Mixing Things up for a Sweater
words and photos by: Johanna Carter
I always admire those who are able to spin mountains of yarn for a big project, ready to knit a wonderful sweater or cardigan. It is a satisfying feeling when you finish all that work, especially if you started with washing and combing the wool or even raising your own sheep.
Mixing spinning and knitting
The typical way to work through a larger project is to spin all the singles first and ply them in a particular order so you get the yarn even throughout the whole project. I don’t have so many bobbins, but my bigger problem is that I am quite impatient and want to get on with knitting once I have an idea. And normally, my brain is full of ideas for fibre work and the limit is the time, as I am a musician and teacher. I can’t sit at the spinning wheel for a long time if I’m not on holiday, so during the school year I mostly knit, and during the holidays I can dye, spin, use my drum carder, and do lots of fibre work. The only time I was able to produce bigger quantities of yarn before I knitted them up was during the Tour de Fleece in the two years during the pandemic, when we did not go on holiday at the beginning of July.
I like to finish knitting one big project like a sweater or cardigan before I start the next one, or at least until I can’t carry it in my bag easily anymore, so I have an excuse to begin the next one. Sometimes it is good to have a second project on the go – I call it mindless knitting, where I don’t have to look very much – which I can keep my hands busy during Zoom or other meetings, which helps me listen.
Mixing colours and fibres
Usually I dye my yarn with plants which I collect in the woods or get from garden flowers. I also use cochineal and indigo, which I buy, to get lots of different colours. I really love the greens and blues I get from dyeing with indigo. I have lots of dyed wool, and all those colours give me inspiration for further projects.
Blending the wool on the drum carder I can get even more shades. I like to blend with fibres like silk, alpaca, or plant fibres, and I love sari silk, to get those little bits of colour in my yarn.
When I have an idea for the next sweater, I start carding, and then I can begin to spin. Once I have spun enough yarn – say, for one day – I cast on and start knitting, usually top down, so I don’t have to decide too much in advance about length and width.
When I spin on my wheel, I have to sit at home, but while spinning I can read a book or talk to others during online meetings. I also like to spin on my spindles, and that works on a walk, or a museum visit. I take them on holiday as they don’t need much space, and when I spin for a lace shawl, I don’t even need much wool either. At home there are spindles all over the place; I can spin when I am waiting for the kettle to boil, when the computer is slow, when I am cooking. Like that I can make good use of a short time and the yarn still grows.
I can take my knitting almost everywhere, which is why I don’t want to wait to get started until I have spun all the yarn for a whole sweater. I knit at home, on the bus or train. The only thing I have to make sure of is to be one step ahead with the yarn.
I love to knit Fair Isle sweaters. My favourite method is to use only one bobbin, which I don’t even fill, because I need smaller quantities of lots of colours. Then I wind a ply ball and ply it on itself. For that I put my thumb through the ball, so I can tension the two singles with my fingers and they don’t get tangled, as long as my thumb (or a cardboard roll or a pencil) stays in the middle. I don’t have any leftovers from plying, and it is quick when I suddenly need more yarn.
I have never had problems with the yarn not being consistent enough throughout a project. I just know what yarn I want and my fingers seem to remember what to do. I am sure it is good advice to have a little card tied to the spinning wheel with a bit of the singles you are aiming for, so you can check and make sure you are spinning a consistent yarn.
Mixing breeds
There are so many different breeds, but some of my favourites are Shetland, BFL, and Jämtland – a Swedish breed. After dyeing them, I often forget what I have used, so when I do a new project it often turns out that I have used different breeds and fibres just to get the right colour. For the Fair Isle knitting I want to juggle lots of colours, which is more important to me than making a sweater out of only one breed.
Recently I made a pullover for my husband using about 12 different breeds and colours, even mixing short and long draw. For me it was a breed experiment and a way to use up lots of smaller quantities of wool I had in my stash. For that sweater I used combed top without blending.
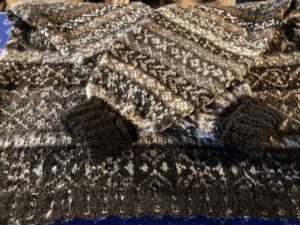
Mixing in knitting during the spinning process is a wonderful way for a spinner to avoid being overwhelmed during a sweater project.
My feeling is that some people don’t dare to start spinning for a bigger project because they get overwhelmed by the quantity they have to spin and then all the knitting there is to do, especially when you want to spin the yarn entirely on spindles. Mixing the spinning and knitting for the same project is more interesting; you get more variety and more freedom to choose what you want to do next as long as you don’t run out of yarn. It breaks the project down into smaller, less daunting parts. The only thing you might want to plan is to have enough fibre at the start, but even that is not necessary, there is always a sheep growing more wool.
Breed Development through Upgrading
Many of the sheep breeds found in the United States are being developed through a technique called upgrading. The United States (like many European countries) has strict regulations on the importation and exportation of live animals and particular breeds. As a result, there are many wonderful sheep breeds that can’t be brought into the United States, like Gotland, Teeswater, Herdwick, Bluefaced Leicester, and Black Welsh Mountain. And yet there are American flocks of all these breeds!
While we can’t import these sheep, we can import semen. A breeder will choose a breed that is close to the breed they want. For example, if a breeder wants Teeswater, they might choose another longwool breed like Leicester Longwool. A Leicester Longwool ewe is inseminated with semen from a Teeswater sheep. The result is a 50/50 genetic blend. This second-generation sheep is then inseminated with Teeswater semen. The resulting lamb is 75/25 Teeswater.
This process is continued until the sheep being bred have primarily Teeswater genes. An upgraded flock will never be 100 percent genetically the same as the original breed. American Teeswater may be 95–99 percent Teeswater. But chances are you or I would not be able to tell the difference unless one population or the other were heavily modified.
At this time, Valais Blacknose – the cutest sheep in the world – are being introduced to the United States via upgrading.
Upgrading is one way we can help preserve breeds and populations that are rare or threatened. Sometimes there aren’t enough sheep left in a population to have sustainable genetic diversity. Upgrading offers a solution for saving threatened breeds.
Have you ever spun a fleece from an upgraded sheep? If so, what genetic percentages did it have? What qualities did the fleece have?
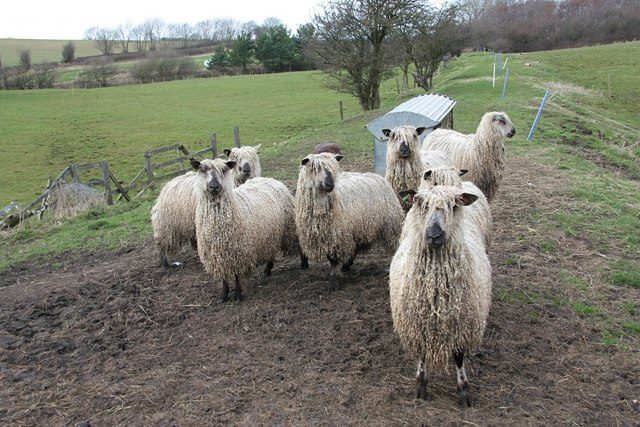
Book Review: Swatch Critters by Deb Essen
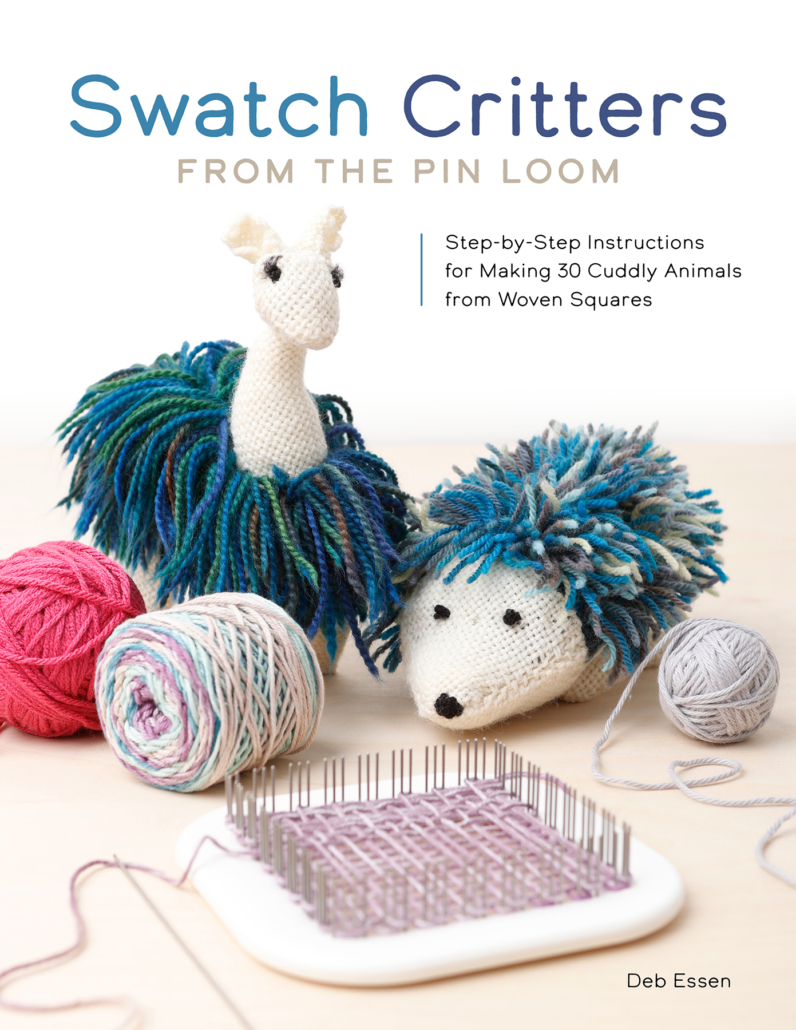
Swatch Critters from the Pin Loom: Step-by-Step Instructions for Making 30 Cuddly Animals from Woven Squares
by Deb Essen
Publisher: Schiffer Craft
US$24.99, 168 pages
Publication date: August 28, 2025
Buy now at Bookshop.org
Review by Meagan Condon
I am usually hesitant to review pattern books, in part because it takes so long to test out the patterns and I sample far more than I do actual projects. However, Essen managed to set the hook (a size G crochet hook, if you were wondering) and reel me in for this one.
I have always loved pin loom swatches, and I have an ongoing affair with my Schacht Zoom Loom. I could make little woven squares all day. However, like many others who have taken to the pin loom, I have an unruly stack of said squares that spill out of my stash in anxiety-inducing disarray.
I’ve looked for ways to use them, but I’ve never been terribly impressed by most of the patterns out there. I’ve found that patterns for using pin loom squares tend to be overly simplified and clumsy. And a scrappy swatch blanket just doesn’t appeal to me.
Essen’s work immediately caught my eye. The creativity and complexity of the designs goes beyond what I’ve seen in other pin loom pattern books. From Eureka the Unicorn to Pablo the Peacock, the patterns are all adorable. Critters for the win.
Essen also does a great job explaining how to use a pin loom. Being a left-handed crafter, I found it particularly useful that she included instructions for using the Zoom Loom both left- and right-handed. All of her instructions are clear and concise and the photos are helpful in visually explaining the text.
After the critter patterns, Essen includes some weaving patterns to add texture to your swatch squares, a great way to customize your critters.
If you are looking for a way to use up all the scrappy bits of handspun in your stash quickly, this will do it with flair!
How Tariffs are Impacting Fiber Arts in the US
In the United States, the president works with Congress to create US tariff policy. A tariff is a tax imposed by a government on goods and products imported from another country. The round of tariffs that was implemented most recently is having an impact on the spinning community, and you may not even realize it yet.
As of the publishing of this article, in the United States, the US president recently escalated a trade war with China, raising tariffs to 145 percent, then agreed to lower them to 10 percent, though tariffs on most Chinese goods are still over 30 percent due to existing duties. The president has also threatened to impose 50 percent tariffs on the EU, though that action is on pause. Tariffs for Canada and Mexico have been set at 25 percent on most goods. And there is a minimum tariff of 10 percent on most other countries. That means if you import spindles from Canada for $10 each, the tariff raises the price to $12.50.
Who pays this import tax? Well, the person or company that imports the item pays the tax. However, it doesn’t end there. That importer increases the price they sell the item for to help them maintain their profit margin. The dyer or spinner or yarn store that buys the wholesale products from the importer is then forced to increase their prices so they can make a living off their dyeing or spinning or reselling. Then you, the customer, spend more of your money to get your dyed or carded fiber or that fancy spinning wheel. So ultimately, tariffs come directly out of our pockets.
Ashford operates out of New Zealand. Louët wheels are manufactured in the Netherlands. A majority of our silk products come from China.
Why don’t we just buy US products, then? Many of our US producers, like Clemes and Clemes, have already taken steps to make as much of their product as possible in the United States. As a result, their prices have managed to stay relatively stable.
Very little of what we use is entirely made in the US, though. Wheels and carders and other tools use imported parts, even if they are constructed here. We simply don’t have the infrastructure to produce all of our fiber and tool parts here. We are lucky to have companies that are working to build the infrastructure, but that doesn’t happen overnight and it isn’t necessarily going to make the product cheaper for consumers. Our spinning community primarily operates as a recreational industry. Hobby and recreation are often hit the hardest when prices systematically increase.
What can you do?
Buy fiber locally. While silk is sexy, there are a ton of wonderful, underappreciated local wools and plant fibers. There is a revival in commercial flax here in the United States. Small farms across the country produce rare and interesting breeds of sheep.
Buying new tools is trickier, but luckily, our biggest imported tool names tend to be in places that are impacted less by the tariffs. We also have an amazing number of independent woodworkers here in the United States that produce and repair fiber tools, if you know where to look and who to ask.
And always, make use of your stash! Every fiber artist has one (or is in the process of building one). I can’t count the number of times I’ve complained that I have too much fiber. This may be a good impetus to use some of it!
Leave a Reply
Want to join the discussion?Feel free to contribute!