Mixing Things up for a Sweater
words and photos by: Johanna Carter
I always admire those who are able to spin mountains of yarn for a big project, ready to knit a wonderful sweater or cardigan. It is a satisfying feeling when you finish all that work, especially if you started with washing and combing the wool or even raising your own sheep.
Mixing spinning and knitting
The typical way to work through a larger project is to spin all the singles first and ply them in a particular order so you get the yarn even throughout the whole project. I don’t have so many bobbins, but my bigger problem is that I am quite impatient and want to get on with knitting once I have an idea. And normally, my brain is full of ideas for fibre work and the limit is the time, as I am a musician and teacher. I can’t sit at the spinning wheel for a long time if I’m not on holiday, so during the school year I mostly knit, and during the holidays I can dye, spin, use my drum carder, and do lots of fibre work. The only time I was able to produce bigger quantities of yarn before I knitted them up was during the Tour de Fleece in the two years during the pandemic, when we did not go on holiday at the beginning of July.
I like to finish knitting one big project like a sweater or cardigan before I start the next one, or at least until I can’t carry it in my bag easily anymore, so I have an excuse to begin the next one. Sometimes it is good to have a second project on the go – I call it mindless knitting, where I don’t have to look very much – which I can keep my hands busy during Zoom or other meetings, which helps me listen.
Mixing colours and fibres
Usually I dye my yarn with plants which I collect in the woods or get from garden flowers. I also use cochineal and indigo, which I buy, to get lots of different colours. I really love the greens and blues I get from dyeing with indigo. I have lots of dyed wool, and all those colours give me inspiration for further projects.
Blending the wool on the drum carder I can get even more shades. I like to blend with fibres like silk, alpaca, or plant fibres, and I love sari silk, to get those little bits of colour in my yarn.
When I have an idea for the next sweater, I start carding, and then I can begin to spin. Once I have spun enough yarn – say, for one day – I cast on and start knitting, usually top down, so I don’t have to decide too much in advance about length and width.
When I spin on my wheel, I have to sit at home, but while spinning I can read a book or talk to others during online meetings. I also like to spin on my spindles, and that works on a walk, or a museum visit. I take them on holiday as they don’t need much space, and when I spin for a lace shawl, I don’t even need much wool either. At home there are spindles all over the place; I can spin when I am waiting for the kettle to boil, when the computer is slow, when I am cooking. Like that I can make good use of a short time and the yarn still grows.
I can take my knitting almost everywhere, which is why I don’t want to wait to get started until I have spun all the yarn for a whole sweater. I knit at home, on the bus or train. The only thing I have to make sure of is to be one step ahead with the yarn.
I love to knit Fair Isle sweaters. My favourite method is to use only one bobbin, which I don’t even fill, because I need smaller quantities of lots of colours. Then I wind a ply ball and ply it on itself. For that I put my thumb through the ball, so I can tension the two singles with my fingers and they don’t get tangled, as long as my thumb (or a cardboard roll or a pencil) stays in the middle. I don’t have any leftovers from plying, and it is quick when I suddenly need more yarn.
I have never had problems with the yarn not being consistent enough throughout a project. I just know what yarn I want and my fingers seem to remember what to do. I am sure it is good advice to have a little card tied to the spinning wheel with a bit of the singles you are aiming for, so you can check and make sure you are spinning a consistent yarn.
Mixing breeds
There are so many different breeds, but some of my favourites are Shetland, BFL, and Jämtland – a Swedish breed. After dyeing them, I often forget what I have used, so when I do a new project it often turns out that I have used different breeds and fibres just to get the right colour. For the Fair Isle knitting I want to juggle lots of colours, which is more important to me than making a sweater out of only one breed.
Recently I made a pullover for my husband using about 12 different breeds and colours, even mixing short and long draw. For me it was a breed experiment and a way to use up lots of smaller quantities of wool I had in my stash. For that sweater I used combed top without blending.
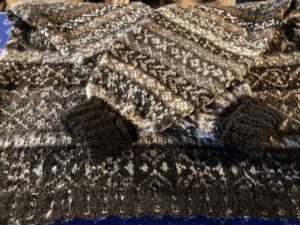
Mixing in knitting during the spinning process is a wonderful way for a spinner to avoid being overwhelmed during a sweater project.
My feeling is that some people don’t dare to start spinning for a bigger project because they get overwhelmed by the quantity they have to spin and then all the knitting there is to do, especially when you want to spin the yarn entirely on spindles. Mixing the spinning and knitting for the same project is more interesting; you get more variety and more freedom to choose what you want to do next as long as you don’t run out of yarn. It breaks the project down into smaller, less daunting parts. The only thing you might want to plan is to have enough fibre at the start, but even that is not necessary, there is always a sheep growing more wool.
Genesee Valley Handspinners Guild: Preserving the Ancient Art of Handspinning
by Ron Tyler
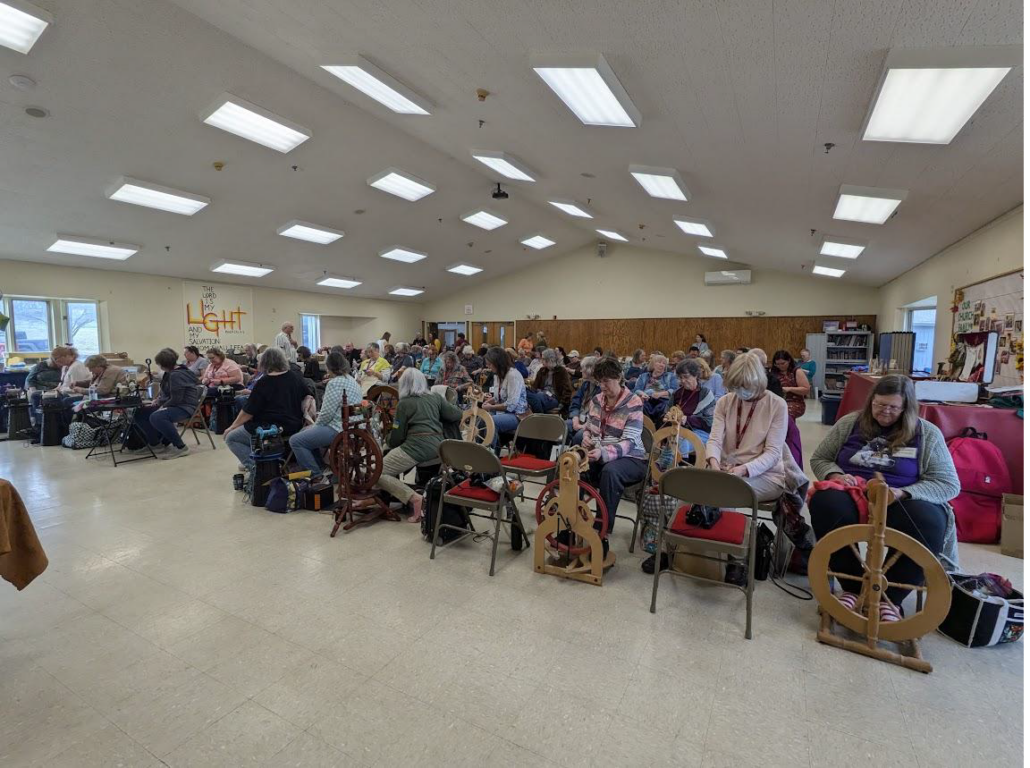
In the nineteenth century, the Genesee County area in upstate New York had many individuals spinning wool and flax to provide textiles for their families and for the barter system that provided many goods and services. Spinning was done on great wheels and saxony wheels that many pioneers brought with them across the state from the New England states. The main purpose was for clothing and to supply linens for their daily lives. Nearly every household was spinning for garments and weaving for textiles.
Upstate New York saw many heritage breeds of sheep, which were the main source of their spinning fiber–producing animals. Many farms in upstate New York also had many acres of flax growing. There were approximately 46 thousand acres of flax produced by families in upstate New York. That process was labor intensive to get linen for clothing and bedding.
In 1985 a small group of like-minded individuals formed the Genesee Valley Handspinners Guild. They had the tenacity and skill to develop their craft. The guild mission statement was to preserve the ancient art of handspinning and to educate themselves and the public on the history and skill of spinning fibers into yarn. Their skills expanded not only to spinning but to weaving, crochet, and knitting. In reality, it birthed a generation that used fibers for many arts and crafts today.
The spinning guild became the launching ground for many to become modern sheep farmers and mill owners to process wool. They educated many to work in textiles and in local museums to preserve that history. I, like many others, are the products of those wonderful individuals who formed the guild and educated their members in spinning, weaving, and the skills necessary to be successful spinners of wool, flax, and other fibers.
The early years of the guild saw many natural-colored sheep wool and fibers. The dawn of color and dyeing fibers brought many skills to spinning. Many spinners saw the creations of colorwork sweaters, garments, blankets, and many socks and shawls. This led into indie dyers and the frenzy of color in the hands of skilled spinners.
In 1995 the guild created The Finger Lakes Fiber Festival held at the local fairgrounds. This yearly festival ran for 25 years, eventually growing to offer over 80 venders and to attract thousands of people. This festival included many opportunities for demonstrations and educational classes. We have since scaled back and now offer The Shepherd’s Wool Market, which is a smaller event. We continue to offer demonstrations and educational classes to support our mission statement.
Our guild programs have been focused on the skills needed to be successful at individual endeavors, teaching skills in drafting techniques, fiber preparation, spinning wheel maintenance, and use of color. We have incorporated a sheep breed study that has delved into the breeds available and their uses for different textiles. We are gradually building our knowledge on the use of color, especially how to manipulate color at the spinning wheel with braids and the use of stash wool with parallel drafting techniques. We continue to strive and provide education for our members and the public. Occasionally our monthly meeting will consist of us sitting and spinning as a group with no agenda.
The Genesee Valley Handspinners Guild continues to this day, recently celebrating its 40th anniversary. We continue to be like-minded individuals preserving this ancient art of handspinning. Modern day spinning provides many guild members yards of yarn. Spinning provides a sense of pleasure, joy, therapy, and self care to the modern spinner, our guild members among them.
The challenge that the guild faces is bringing this craft to the next generation. We are using our collective experiences to encourage and refresh the guild’s presence in the next generation.
Ron Tyler, a retired nurse, is president of the Genesee Valley Handspinners Guild. He has been spinning for close to 20 years and is an avid collector of antique spinning wheels. He is also a historical interpreter in textiles at a local museum with an expertise in the history of flax.
Are you part of a fiber guild with a great history or a guild that is doing truly innovative work? We want to know about you!
By the Books: Using Older Texts to Inform Our Modern Understanding of Fiber
By Meagan Condon
I love the smell of old books. It is a smell that goes nicely with the smell of fresh fleece and hot coffee. My perfect afternoon would probably involve pivoting between scouring a fleece, one small bag at a time, and curling up in the living room next to a stack of old non-fiction books.
There seems to be a lot of crossover between book people and fiber people. It is part of why I spend so much time researching fiber arts. I love to play with fiber, but I am always looking for deeper meaning about how and why it behaves the way it does.
Right now, thanks to my local library, Sheep and Man by Michael L Ryder, an 856-page tome – and I do mean tome – published in the UK in 1983, sits half-read on my nightstand. Published more than 40 years ago, this book is touted by some to be the definitive work on the history of the domestication of sheep – which is interesting, considering it isn’t in publication and used copies are so rare they go for more than my car payment.
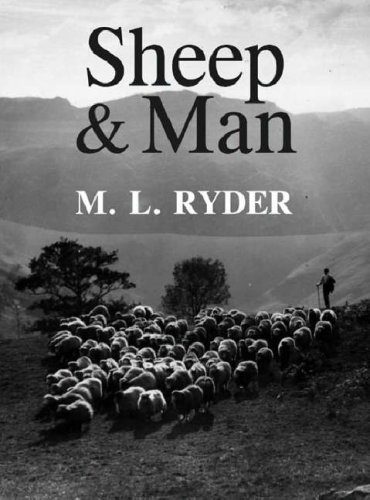
Definitive is a dangerous word, to me. It gives us the illusion that knowledge is finite and unchanging, neither of which is true. New science comes along and answers questions we didn’t have answers for, which changes our understanding of things we thought we knew. In the handspinning community, we are particularly at risk of thinking that the knowledge and history of the craft never changes. It worked 500 years ago, so it should work the same way today.
The truth is, as soon as something is published, it is outdated. As a general rule, I approach any text older than 10 years with this fact tucked neatly in the back of my mind, and as I read, I question just about every fact that I don’t already have a clear understanding of (and even some facts which I do).
For example, Ryder points out that the proteins in sheep and goat wool are different, which indicates they likely diverged evolutionarily before they were domesticated. This made me curious – did more current microscopy and DNA analysis support this? So I set my book down, picked up my tablet, and began to research the difference between goat and sheep hair proteins.
In my further research, I learned that wool and cashmere are primarily made from keratin, the same protein our hair and nails are made from. However, they contained different keratin-associated proteins (KRTAPs) and the arrangement and amount of these additional proteins was different.
In fact, KRTAPs not only differed between ruminant species but also proved to be a determining factor in how fine, strong, and flexible a fiber is within a breed of sheep or goats.
This gave me additional information in support of what Ryder said four decades ago. Ryder didn’t have all the answers, though it would have been easy for me to just accept his word on the matter. After all, he was the expert! That said, his voice wasn’t able to give me the full picture of how goat and sheep hair differed. What it gave me was the right questions to ask.
An hour and a half diversion from my book, a fresh cup of coffee, and 4 tablespoons of wool wash later, and I can finally move to the next paragraph, page 19. I’ve got a long afternoon ahead of me.
References
Li S, Xi Q, Zhao F, Wang J, He Z, Hu J, Liu X, Luo Y. “A highly polymorphic caprine keratin-associated protein gene identified and its effect on cashmere traits.” J Anim Sci. 2021 Sep 1;99(9):skab233. doi: 10.1093/jas/skab233. PMID: 34370022; PMCID: PMC8442941.
Ryder, M. L. (2007). Sheep & Man. Duckworth.
Zhang C, Qin Q, Liu Z, Xu X, Lan M, Xie Y, Wang Z, Li J, Liu Z. “Identification of the key proteins associated with different hair types in sheep and goats.” Front Genet. 2022 Sep 23;13:993192. doi: 10.3389/fgene.2022.993192. PMID: 36212123; PMCID: PMC9539809.
Zhanzhao, Chen & Cao, Jian & Zhao, Fang & He, Zhaohua & Sun, Hongxian & Wang, Jiqing & Liu, Xiu & Li, Shaobin. (2023). “Identification of the Keratin-Associated Protein 22-2 Gene in the Capra hircus and Association of Its Variation with Cashmere Traits.” Animals. 13. 2806. 10.3390/ani13172806.
Third Thursdays Guild Tips
As we ramp up for tonight’s PLY Spinners Guild Third Thursday foundational spin-in, we’d like to take a moment to feature some tips from one of our wonderful PLY Guild spin-in leaders, Terri Guerette.
What should I bring to a workshop?
Although not something to bring to a workshop, one of the reminders I often offer to people taking my workshops is to make sure your tetanus shots are up to date. We work with a lot of sharp tools that are sometimes used on raw fleece. So we really need to make sure we protect our health!
There are a lot of factors to consider when taking a workshop. How long is the workshop? Where is it being held? But the most important thing is to pay close attention to the class description for the items you should be bringing to class. If there is anything in the description that you are unsure of, please don’t hesitate to contact the instructor.
My next recommendation is to make sure your items are clearly marked with your name since many of us have the same or similar equipment.
Beyond that, you can consider bringing a myriad of things, including but not limited to a repair kit with the items you may need for your specific wheel; documentation supplies (notebook, pen/pencil, labels, bags); and personal care items (hand sanitizer, snacks, water bottle, throat lozenges).
Last but not least, it’s usually a good idea to have one or more of your shawls/sweaters with you because workshop environments can be quite varied. Besides, it’s so much fun to share the things we’ve made with our friends, old and new!
For a more in-depth discussion of this topic, see:
“The Ultimate Spinning Toolbag,” PLY Magazine (Winter 2017): 44–48
“Power Learning,” PLY Magazine (Autumn 2018): 34–37
Also, if you haven’t already seen the news…
Season two has begun!
The first episode of the second (worsted) season has dropped and is ready for your viewing pleasure!
- Four spinning segments
- Three teachers: Maggie Casey, Heavenly Bresser, and Jacey
- 2 hours of spinning content
- Jacey has included a new intro to the guild (which you should totally watch, it has lots of new info)
- And two teacher teas (from last year) for the teachers in this episode (which if you haven’t seen them yet, they’re delightful)
It’s a great episode filled with lots of worsted drafting, and it will get you ready for everything else we’re going to do this season.
Also a reminder! Sunday, April 20 there will be no guild spin-in!
This is Easter Sunday so we’ve decided to not hold the spin-in, but don’t worry, we’re going to make it up with a fantastic giveaway at the next Sunday spin-in. (Remember when we spent that whole spin-in looking at a fancy new carder? Well…)
Leave a Reply
Want to join the discussion?Feel free to contribute!