Mixing Things up for a Sweater
words and photos by: Johanna Carter
I always admire those who are able to spin mountains of yarn for a big project, ready to knit a wonderful sweater or cardigan. It is a satisfying feeling when you finish all that work, especially if you started with washing and combing the wool or even raising your own sheep.
Mixing spinning and knitting
The typical way to work through a larger project is to spin all the singles first and ply them in a particular order so you get the yarn even throughout the whole project. I don’t have so many bobbins, but my bigger problem is that I am quite impatient and want to get on with knitting once I have an idea. And normally, my brain is full of ideas for fibre work and the limit is the time, as I am a musician and teacher. I can’t sit at the spinning wheel for a long time if I’m not on holiday, so during the school year I mostly knit, and during the holidays I can dye, spin, use my drum carder, and do lots of fibre work. The only time I was able to produce bigger quantities of yarn before I knitted them up was during the Tour de Fleece in the two years during the pandemic, when we did not go on holiday at the beginning of July.
I like to finish knitting one big project like a sweater or cardigan before I start the next one, or at least until I can’t carry it in my bag easily anymore, so I have an excuse to begin the next one. Sometimes it is good to have a second project on the go – I call it mindless knitting, where I don’t have to look very much – which I can keep my hands busy during Zoom or other meetings, which helps me listen.
Mixing colours and fibres
Usually I dye my yarn with plants which I collect in the woods or get from garden flowers. I also use cochineal and indigo, which I buy, to get lots of different colours. I really love the greens and blues I get from dyeing with indigo. I have lots of dyed wool, and all those colours give me inspiration for further projects.
Blending the wool on the drum carder I can get even more shades. I like to blend with fibres like silk, alpaca, or plant fibres, and I love sari silk, to get those little bits of colour in my yarn.
When I have an idea for the next sweater, I start carding, and then I can begin to spin. Once I have spun enough yarn – say, for one day – I cast on and start knitting, usually top down, so I don’t have to decide too much in advance about length and width.
When I spin on my wheel, I have to sit at home, but while spinning I can read a book or talk to others during online meetings. I also like to spin on my spindles, and that works on a walk, or a museum visit. I take them on holiday as they don’t need much space, and when I spin for a lace shawl, I don’t even need much wool either. At home there are spindles all over the place; I can spin when I am waiting for the kettle to boil, when the computer is slow, when I am cooking. Like that I can make good use of a short time and the yarn still grows.
I can take my knitting almost everywhere, which is why I don’t want to wait to get started until I have spun all the yarn for a whole sweater. I knit at home, on the bus or train. The only thing I have to make sure of is to be one step ahead with the yarn.
I love to knit Fair Isle sweaters. My favourite method is to use only one bobbin, which I don’t even fill, because I need smaller quantities of lots of colours. Then I wind a ply ball and ply it on itself. For that I put my thumb through the ball, so I can tension the two singles with my fingers and they don’t get tangled, as long as my thumb (or a cardboard roll or a pencil) stays in the middle. I don’t have any leftovers from plying, and it is quick when I suddenly need more yarn.
I have never had problems with the yarn not being consistent enough throughout a project. I just know what yarn I want and my fingers seem to remember what to do. I am sure it is good advice to have a little card tied to the spinning wheel with a bit of the singles you are aiming for, so you can check and make sure you are spinning a consistent yarn.
Mixing breeds
There are so many different breeds, but some of my favourites are Shetland, BFL, and Jämtland – a Swedish breed. After dyeing them, I often forget what I have used, so when I do a new project it often turns out that I have used different breeds and fibres just to get the right colour. For the Fair Isle knitting I want to juggle lots of colours, which is more important to me than making a sweater out of only one breed.
Recently I made a pullover for my husband using about 12 different breeds and colours, even mixing short and long draw. For me it was a breed experiment and a way to use up lots of smaller quantities of wool I had in my stash. For that sweater I used combed top without blending.
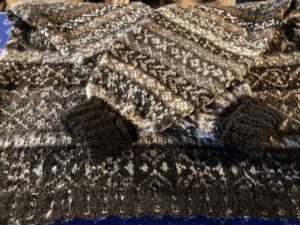
Mixing in knitting during the spinning process is a wonderful way for a spinner to avoid being overwhelmed during a sweater project.
My feeling is that some people don’t dare to start spinning for a bigger project because they get overwhelmed by the quantity they have to spin and then all the knitting there is to do, especially when you want to spin the yarn entirely on spindles. Mixing the spinning and knitting for the same project is more interesting; you get more variety and more freedom to choose what you want to do next as long as you don’t run out of yarn. It breaks the project down into smaller, less daunting parts. The only thing you might want to plan is to have enough fibre at the start, but even that is not necessary, there is always a sheep growing more wool.
PLY Guild: Second Season Drop – Episode 2
Ding! Ding! Ding!
The second episode of the second (worsted) season of the PLY Guild has dropped and is ready for your viewing pleasure!
- Four brand-spanking-new spinning segments
- Four great teachers: Deb Robson, Maggie Casey, Jillian Moreno, and Jacey!
- More than 2 hours of spinning content!
It’s a great episode filled with lots of information about choosing fibers for worsted yarns.
We’ll see you again with a new episode in six weeks (but in the meantime, come see us in a spin-in)! If you haven’t already gotten your membership, this is an episode you won’t want to miss!
PLY Spinners Guild is a space for spinners. We are an inclusive and diverse community that embraces all spinners committed to learning, growing, questioning, answering, and supporting their fellow guild members. We strongly believe that the more diverse our community is, the stronger our community is. Our core beliefs of kindness, diversity, and inclusivity inform everything we do. PSG supports people of every ability, ethnicity, race, religion, sex, and gender. We hold that every single community member is important. We believe that black and brown lives matter. We see and support our LGBTQ+ community. We reserve the right to remove anyone that meaningfully and purposefully disrupts the community or makes other members feel unsafe.
Third Thursdays Guild Tip
Time to ramp up for tonight’s PLY Spinners Guild Third Thursday foundational spin-in!
Here’s a tip to tide you over until the spin-in starts! This is something I’ve observed time and again during my years of teaching spinners.
When we first begin spinning with a short forward draw, many of us struggle to get a thin, even yarn. Much like a toddler who needs to master the chunky crayons before they can move on to the pencils, new spinners will spin lumpy, bumpy, chunky yarn until they master the fine motor control needed to get those lovely, even singles. Then comes the second part of this problem.
Once spinners master the thin, even single… it becomes really difficult for them to spin a thick yarn again. It is a skill they have to learn all over again and is often a shock when they realize they’ve lost the ability.
To work toward getting that thicker yarn again, pay attention to what each of your hands is doing as your spin. One hand manages the fiber supply (the fiber hand), while the other hand forms a pinch point and controls the twist (the working hand).
When you spin a fine single, you might notice that your pinch point stays near the very tips of the fibers and draws only a few fibers at a time into the twisted yarn. While not always the case, you might also notice that your fiber hand holds the fiber supply with a somewhat firm pressure.
To get a thicker yarn, move your pinch point deeper into the drafting triangle so that you are drawing up more fibers into the twist zone. To complement this new motion, your fiber hand should have a very loose grip on your fiber. If you hold your supply tightly, fewer fibers can be drawn into the twist zone.
Test this out at the spin-in, tonight! Make sure that you have joined the guild to get the Zoom link!
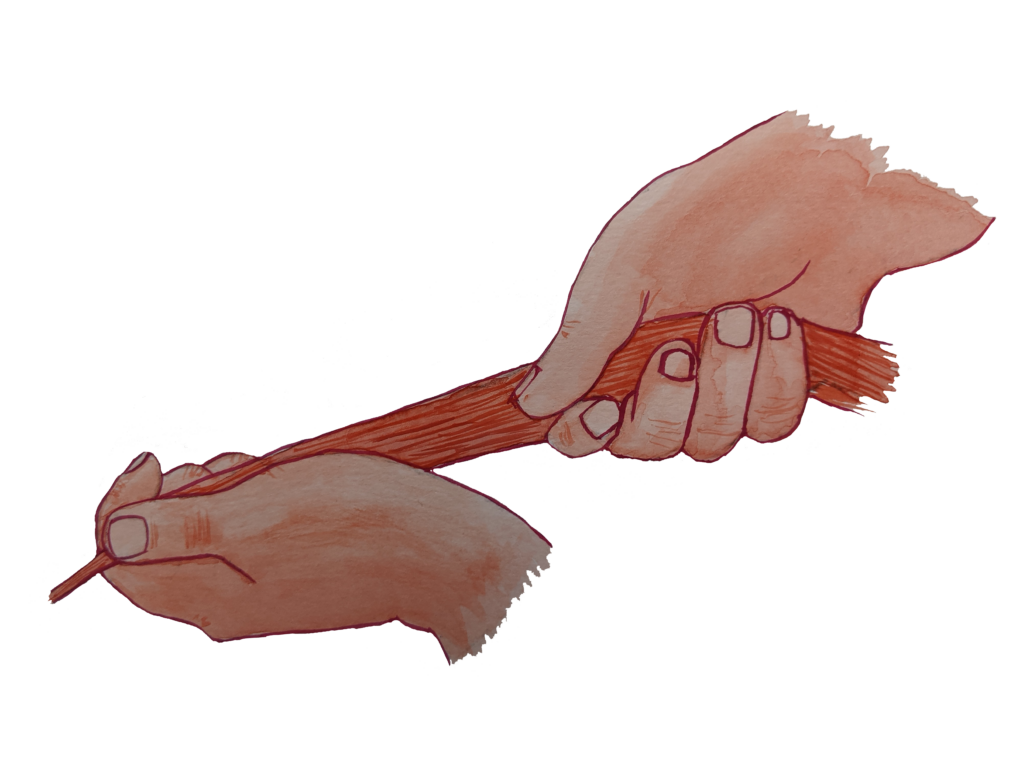
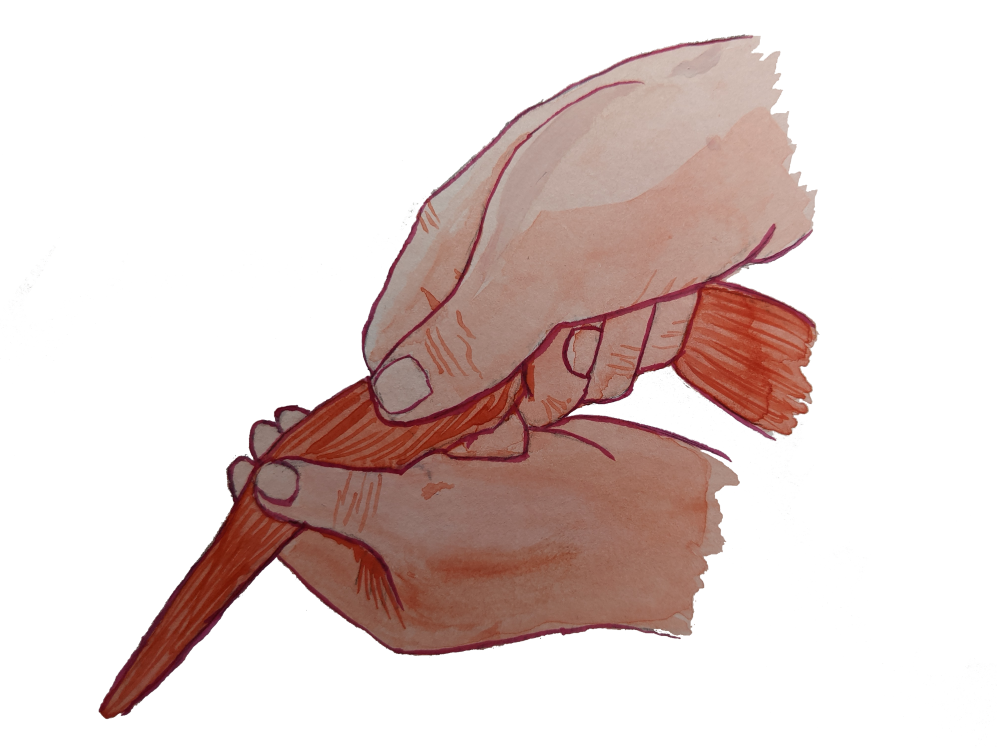
Ask Jillian: Parallel Drafting Tips
Dear Jillian,
I am having the worst time parallel drafting! My fibers don’t draft well, there’s clumping, and one color frequently falls away. Can you give me some tips to make it easier?
~Tess (and others) in Jillian’s class at Maryland Sheep and Wool
Hi Tess,
Parallel drafting may be my favorite color spinning technique, but it was super awkward for me when I first started. I felt like I was trying to spin with my toes!

Here are my tips to create an even marl in your singles so you can have wonderfully speckled and blended colors in your ply. I hope one or all of them work for you to make parallel drafting easier!
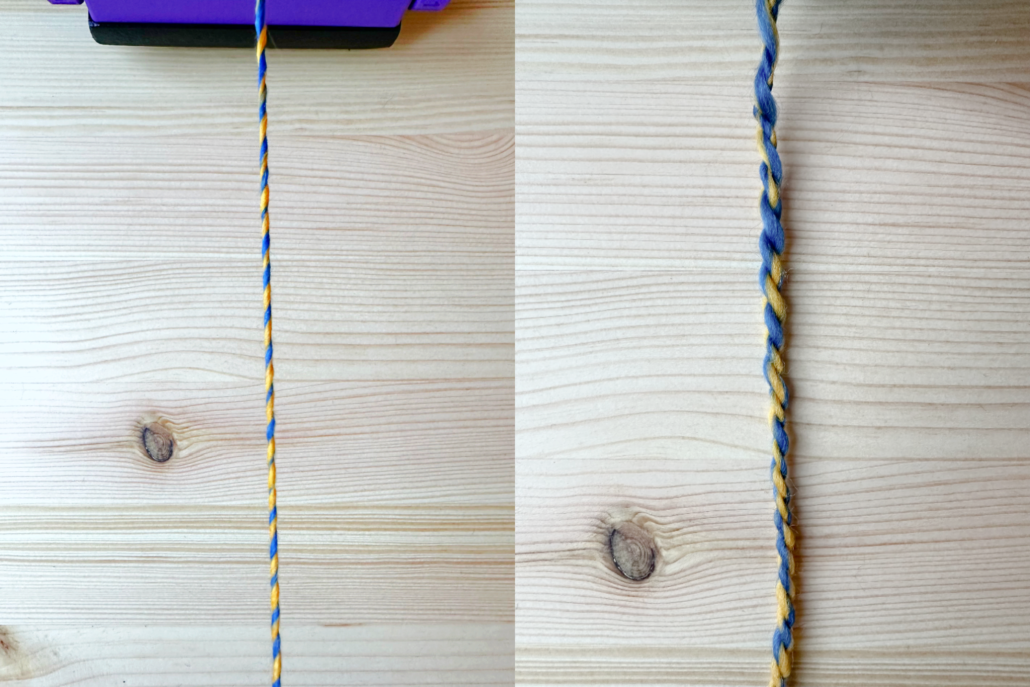
Fiber
It helps when you are first learning to parallel draft to use fibers that are close in staple length. Corriedale and Falkland or Merino and Polwarth are great places to start, and when those feel comfy, move to combos like Corriedale and BFL or Merino and Merino/silk. Keep practicing and you’ll get to the point where you can parallel draft almost any fibers together.
Preparing Your Fibers
This may be the most important tip: use less fiber than you want to. Not what you want to hear, I know, but it makes such a difference.
I measure my fiber with my fingers. I use two-fingers’ width of fiber, after it’s been fully fluffed.
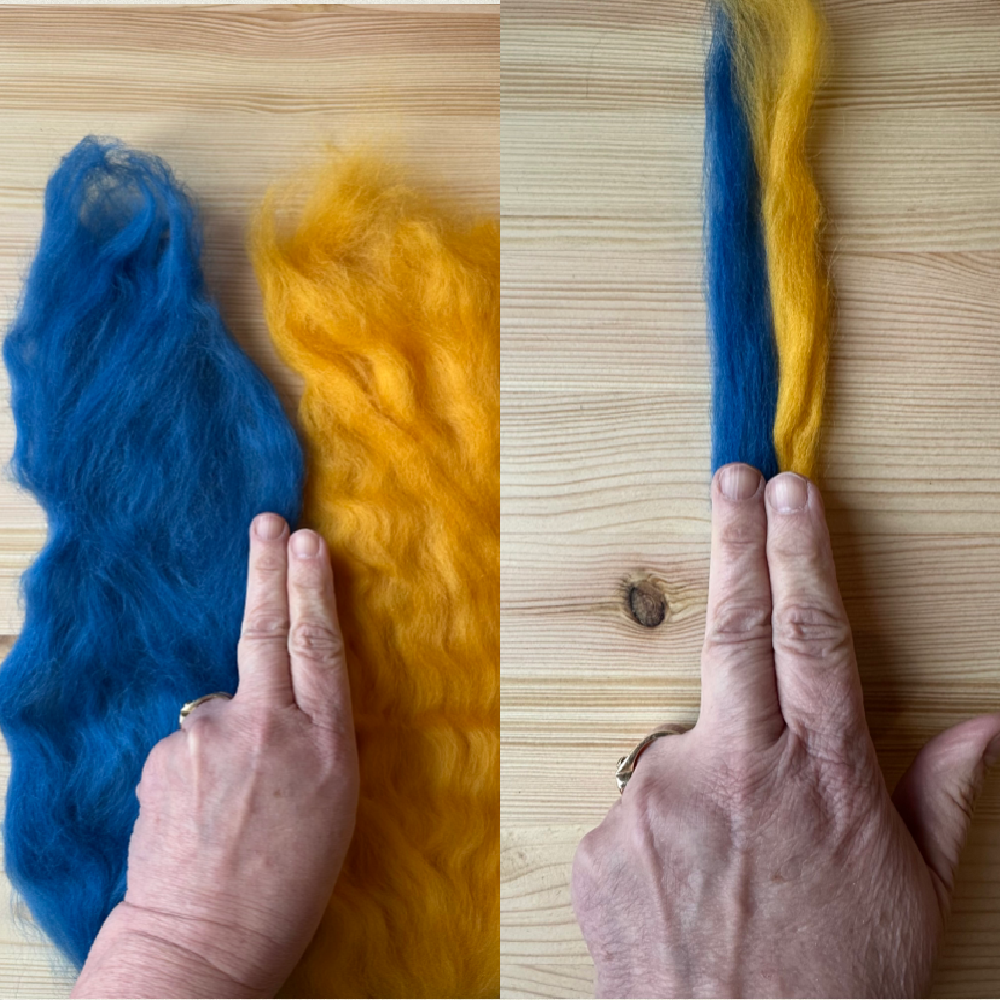
I open my fibers horizontally and measure the strips of fiber to use. If I am drafting two braids or two solid colors together, I use a finger’s width of each color; if I’m using a natural color and a braid, I use 2/3 of my two-finger’s width of the braid and 1/3 of the natural color.
It’s easy to try to parallel draft without opening your fibers all the way, but that leads to less-than-smooth drafting and clumping.
After I open and strip my fibers, I hold them side by side and pre-draft them together. I slowly, vertically attenuate them, which helps the fibers grab onto each other before drafting at the wheel even begins.
You can do it just with your hands, or you can pull them through a diz, using a handcard or comb to hold your fibers.
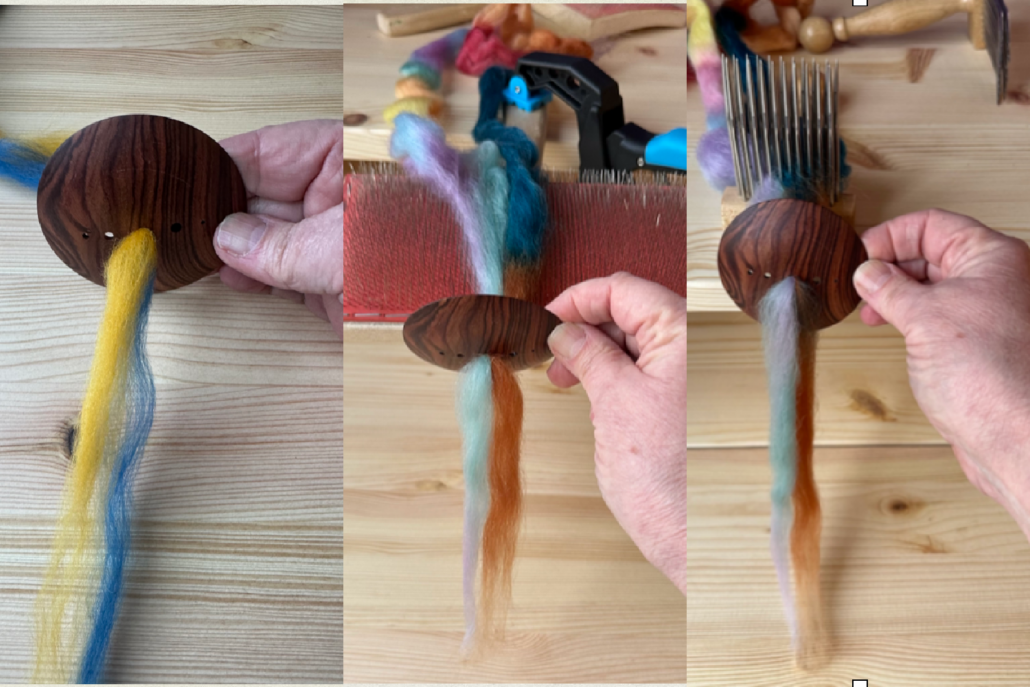
Tension and speed
One of the rudest things to say to a spinner is “slow down.” We want to get our yarn done fast so we can bask in its gorgeousness and get on to our next yarn. But if you slow down overall while you are learning to parallel draft, it makes a huge difference. Slowing down helps you draft more easily and keeps both fibers together.
Once you feel like you have the technique down, you can move back to Speed Racer mode.
Finding a way to equally tension the pieces of fiber will help keep one fiber from falling away while you are drafting. I’ve found that putting a finger from my fiber (back) hand in between the two strips of fiber allows me to tension them equally, change the tension between the two if one strip feels fatter, and notice quickly if one strip falls away.
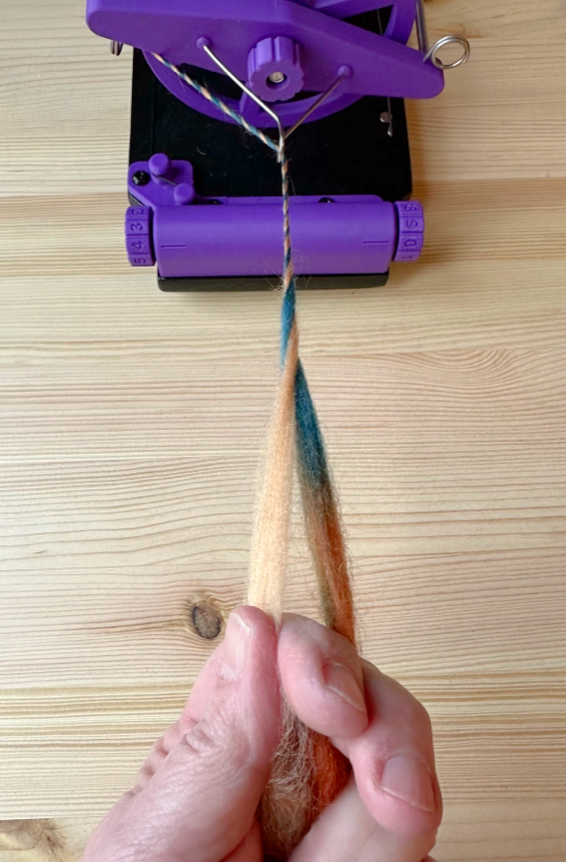
Want Jillian or Jacey to take a stab at your question? Tell us what you want to know:
Leave a Reply
Want to join the discussion?Feel free to contribute!