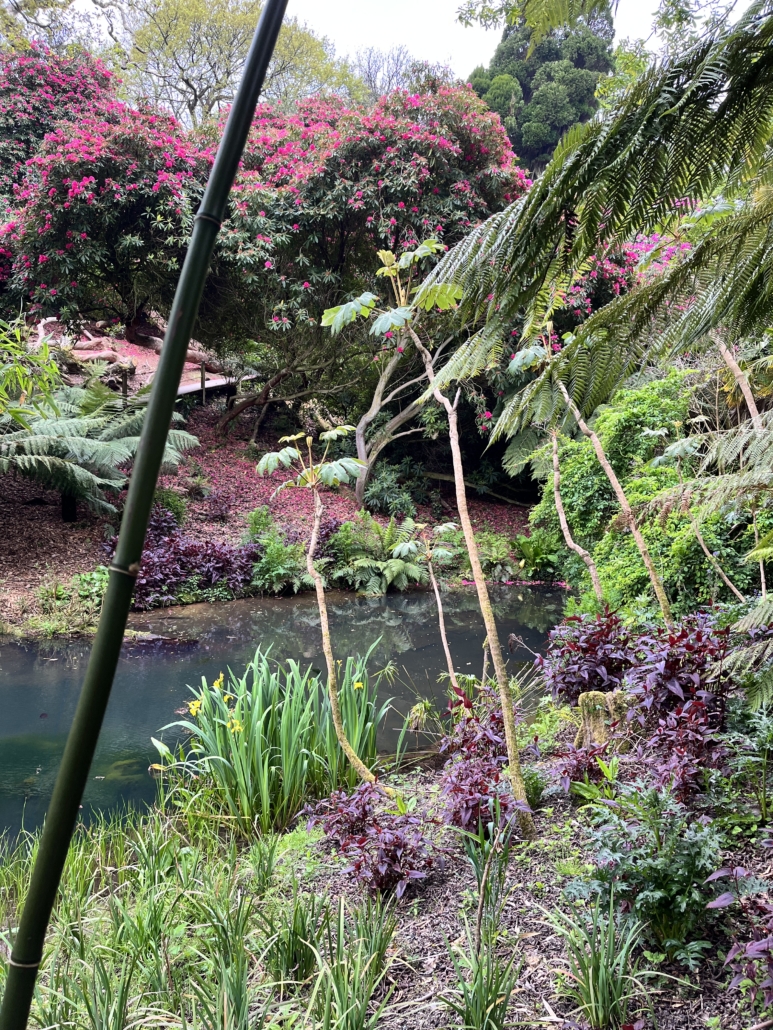
Along with the gardens, Heligan also is home to several heritage breed animals. In particular, they raise and care for the rare Devon & Cornwall Longwool (which are gorgeous sheep!) and also have Ryeland, Jacobs, and Kerry Hill.
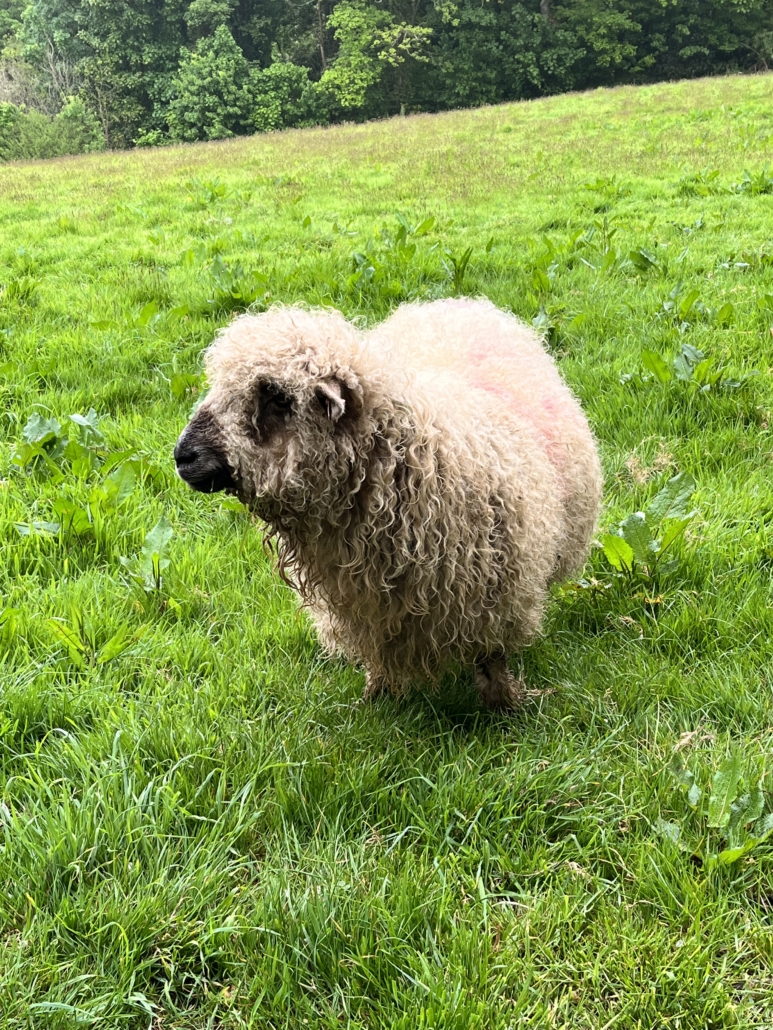
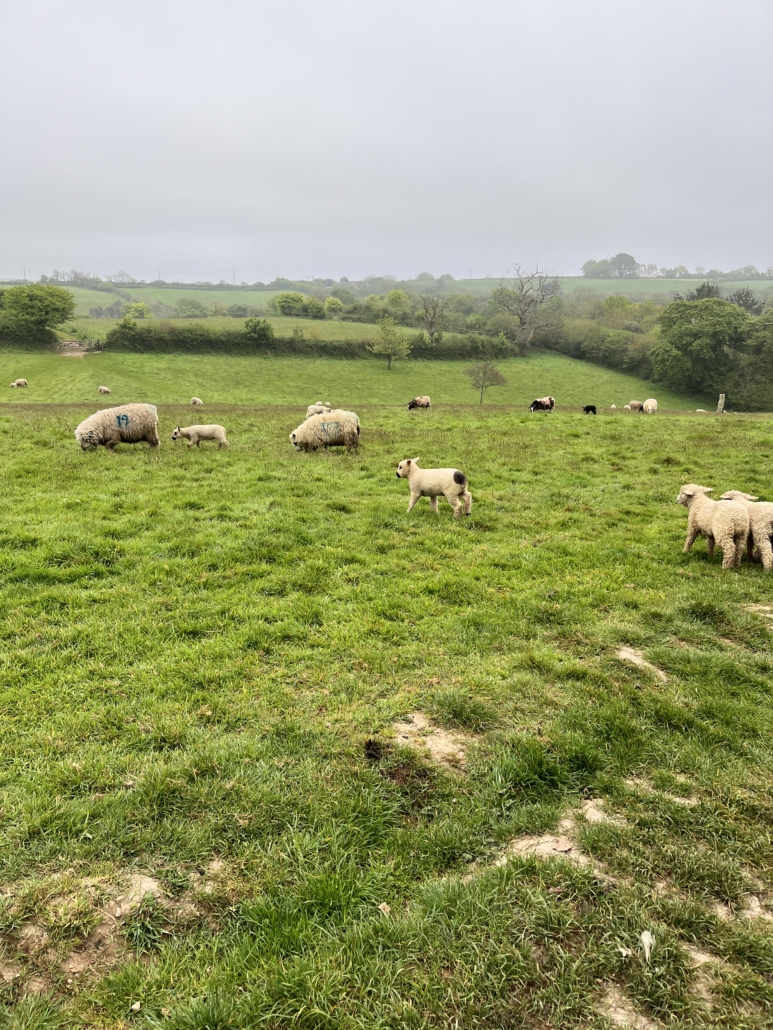
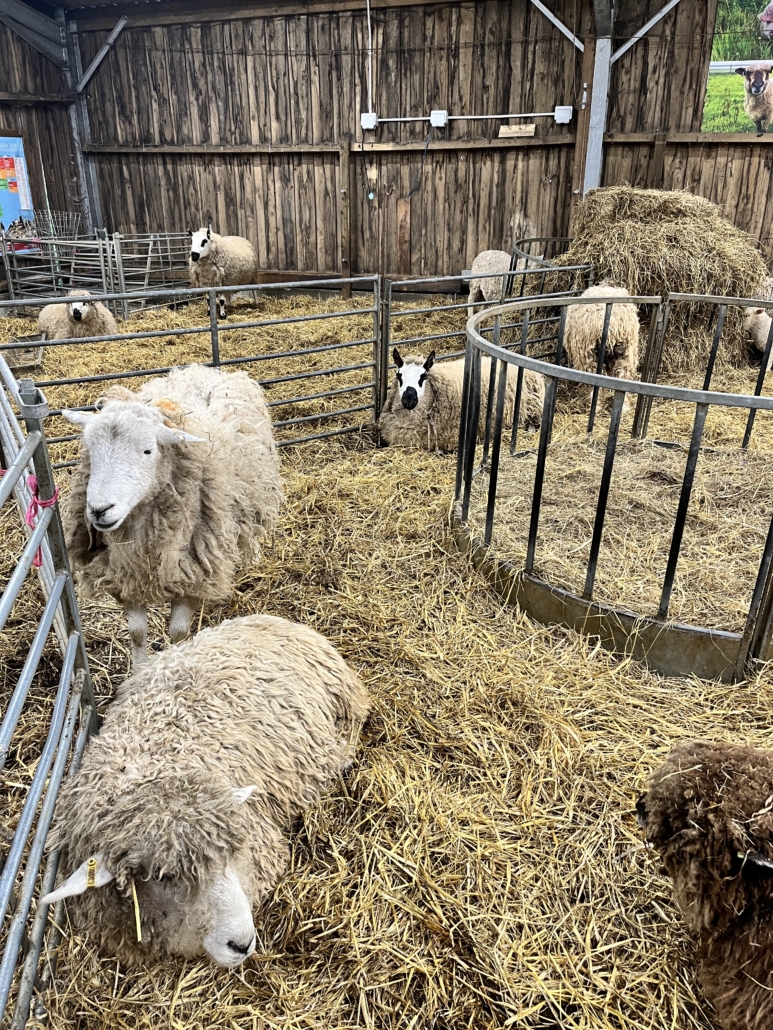
We were back to Bath for another day, making a quick stop in Glastonbury along with way. In Bath, we spent time relaxing and doing more sightseeing and shopping. I took to opportunity to visit the Jane Austen Center and even did a little dressing up! Also, if you’re even in Bath, make sure to have tea and a Sally Lunn bun (at Sally Lunn’s). Delicious!
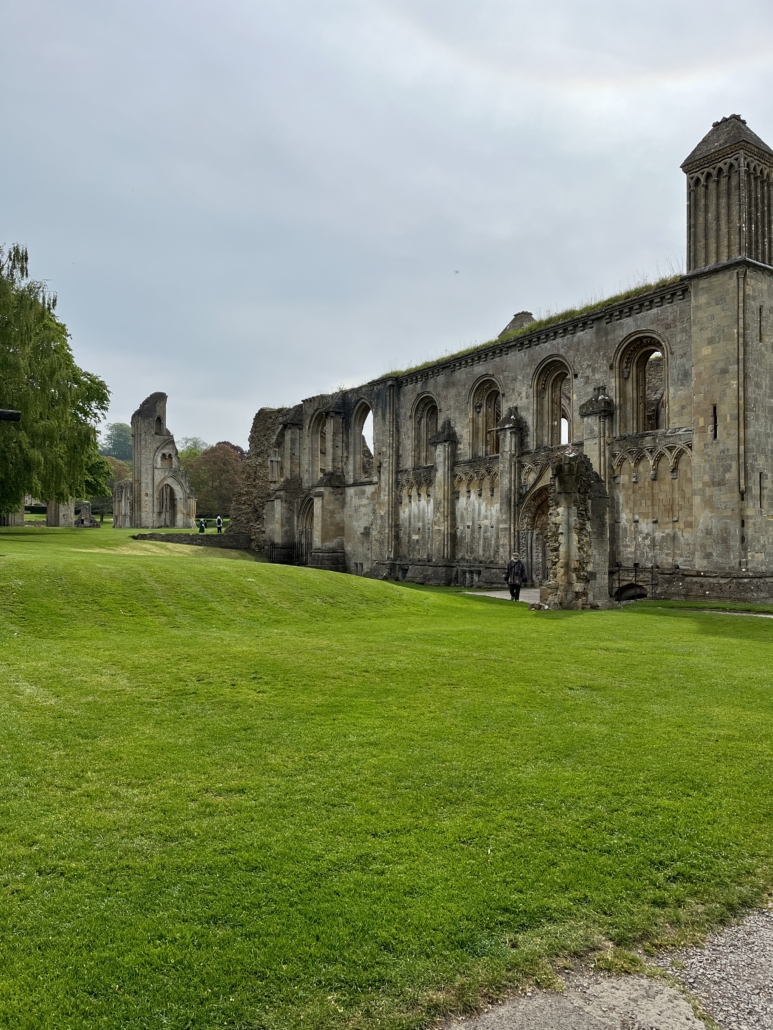
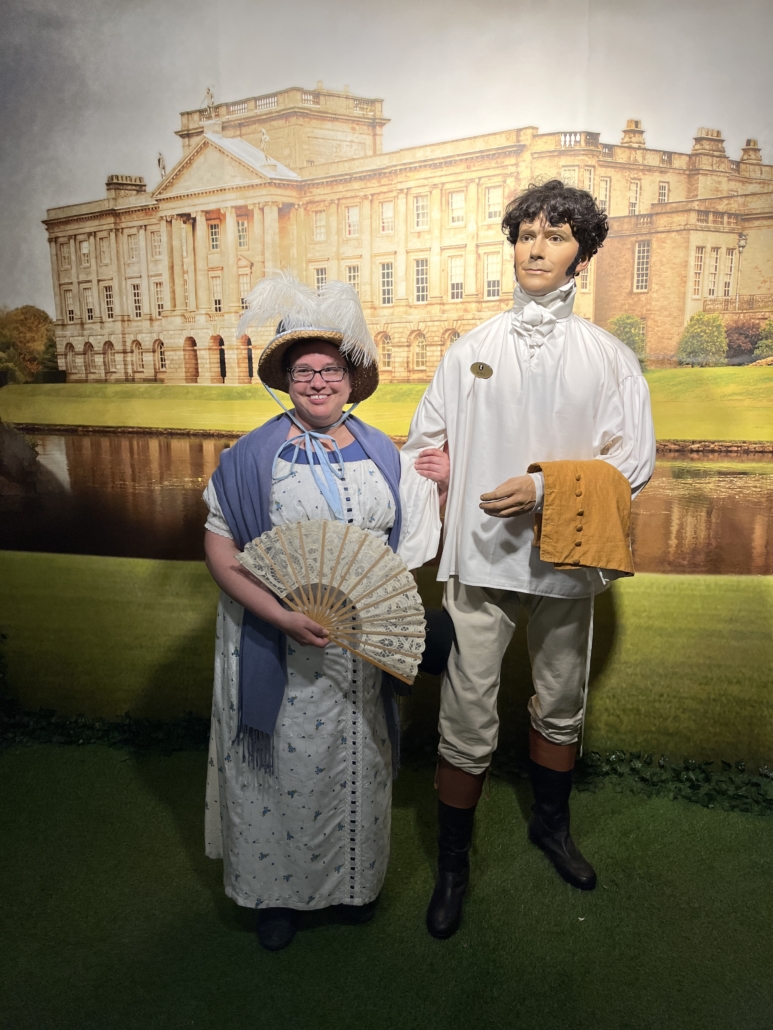
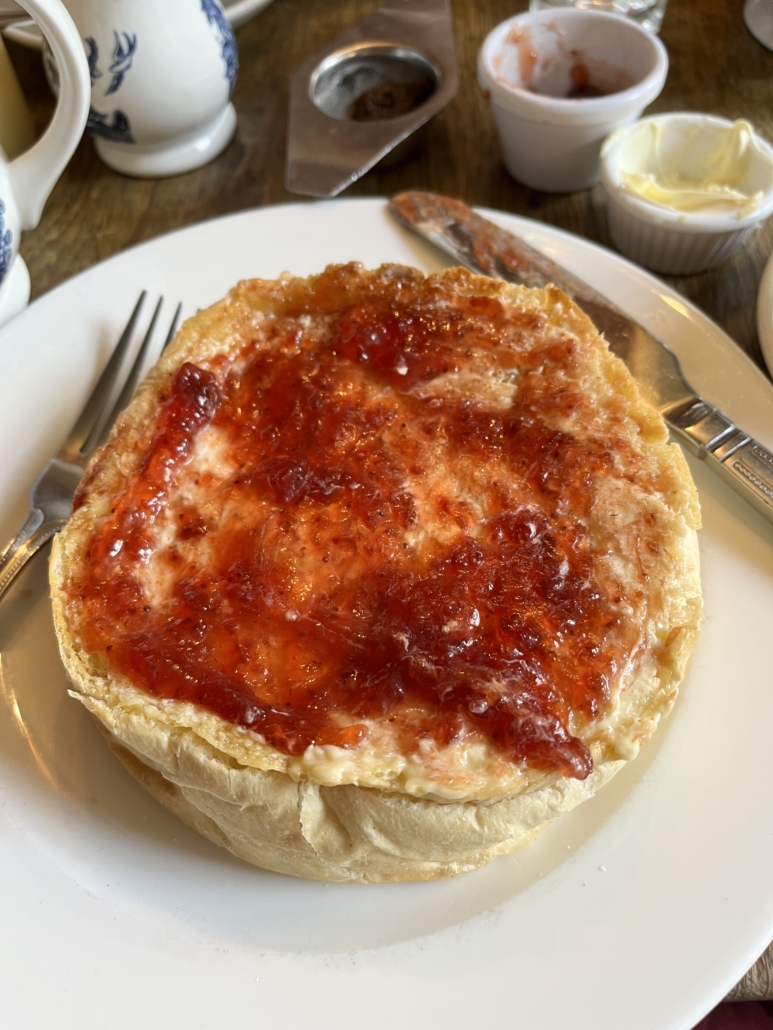
Our final three days were spent in the Cotswolds at Daylesford Organic Farm (which was an absolutely incredible place!). Along the way we went to Alderbrook Farm, where Grace showed us her Cotswold sheep as well as several fleeces (which one of our travelers decided to buy).
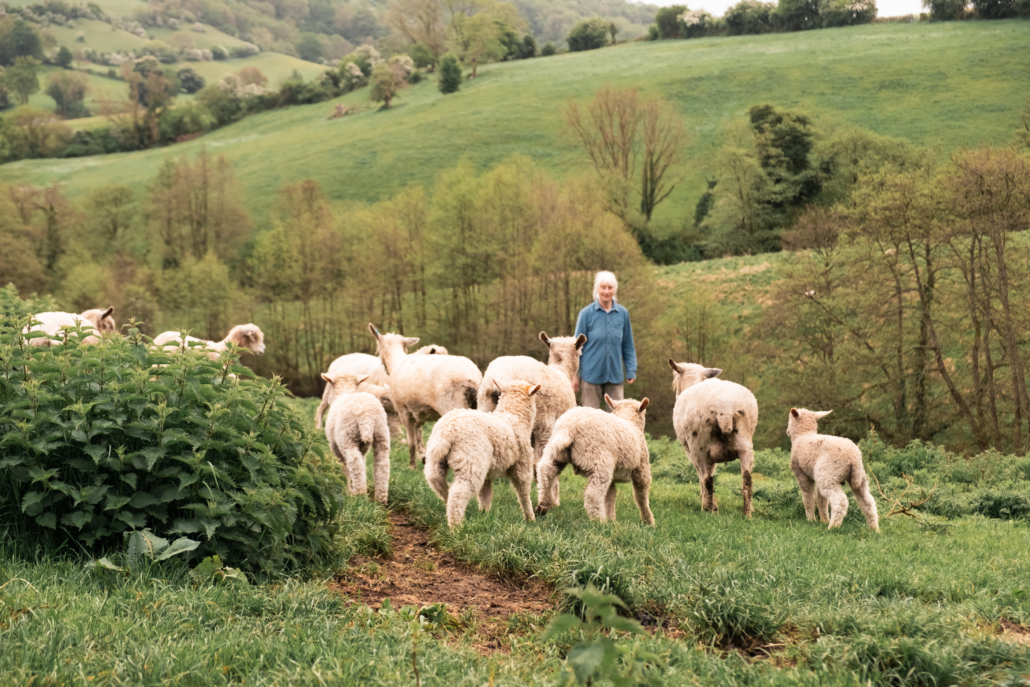
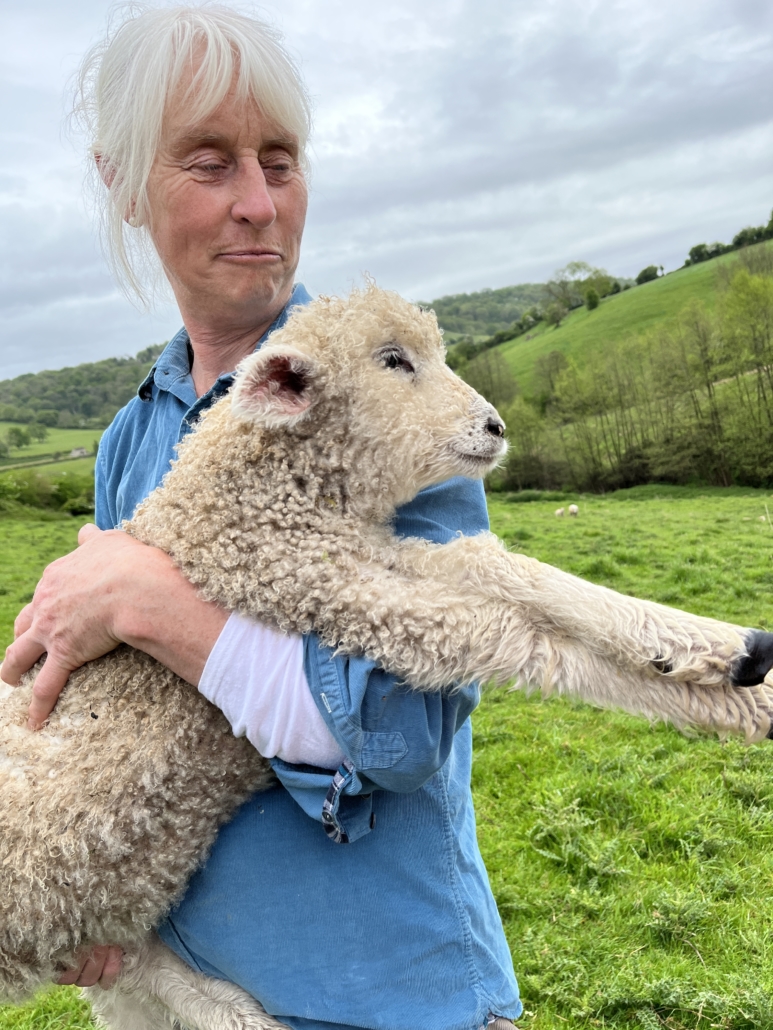
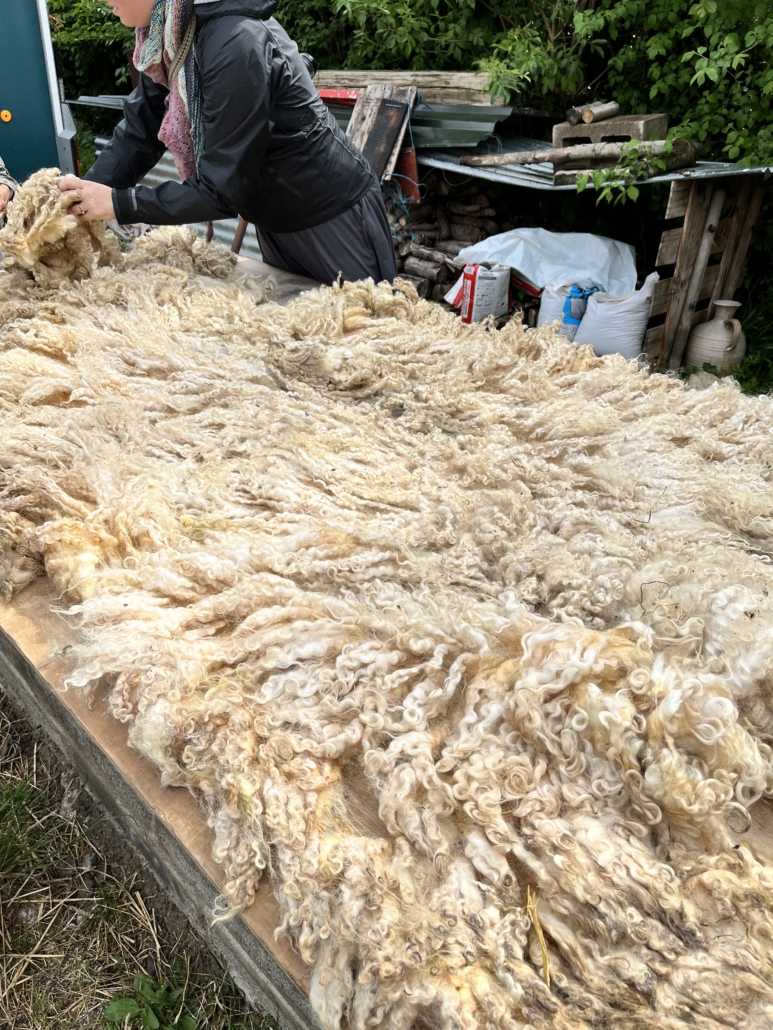
We also visited Sudeley Castle, where we were given a talk and tour by the castle’s textile conservator. The chapel at this castle is the resting place of Henry VIII’s final wife, Catherine Parr.
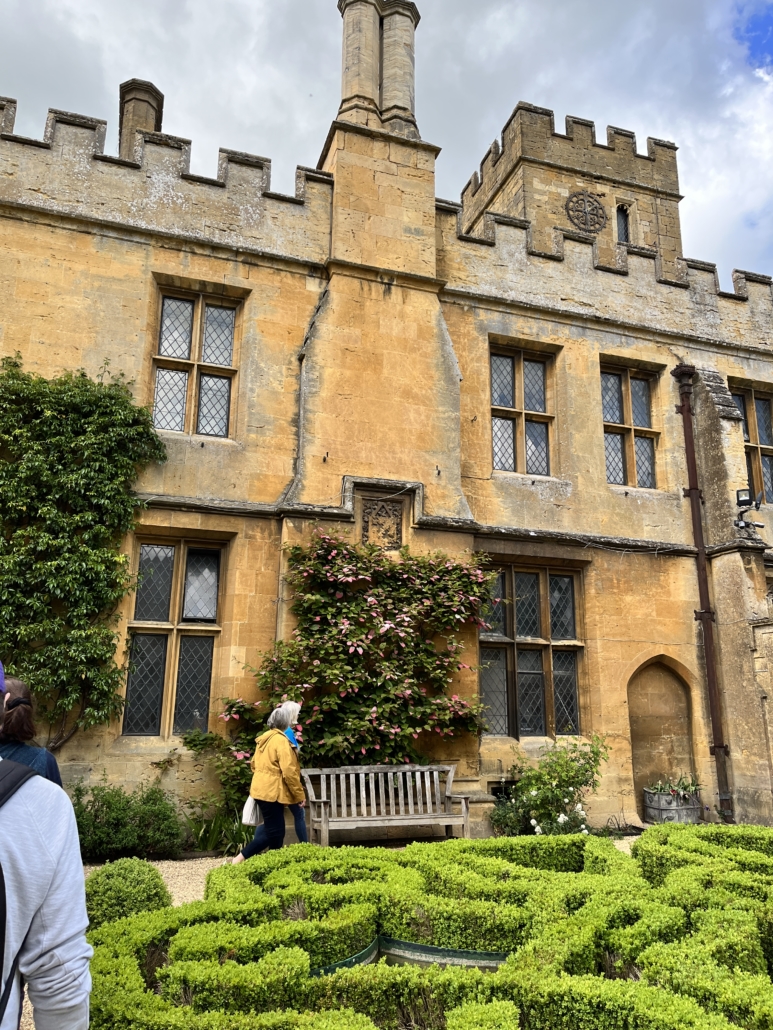
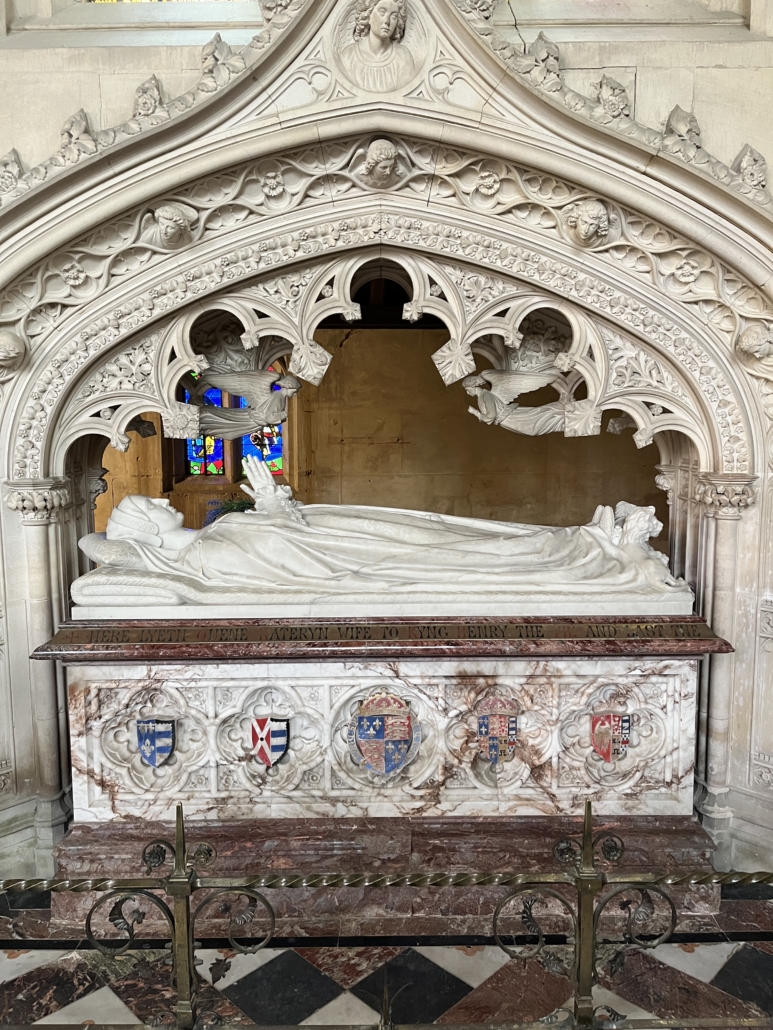
Our second-to-last full day was full of workshops for spinning and for cooking. Wendy McNamee brought fiber from various breeds along with a flock of Ashford wheels and we were able to spent several hours with her spinning those breeds (and learning to spin for those who didn’t yet know how). The cooking lesson was incredible—all ingredients came from right there at the farm and we made a tasty soup and a salmon dish.
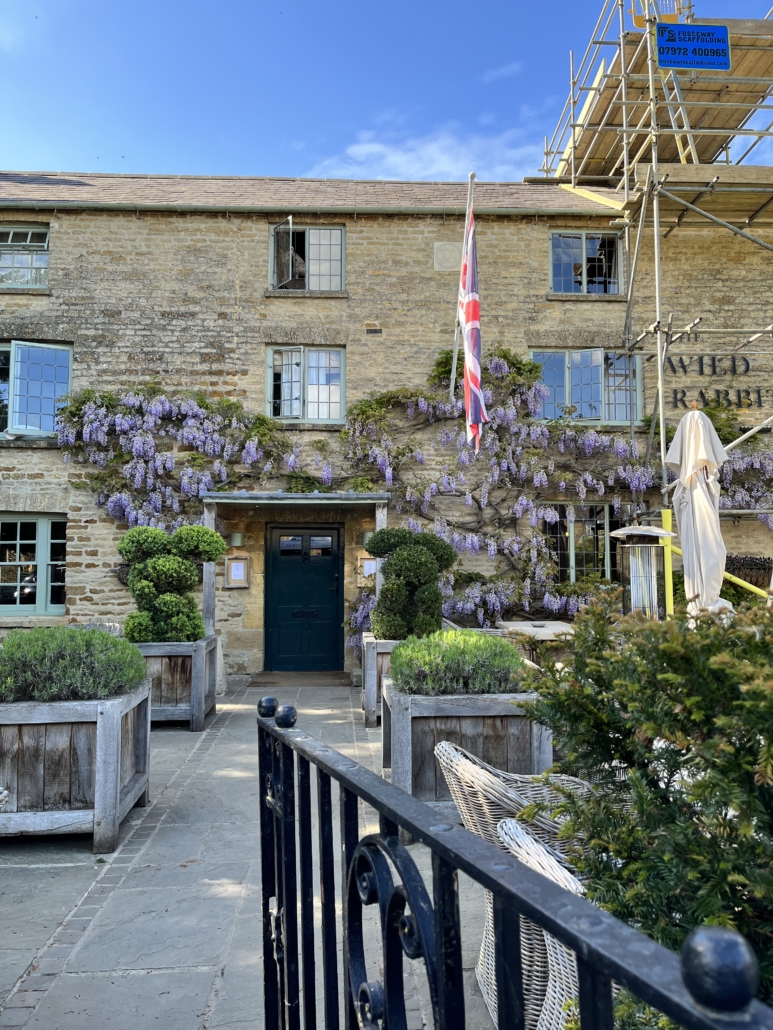
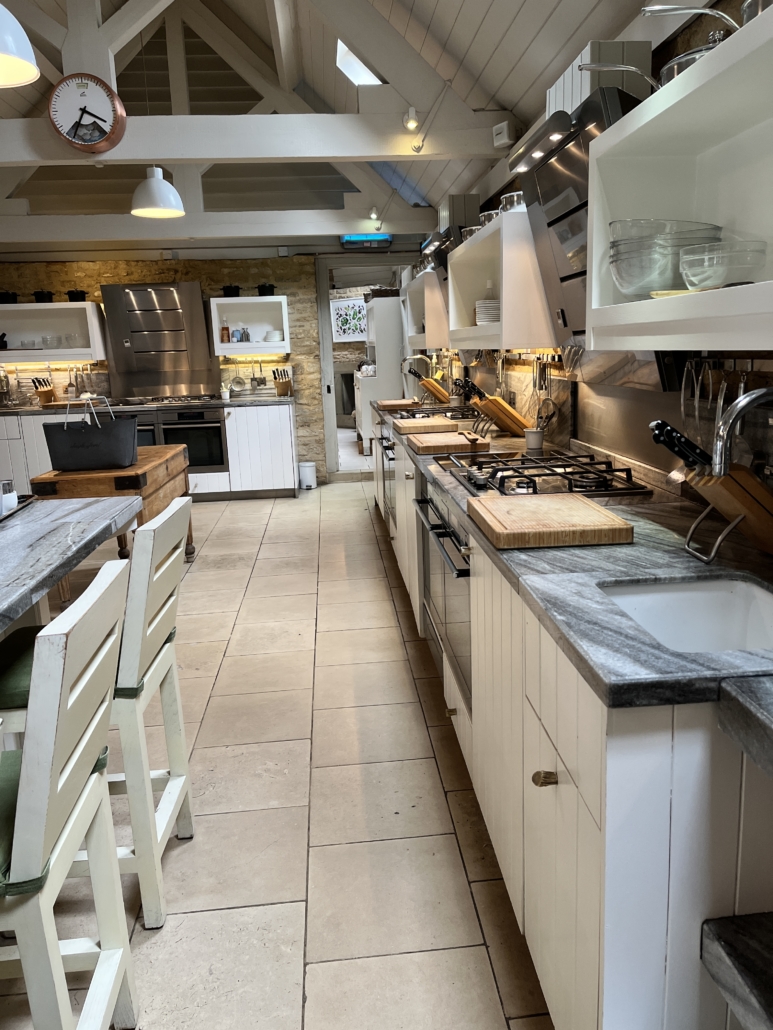
And our final day brought us to Armscote Manor, a private home with extensive grounds and sheep. We got a tour of the garden and got to meet the sheep, which included Portland and Black Welsh Mountain. After that, we visited Broadway Tower, with incredible views at the top.
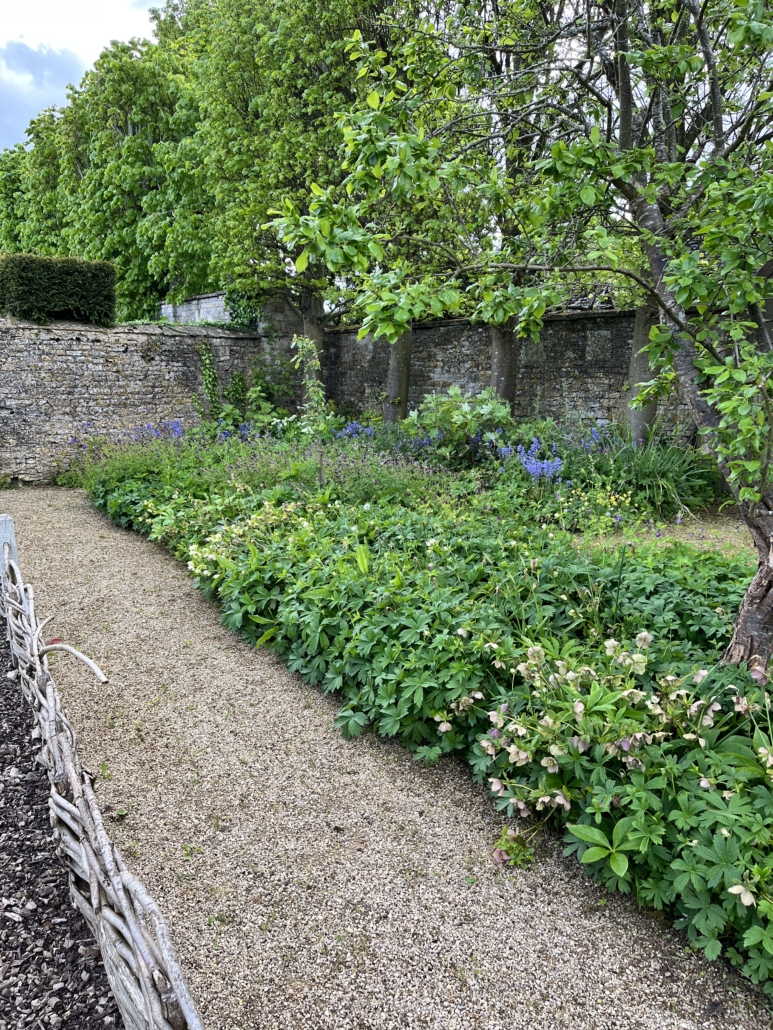
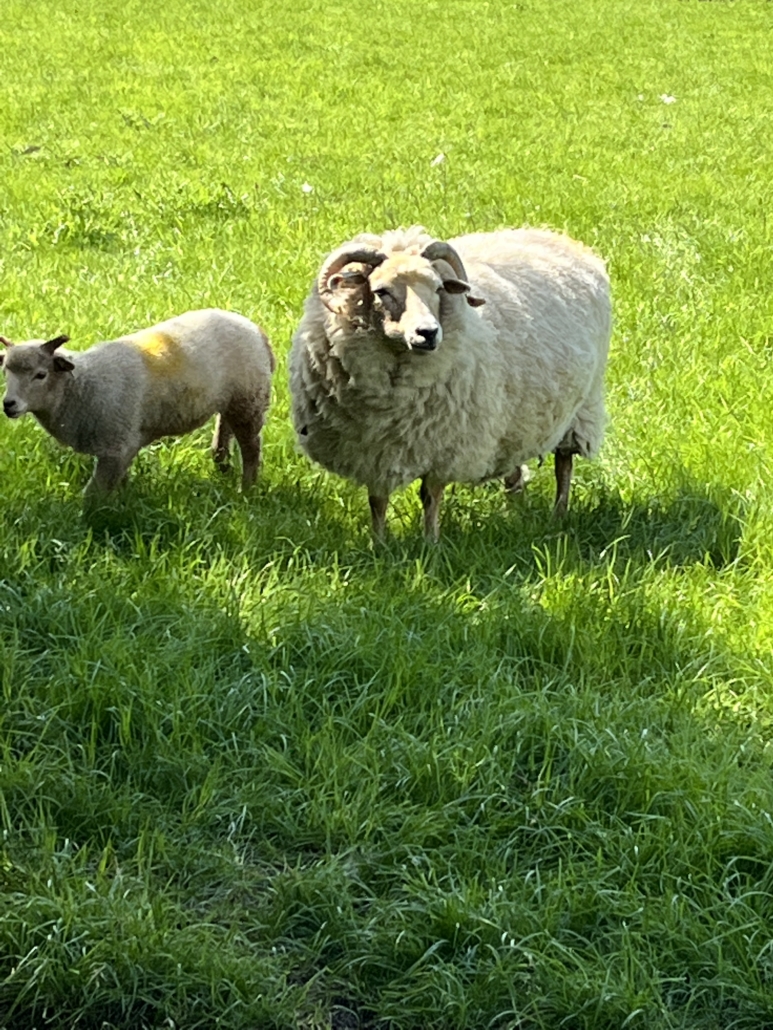
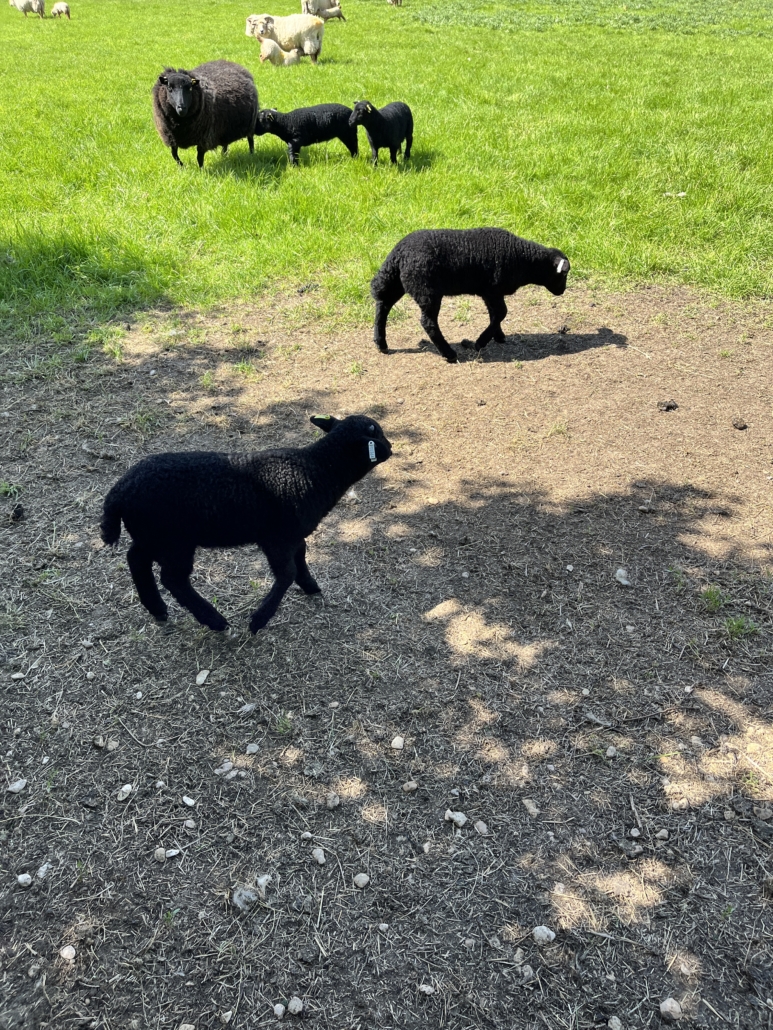

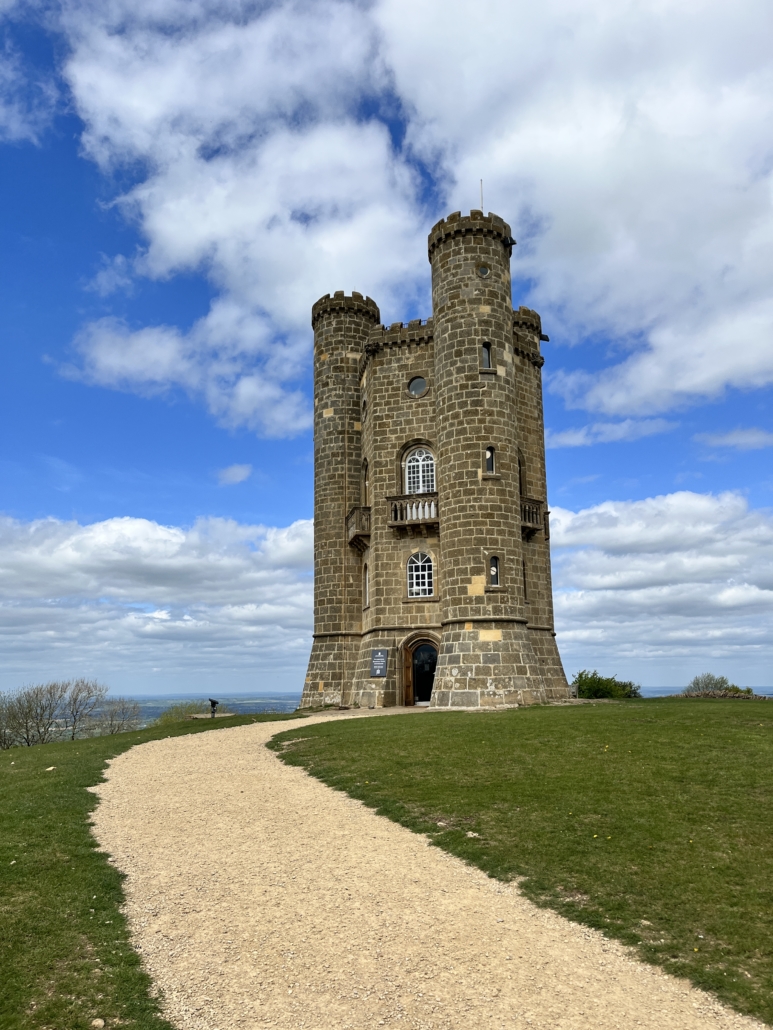
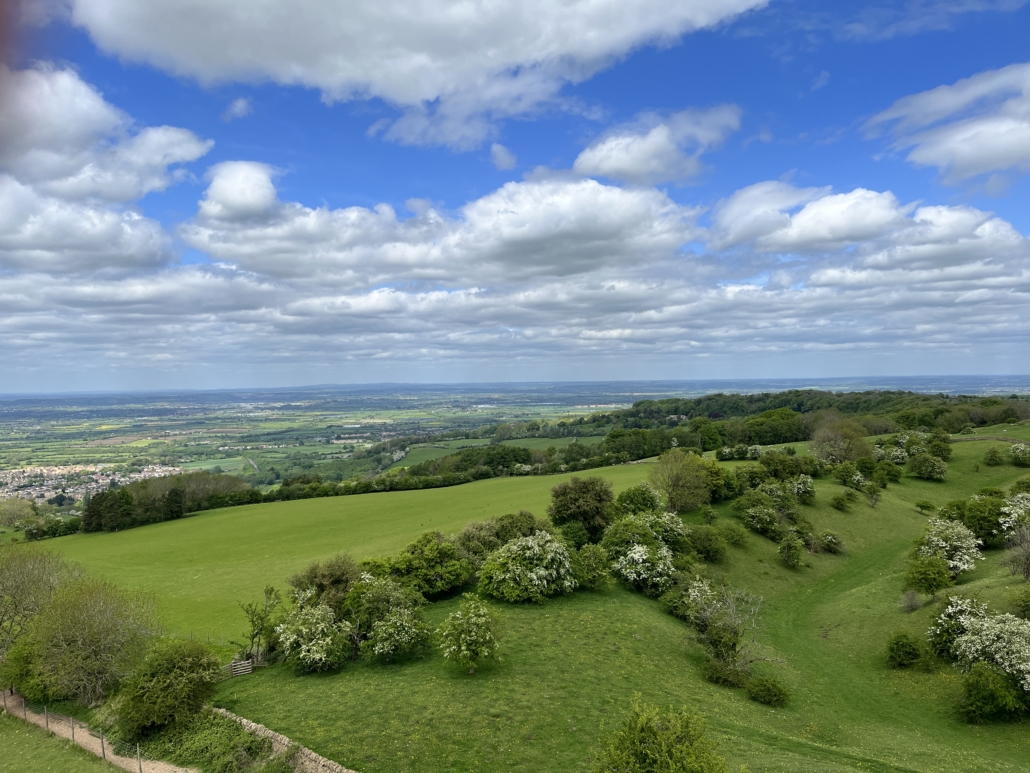
We capped off our final evening by a visit to the circus! Gifford’s Circus features performers both humorous and extremely talented (the two women who did acrobatics that involved hanging by their hair was both slightly terrifying and absolutely amazing). And we had dinner at Circus Sauce, a farm to table pop up that travels with the circus.
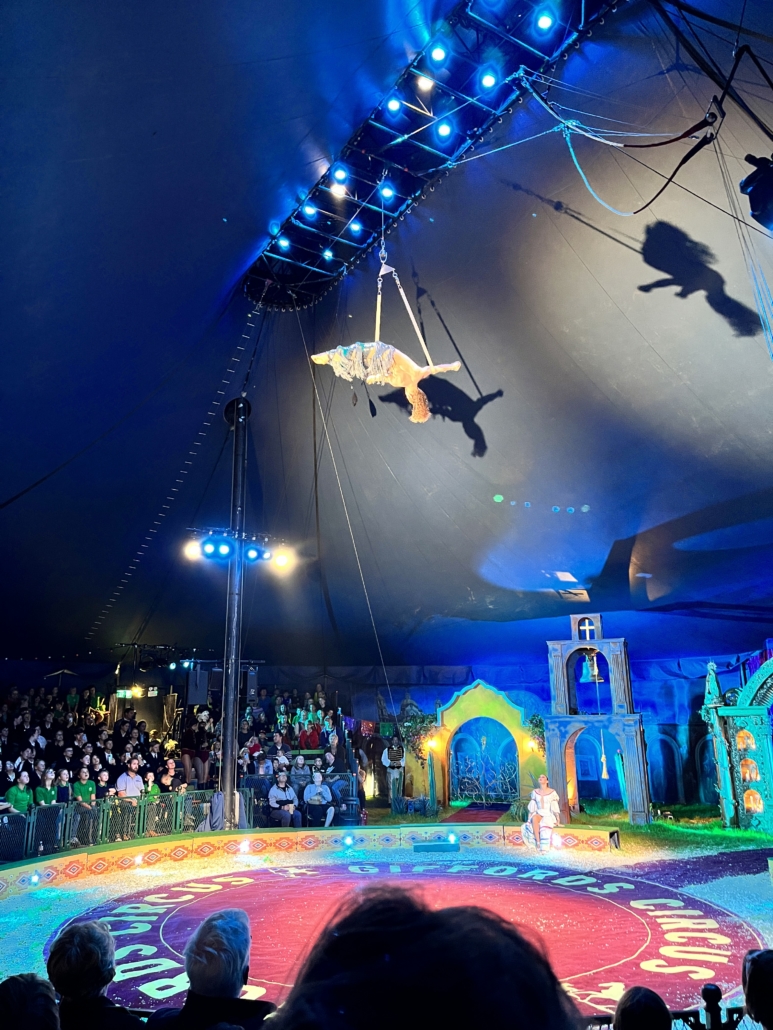
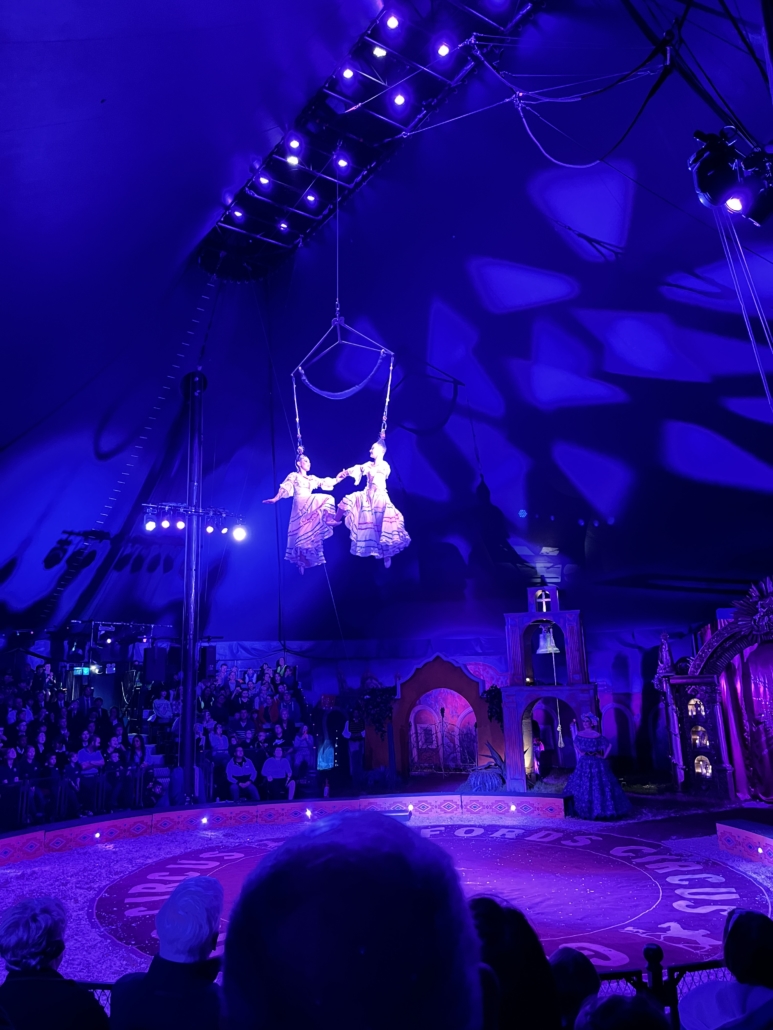
We got to do and see so many things on this trip, both sheep and fiber related as well as historical. But honestly, one of the best parts of the trip was getting to know the others on the tour, especially with our common interest in fiber arts. I was originally a little worried since I was going without knowing anyone else on the tour, but any fears were quickly put to rest with the warm and welcoming atmosphere of the group and of the trip leaders, Heather and Suzie. I can truly say that I made several new friends on this adventure of a lifetime.
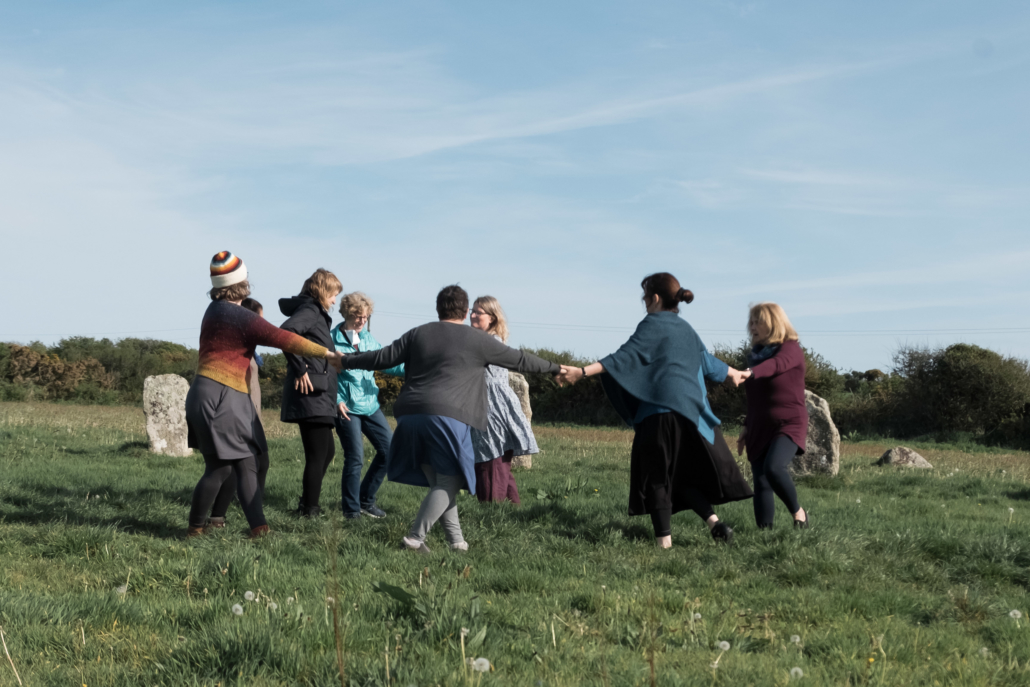
Rowan Tree Travel is a small tour company that offers tours specifically designed for the crafting community. In fact, there’s a “companion” tour to the one I went on coming up in the fall that covers northern England. That one is called A Wool Lover’s Visit to the North of England. Want to go? There are spots available. I’d love to see you there (that’s right, I’ve signed up for that one too!). Otherwise, there are/will be tours in other part of England, Wales, and Scotland, as well as Ireland, Iceland, Copenhagen and the Faroe Islands, Greece, and Canada.
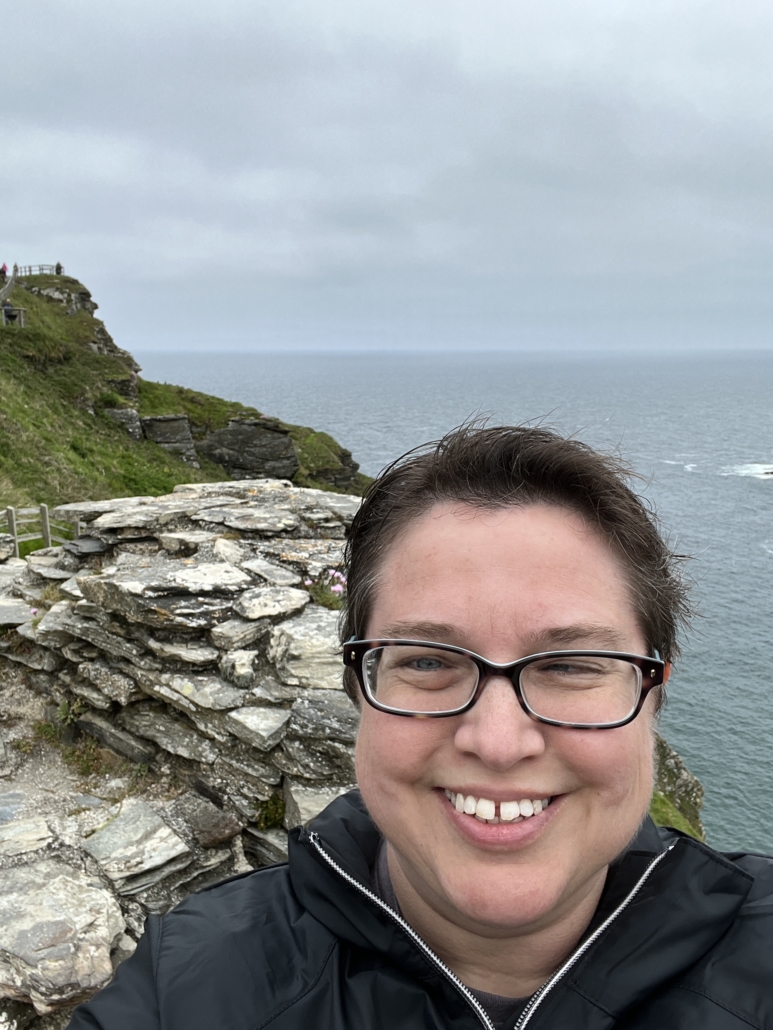
Karen Robinson has been knitting for almost twenty years and spinning for fifteen. She loves exploring the characteristics of various sheep breeds. She’s a voracious reader and has a full household with a husband, 10-year-old son, two Boston Terriers, and two cats. And she’s also the Managing Editor of PLY Magazine.
Let’s Talk About Sparkle Fluff
words by Jacqueline Harp | photos by Susan Schroeder
Have you ever heard of Sparkle Fluff? Oh, my! Envision a handful of fiber goodness that features a colorful mixture of mohair locks and glitz, and it is known to make handspinners smile when they get their hands on it. Sparkle Fluff is a fiber preparation composed of a color-coordinated mix of mohair locks, sheep wool locks, and loose Angelina fibers. It is ready-to-spin and full of texture and sparkle. You can spin it into a wide variety of chunky, fantastical art yarns or sprinkle it into carded preparations to add some extra pizzazz.
Let’s meet the innovative mind behind Sparkle Fluff, Susan Schroeder of Rusty Spur Ranch and Creations, located in Rathdrum, Idaho. Be prepared to be inspired to use mohair in ways that bring the most joy to your spin projects.
Meet the fiber creative
I came across Susan a few years ago, at a fiber arts festival in the Pacific Northwest, and was impressed with her creativity, hard work, and effervescent personality. Susan is an expert indie dyer, fiber artist, and Angora goat shepherdess to a well-cared for flock that provides high quality mohair for her fiber projects.
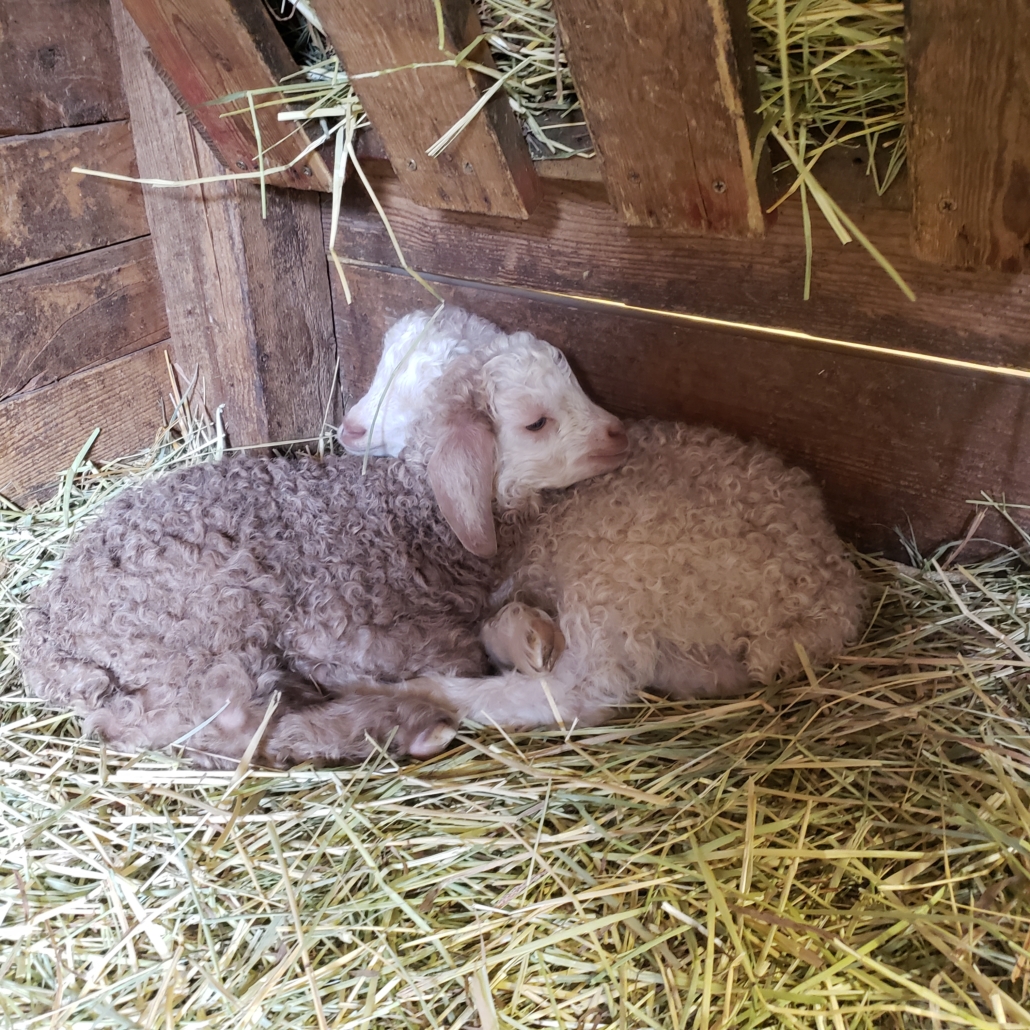
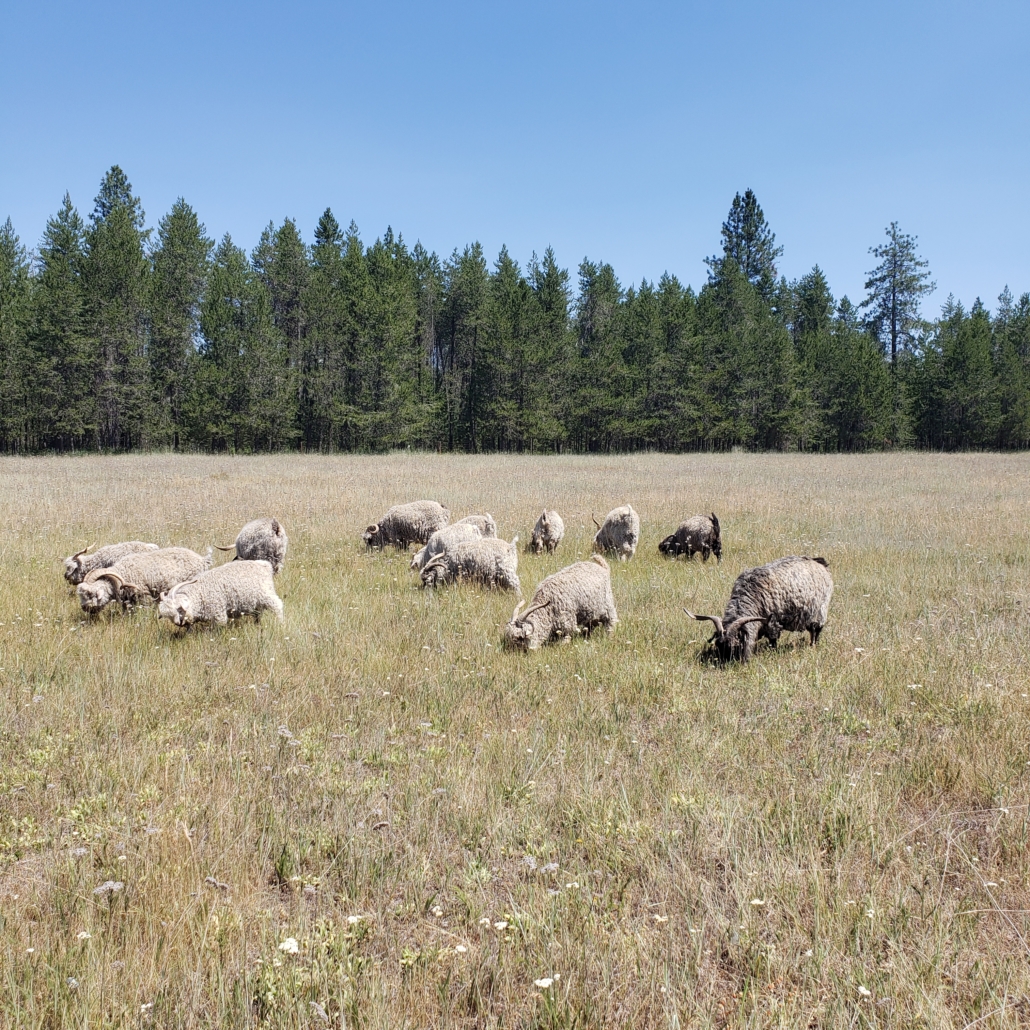
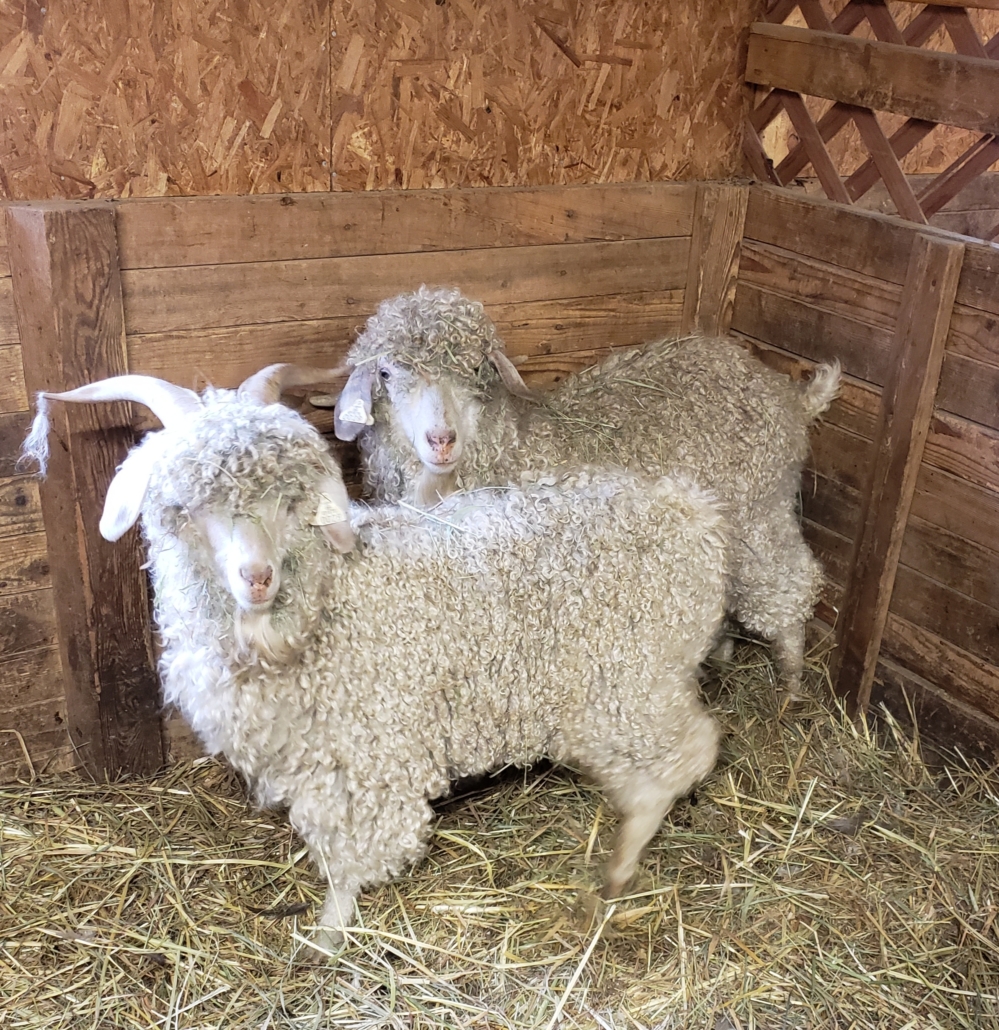
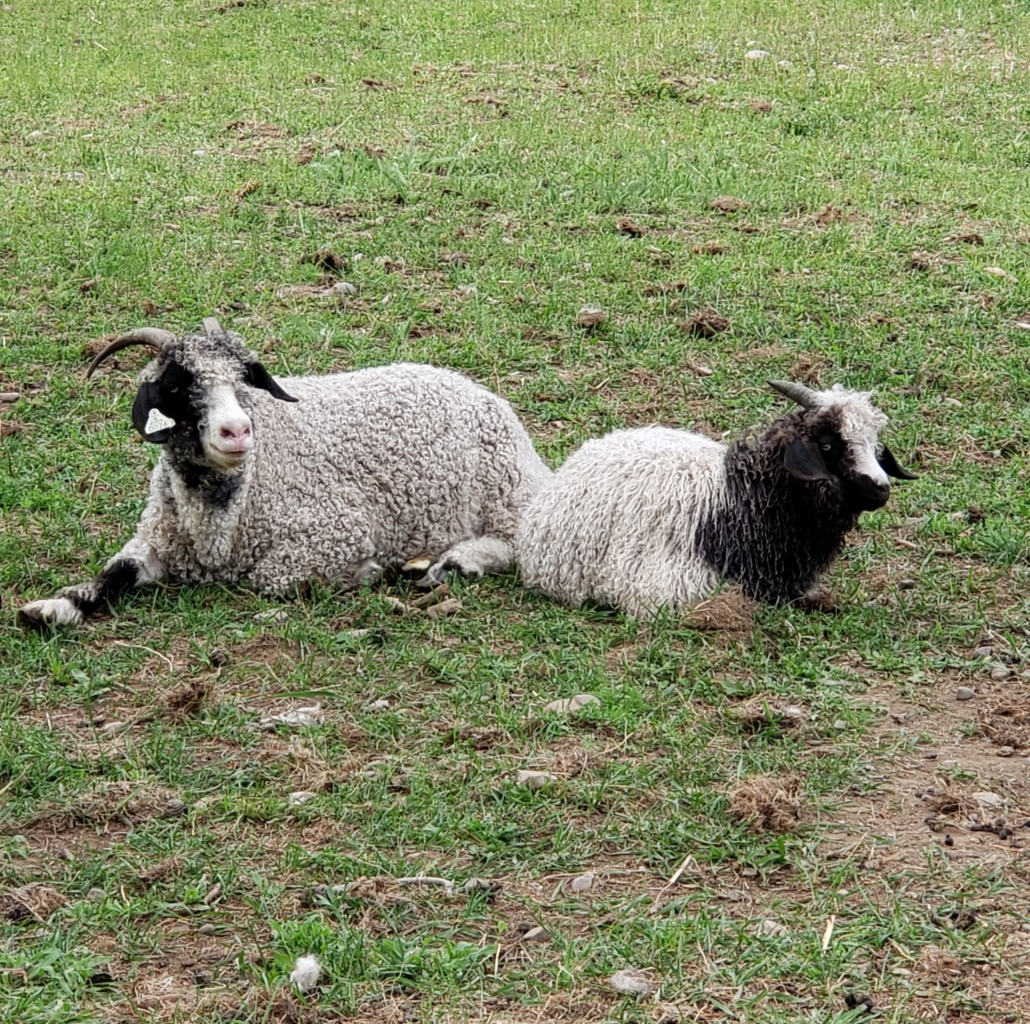
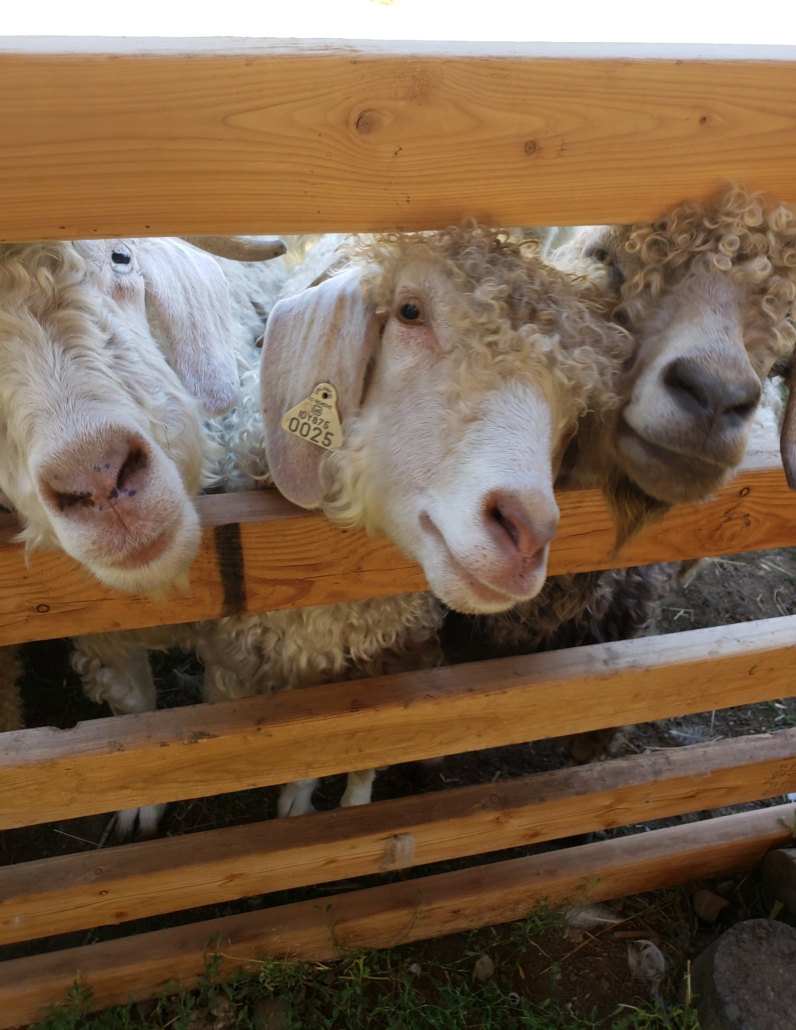
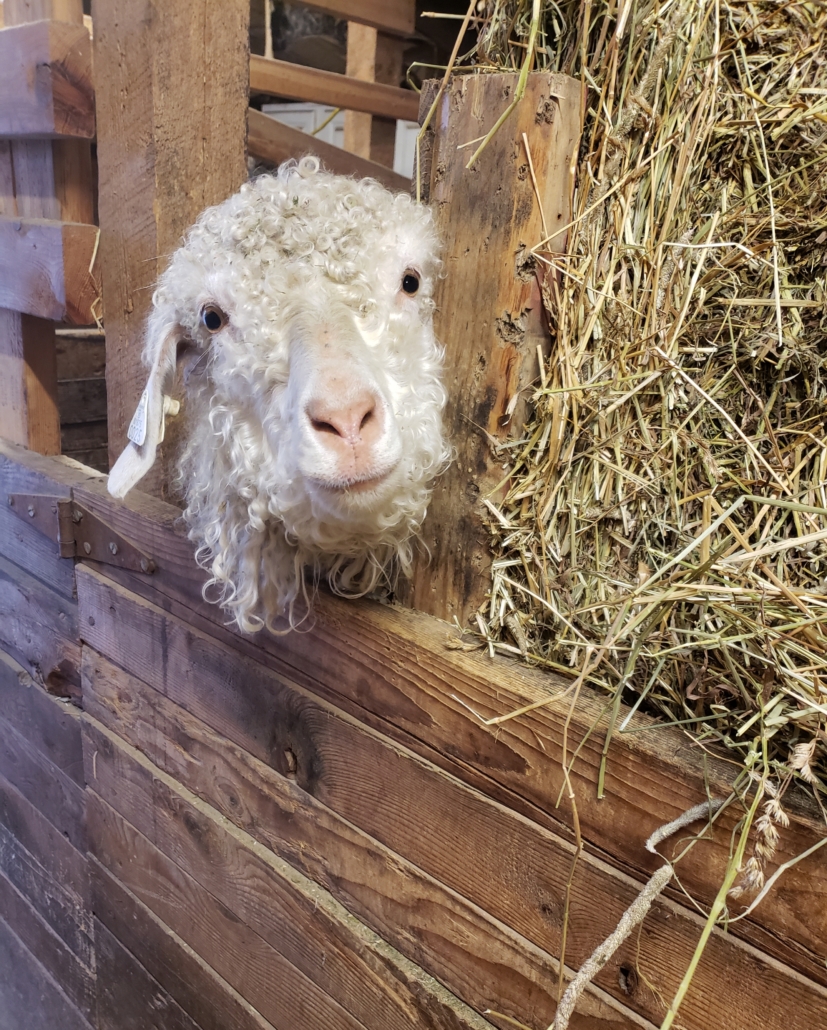
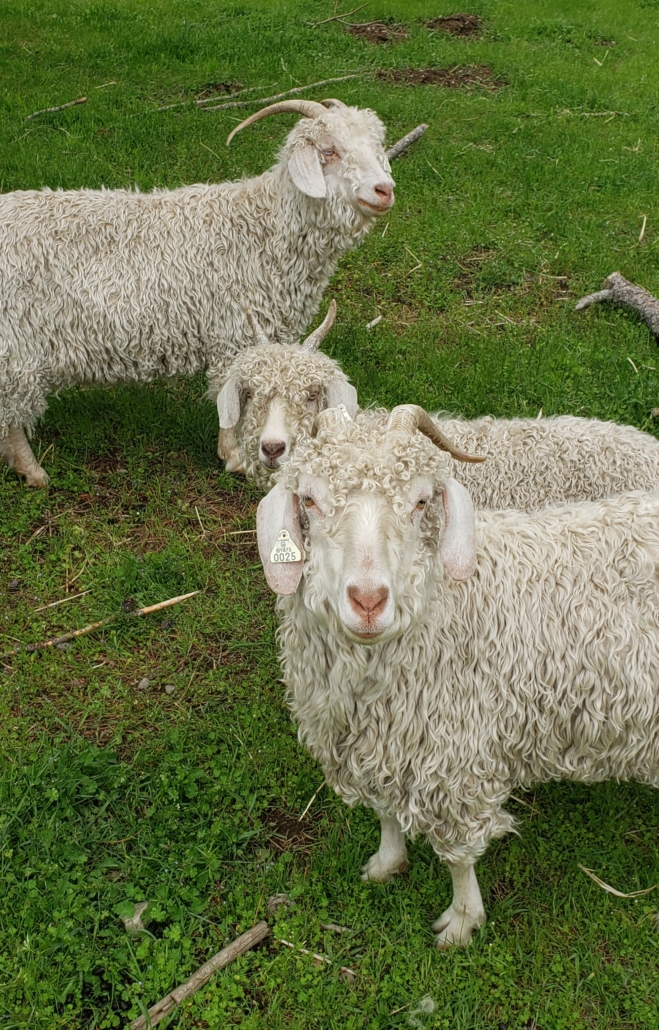
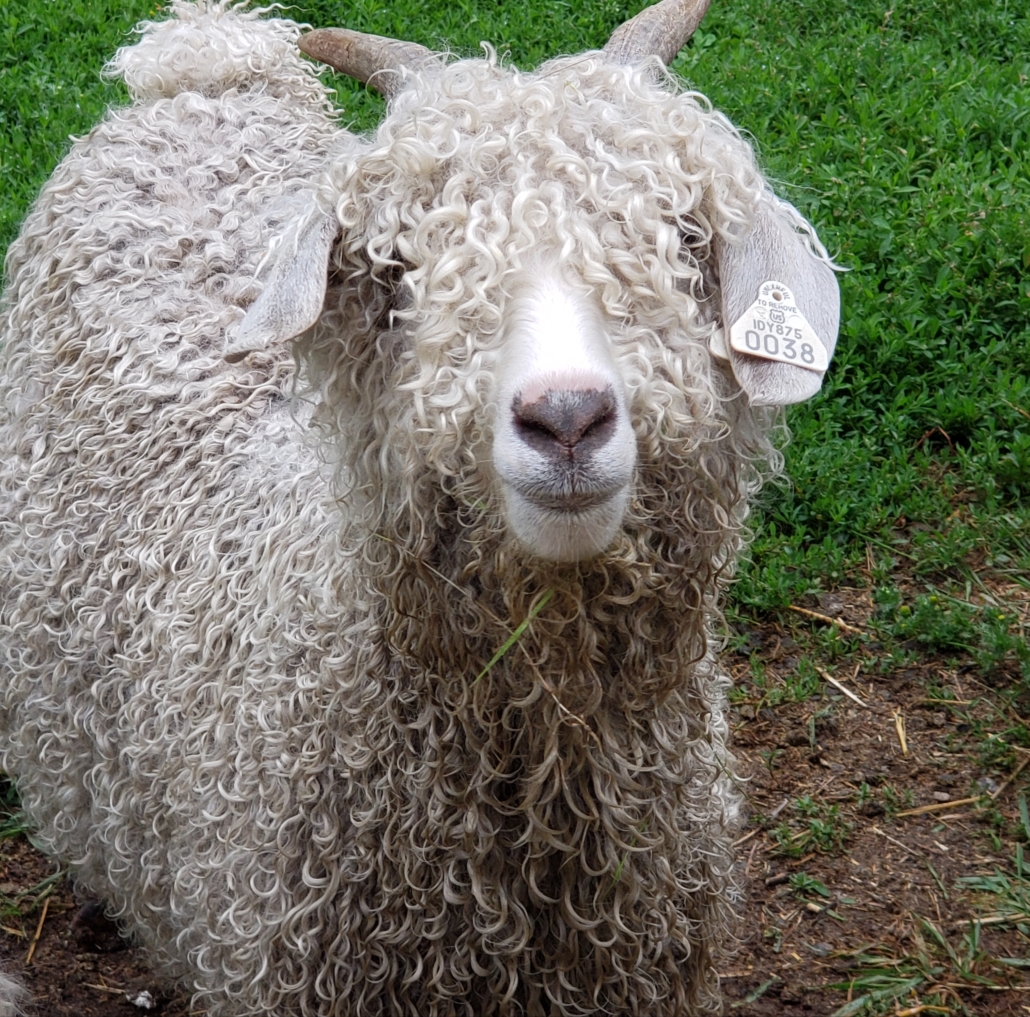
Susan’s fiber arts journey started with knitting as a way to pass the time during family road trips. She bought a handspun skein from Symeon North, author of the book, Get Spun (2010), and this beautiful yarn inspired Susan to learn handspinning. She started with a drop spindle and eventually learned to use a wheel. She then taught herself the art of dyeing fiber to bring unique colors to her own spinning fibers. A few years later, four Angora goats made their way into Susan’s life to provide mohair fleeces and natural weed control for her farm. Inspired by the growing flock of Angora goats on her farm, she started a fiber arts studio and named it the Rusty Spur Ranch and Creations.
Susan strives to use the whole mohair fleece in a productive manner. The prime locks are used for Sparkle Fluff, while clean belly fleece goes into cat toys. Remaining parts of the fleece go into the garden as mulch or into the bottom of plant pots to improve water retention.
Gathering the elements
Raw fleece selection is step one. Within a batch of Sparkle Fluff, there may be two or three different textures of mohair depending on what Susan has available. She knows the fleece of each goat in her flock, as it varies from goat to goat. Some fleeces are Navajo-style, with long, straight locks, while others have tiny curls.
Along with the mohair locks, each batch of Sparkle Fluff may have wool locks from up to five different breeds of sheep. While the mohair comes from her own flock, the sheep wool is sourced from different farms. For both fiber types, Susan looks for well-separated, open locks that are not felted and that contain the least amount of hay.
Secondly, she uses gentle washing methods so the locks don’t stick together. Once the locks from all fleeces are clean, she will dye bulk batches of locks in different colors.
Susan: I don’t have a Sparkle Fluff color idea in mind when I start dyeing fleeces. I will dye up to five fleeces at once. Each fleece is dyed a different color. After the fleeces are dyed, I start playing with the colors I created. The key is to take a few handfuls of various proportions and start mixing them together. If I like what I have, I will pull large amounts of dyed fleece and weigh it into about 10 ounce batches before I start mixing.
Mixing it up!
Once she has selected the color and fiber mix, she makes a pile and starts handpicking the locks and placing them into a large bin. She uses her hands to carefully pick and separate the locks because a fiber picker would rip the locks apart. After filling the bin, she gently tosses the fibers like a salad to ensure the Angelina is well distributed and the locks are evenly mixed to her satisfaction. She wants the locks and Angelina mix to be loose and flowing, not clumpy.
When mohair is mixed with wool and Angelina, the mohair pops! All fibers in Sparkle Fluff support the pop and shine of mohair.
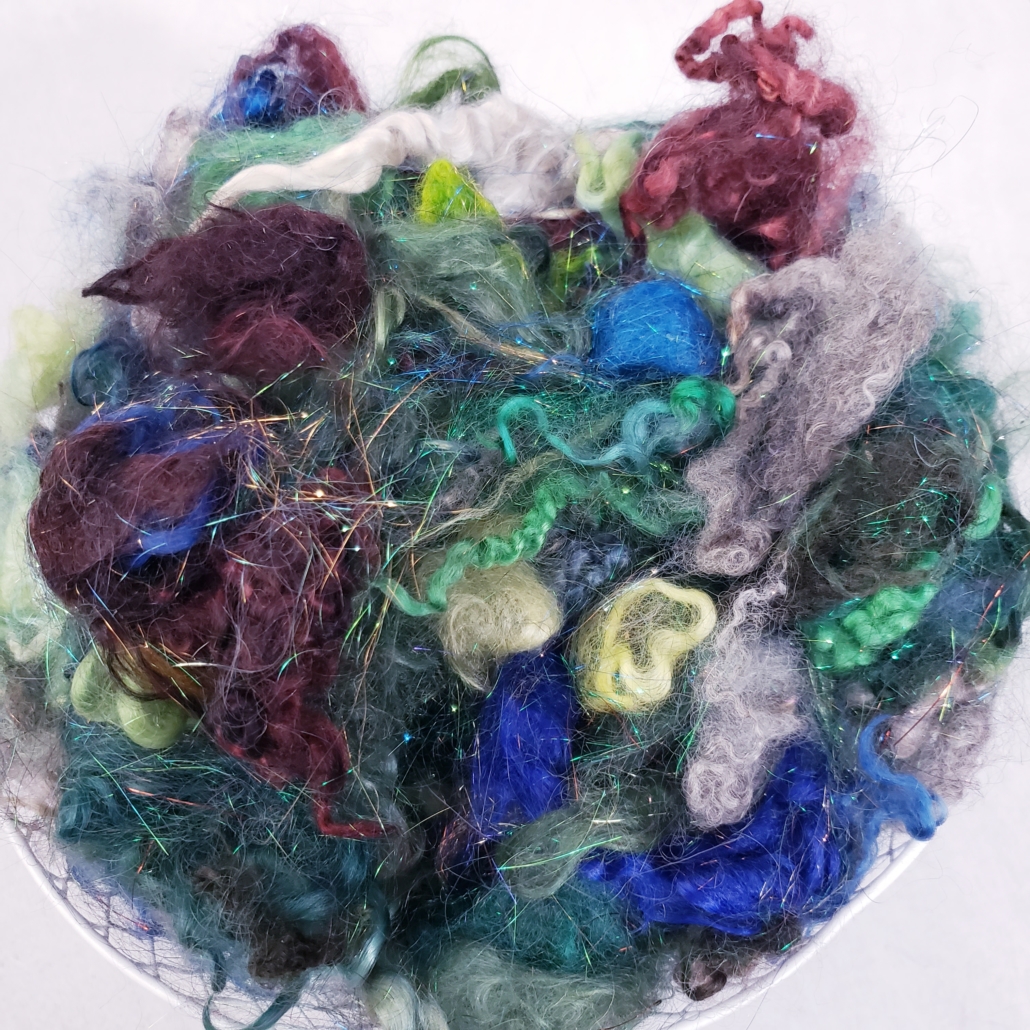
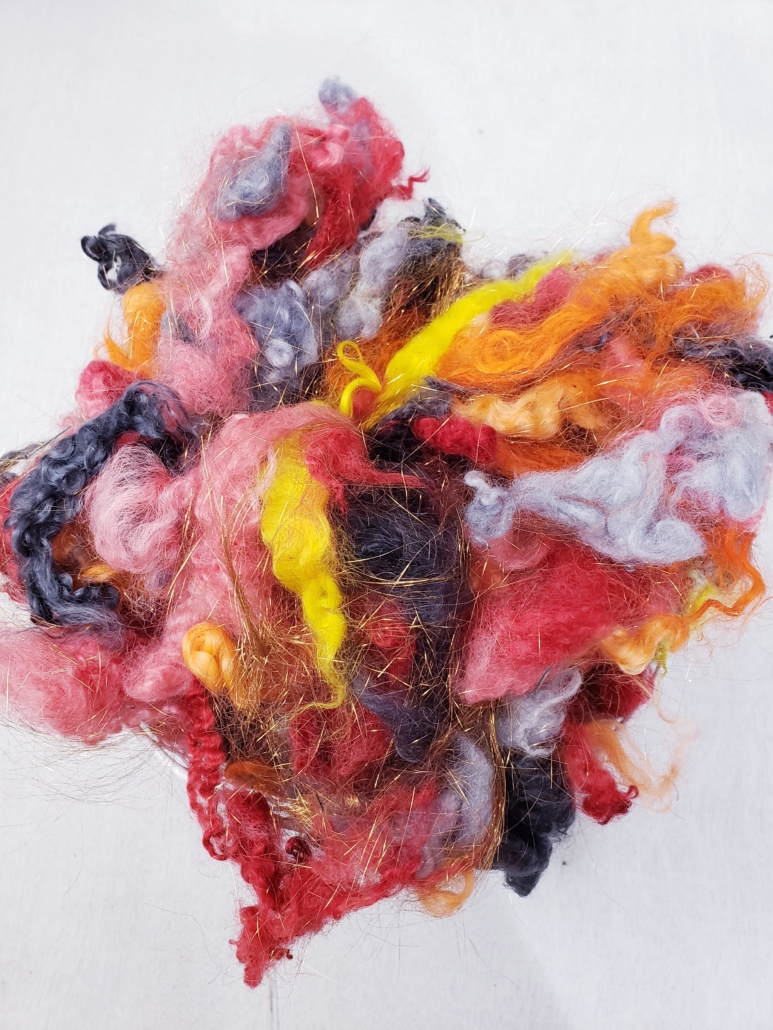
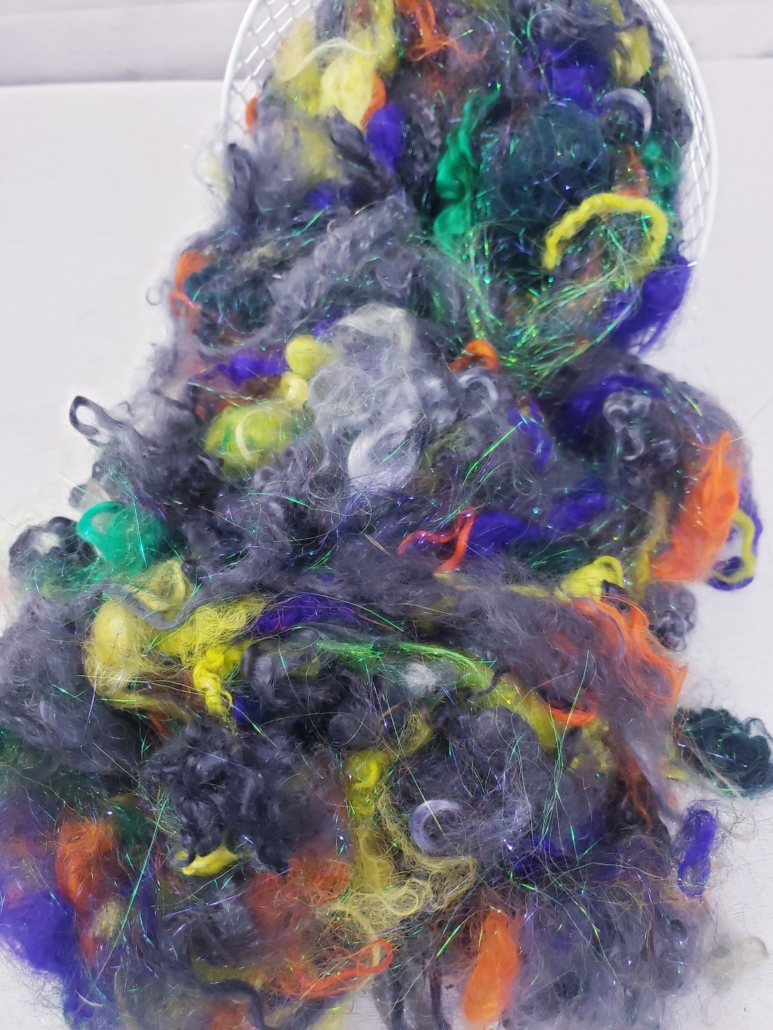
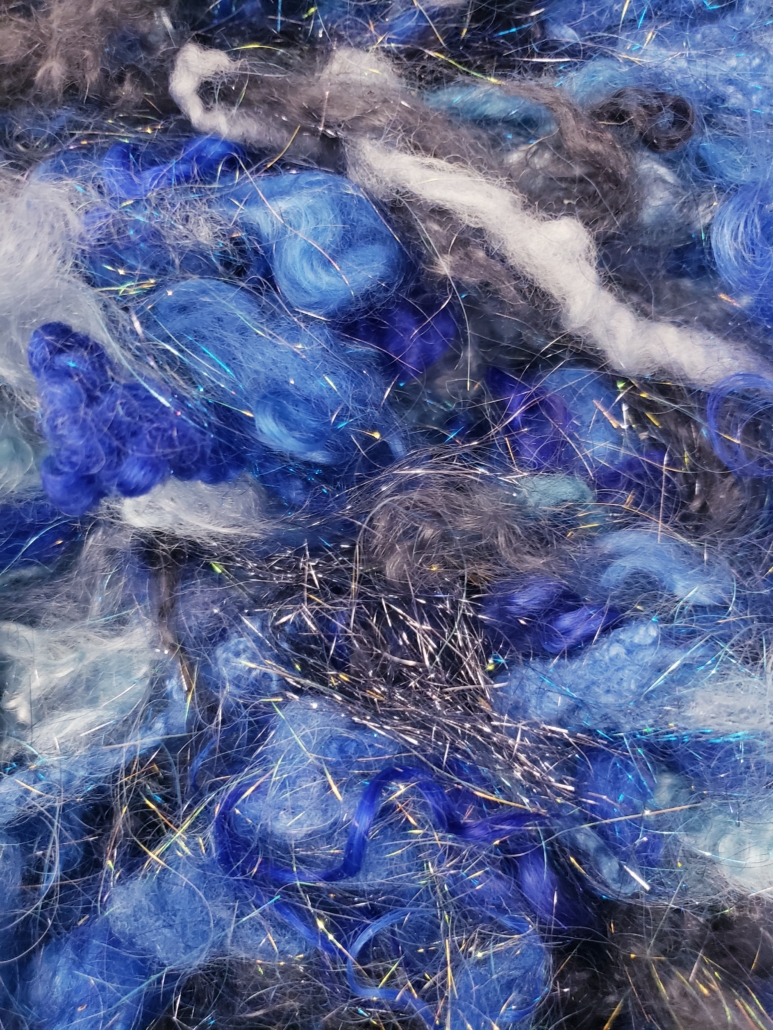
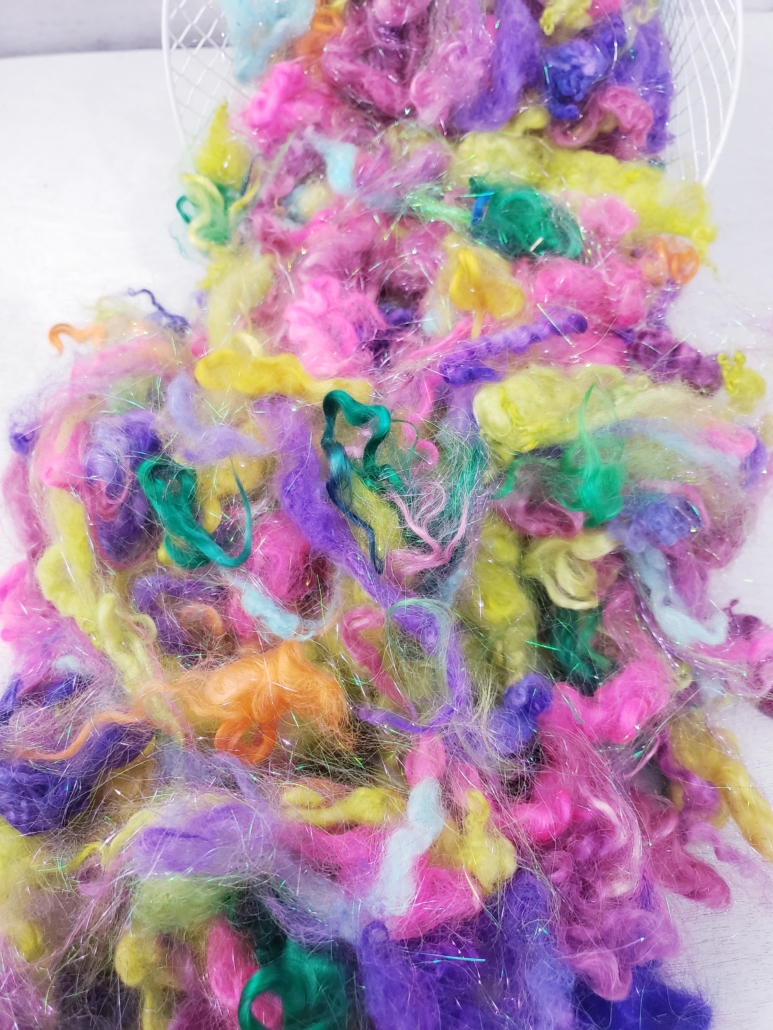
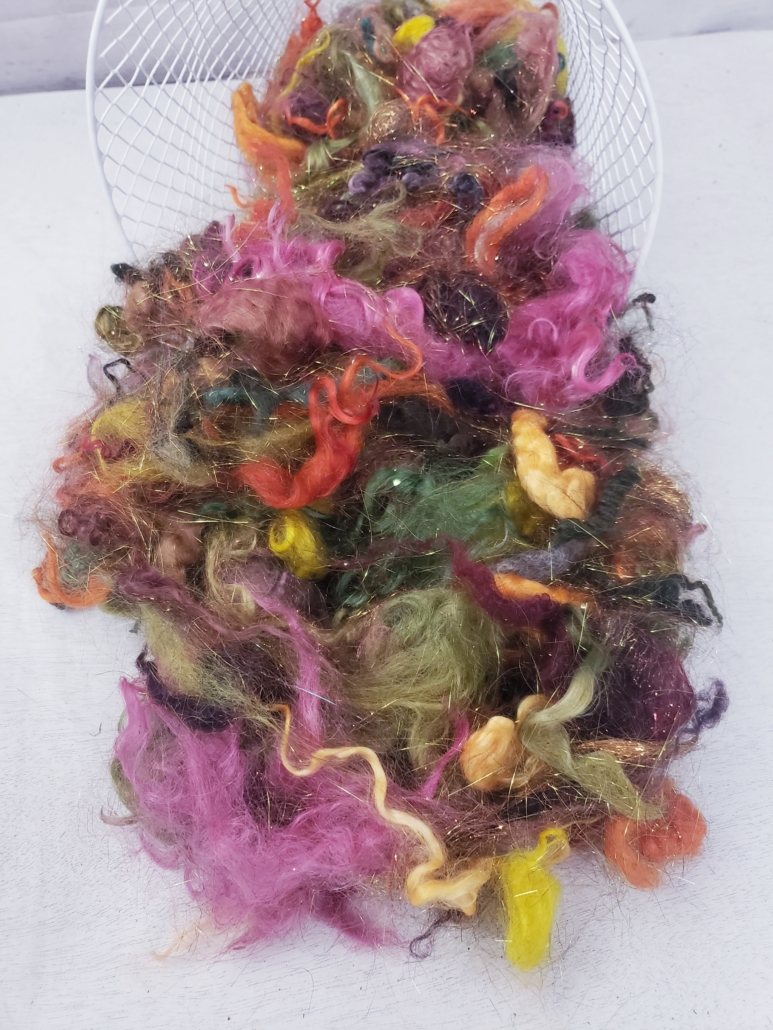
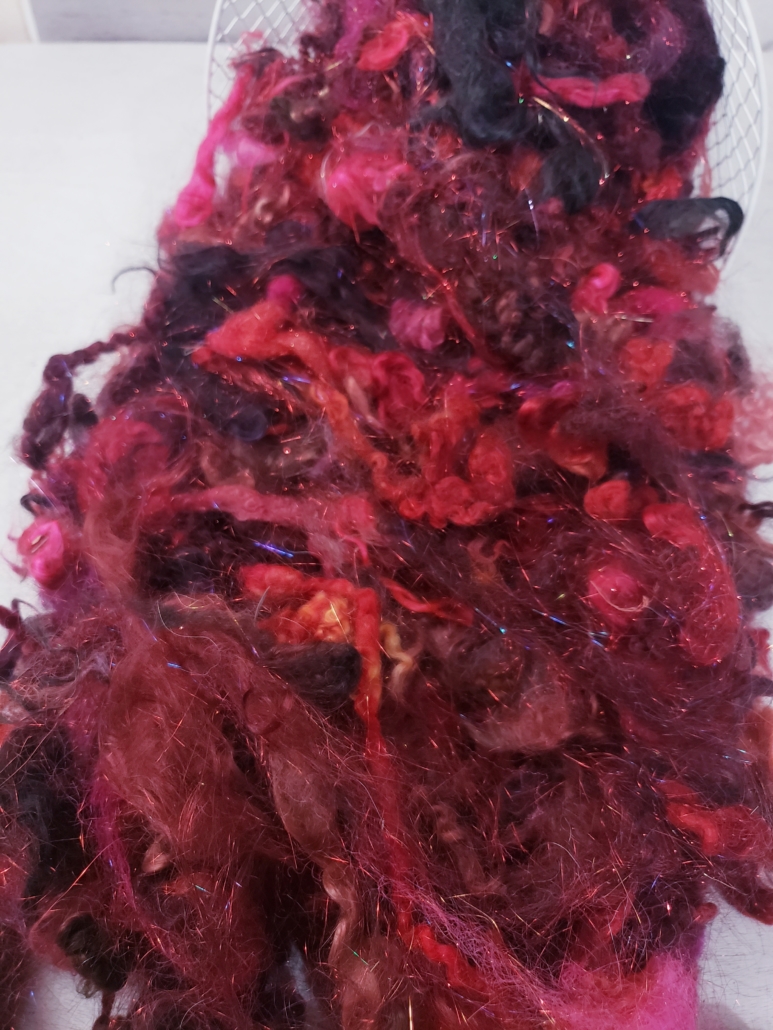
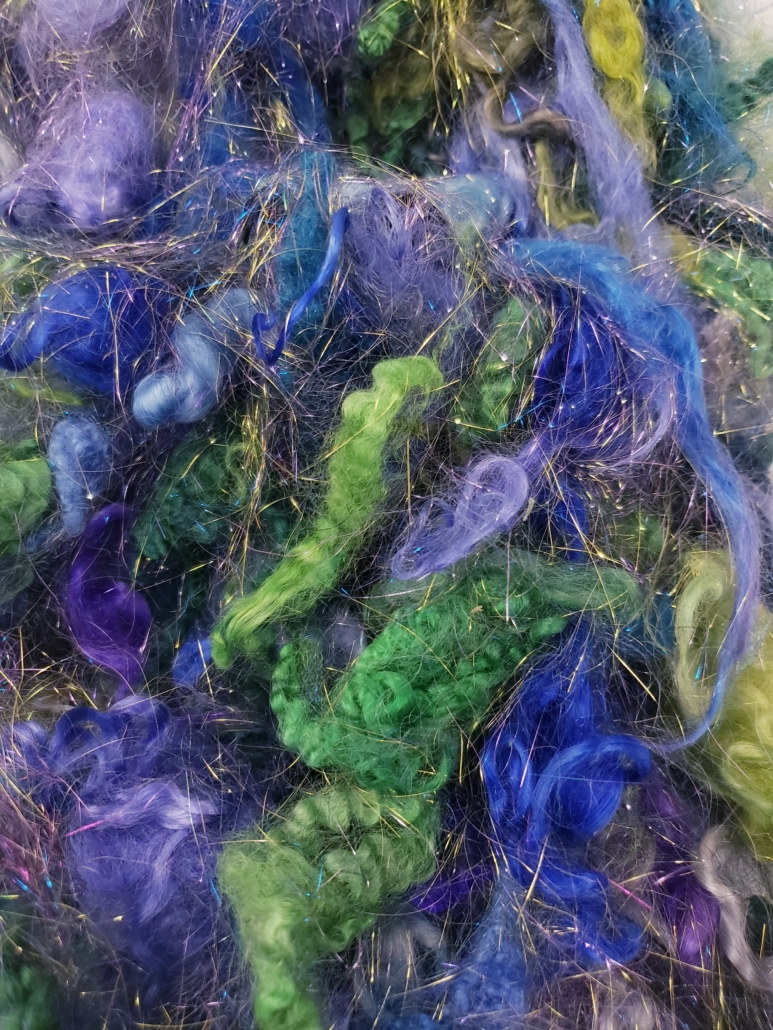
If Susan had to select three words to describe her Sparkle Fluff, she would choose:
Sparkle – because the Angelina throughout the fluff looks dazzling in the sunlight.
Shine – since mohair has a mirror-like shine.
Texture – the feel of so many different locks, wools, and fibers to be enjoyed however one wishes.
Spinning Sparkle Fluff
Chunky. Fine. Direct to wheel. Carding and blending.
Sparkle Fluff has no limits to its creative use. Susan’s favorite way to spin Sparkle Fluff is to take handfuls and let it flow through her wheel for a highly textured, bulky art yarn. She notes that Sparkle Fluff can also be lightly blended on a blending board for those who want more control over the texture and weight of their handspun.
Susan: I have seen other handspinners run a batch through a drum carder and spin it fine, with amazing results. As a person with curly hair, I appreciate the different textures of wool and mohair, and I like that my Sparkle Fluff preserves and highlights the texture of the locks.
Other surprising ways to use Sparkle Fluff: Fill little glass bottles with it and place those bottles around your studio to liven things up. Felt it into a gnome’s beard for some spice and color. Weave it into a wall hanging with some driftwood you picked up from the beach. The possibilities are endless!
As a parting thought to handspinners looking to start their next mohair spinning projects:
Susan: Don’t be afraid to try something new. A lot of spinners stick with wool because it’s a fiber they know. It takes courage to branch out and try something new. Especially when spinning with locks – you have to let go and let the locks flow. It is not precise. You are not looking for a specific twist direction or the perfect spinning ratio. Sometimes it takes a new spinner a long time to feel comfortable enough to be able to flow. But give it a try. Maybe you will get it right away, maybe you won’t, but just keep playing with it and practicing. I promise the Angora goats will keep growing fiber, so we won’t run out!
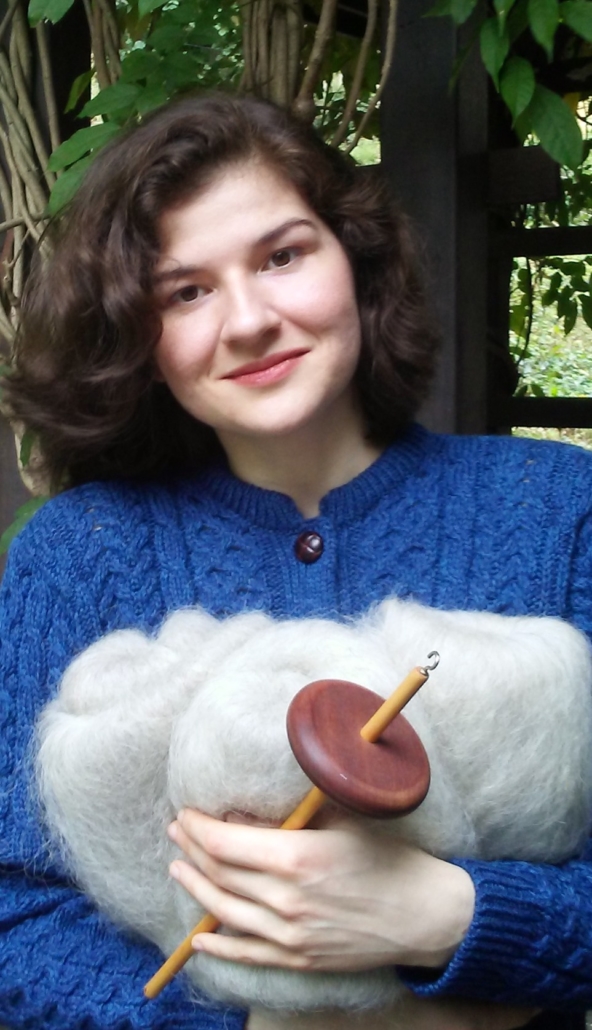
Jacqueline Harp is a freelance writer and multimedia fiber artist who spins, felts, weaves, crochets, and knits in every spare moment possible. She is also a certified Master Sorter of Wool Fibers through the State Univ. of N.Y. (Cobleskill) Sorter-Grader-Classer (SGC) Program. Her Instagram handle is @foreverfiber
Leave a Reply
Want to join the discussion?Feel free to contribute!