Mixing Things up for a Sweater
words and photos by: Johanna Carter
I always admire those who are able to spin mountains of yarn for a big project, ready to knit a wonderful sweater or cardigan. It is a satisfying feeling when you finish all that work, especially if you started with washing and combing the wool or even raising your own sheep.
Mixing spinning and knitting
The typical way to work through a larger project is to spin all the singles first and ply them in a particular order so you get the yarn even throughout the whole project. I don’t have so many bobbins, but my bigger problem is that I am quite impatient and want to get on with knitting once I have an idea. And normally, my brain is full of ideas for fibre work and the limit is the time, as I am a musician and teacher. I can’t sit at the spinning wheel for a long time if I’m not on holiday, so during the school year I mostly knit, and during the holidays I can dye, spin, use my drum carder, and do lots of fibre work. The only time I was able to produce bigger quantities of yarn before I knitted them up was during the Tour de Fleece in the two years during the pandemic, when we did not go on holiday at the beginning of July.
I like to finish knitting one big project like a sweater or cardigan before I start the next one, or at least until I can’t carry it in my bag easily anymore, so I have an excuse to begin the next one. Sometimes it is good to have a second project on the go – I call it mindless knitting, where I don’t have to look very much – which I can keep my hands busy during Zoom or other meetings, which helps me listen.
Mixing colours and fibres
Usually I dye my yarn with plants which I collect in the woods or get from garden flowers. I also use cochineal and indigo, which I buy, to get lots of different colours. I really love the greens and blues I get from dyeing with indigo. I have lots of dyed wool, and all those colours give me inspiration for further projects.
Blending the wool on the drum carder I can get even more shades. I like to blend with fibres like silk, alpaca, or plant fibres, and I love sari silk, to get those little bits of colour in my yarn.
When I have an idea for the next sweater, I start carding, and then I can begin to spin. Once I have spun enough yarn – say, for one day – I cast on and start knitting, usually top down, so I don’t have to decide too much in advance about length and width.
When I spin on my wheel, I have to sit at home, but while spinning I can read a book or talk to others during online meetings. I also like to spin on my spindles, and that works on a walk, or a museum visit. I take them on holiday as they don’t need much space, and when I spin for a lace shawl, I don’t even need much wool either. At home there are spindles all over the place; I can spin when I am waiting for the kettle to boil, when the computer is slow, when I am cooking. Like that I can make good use of a short time and the yarn still grows.
I can take my knitting almost everywhere, which is why I don’t want to wait to get started until I have spun all the yarn for a whole sweater. I knit at home, on the bus or train. The only thing I have to make sure of is to be one step ahead with the yarn.
I love to knit Fair Isle sweaters. My favourite method is to use only one bobbin, which I don’t even fill, because I need smaller quantities of lots of colours. Then I wind a ply ball and ply it on itself. For that I put my thumb through the ball, so I can tension the two singles with my fingers and they don’t get tangled, as long as my thumb (or a cardboard roll or a pencil) stays in the middle. I don’t have any leftovers from plying, and it is quick when I suddenly need more yarn.
I have never had problems with the yarn not being consistent enough throughout a project. I just know what yarn I want and my fingers seem to remember what to do. I am sure it is good advice to have a little card tied to the spinning wheel with a bit of the singles you are aiming for, so you can check and make sure you are spinning a consistent yarn.
Mixing breeds
There are so many different breeds, but some of my favourites are Shetland, BFL, and Jämtland – a Swedish breed. After dyeing them, I often forget what I have used, so when I do a new project it often turns out that I have used different breeds and fibres just to get the right colour. For the Fair Isle knitting I want to juggle lots of colours, which is more important to me than making a sweater out of only one breed.
Recently I made a pullover for my husband using about 12 different breeds and colours, even mixing short and long draw. For me it was a breed experiment and a way to use up lots of smaller quantities of wool I had in my stash. For that sweater I used combed top without blending.
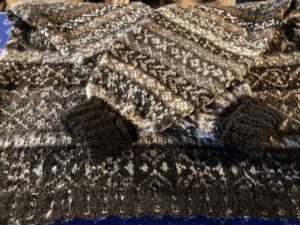
Mixing in knitting during the spinning process is a wonderful way for a spinner to avoid being overwhelmed during a sweater project.
My feeling is that some people don’t dare to start spinning for a bigger project because they get overwhelmed by the quantity they have to spin and then all the knitting there is to do, especially when you want to spin the yarn entirely on spindles. Mixing the spinning and knitting for the same project is more interesting; you get more variety and more freedom to choose what you want to do next as long as you don’t run out of yarn. It breaks the project down into smaller, less daunting parts. The only thing you might want to plan is to have enough fibre at the start, but even that is not necessary, there is always a sheep growing more wool.
How Tariffs are Impacting Fiber Arts in the US
In the United States, the president works with Congress to create US tariff policy. A tariff is a tax imposed by a government on goods and products imported from another country. The round of tariffs that was implemented most recently is having an impact on the spinning community, and you may not even realize it yet.
As of the publishing of this article, in the United States, the US president recently escalated a trade war with China, raising tariffs to 145 percent, then agreed to lower them to 10 percent, though tariffs on most Chinese goods are still over 30 percent due to existing duties. The president has also threatened to impose 50 percent tariffs on the EU, though that action is on pause. Tariffs for Canada and Mexico have been set at 25 percent on most goods. And there is a minimum tariff of 10 percent on most other countries. That means if you import spindles from Canada for $10 each, the tariff raises the price to $12.50.
Who pays this import tax? Well, the person or company that imports the item pays the tax. However, it doesn’t end there. That importer increases the price they sell the item for to help them maintain their profit margin. The dyer or spinner or yarn store that buys the wholesale products from the importer is then forced to increase their prices so they can make a living off their dyeing or spinning or reselling. Then you, the customer, spend more of your money to get your dyed or carded fiber or that fancy spinning wheel. So ultimately, tariffs come directly out of our pockets.
Ashford operates out of New Zealand. Louët wheels are manufactured in the Netherlands. A majority of our silk products come from China.
Why don’t we just buy US products, then? Many of our US producers, like Clemes and Clemes, have already taken steps to make as much of their product as possible in the United States. As a result, their prices have managed to stay relatively stable.
Very little of what we use is entirely made in the US, though. Wheels and carders and other tools use imported parts, even if they are constructed here. We simply don’t have the infrastructure to produce all of our fiber and tool parts here. We are lucky to have companies that are working to build the infrastructure, but that doesn’t happen overnight and it isn’t necessarily going to make the product cheaper for consumers. Our spinning community primarily operates as a recreational industry. Hobby and recreation are often hit the hardest when prices systematically increase.
What can you do?
Buy fiber locally. While silk is sexy, there are a ton of wonderful, underappreciated local wools and plant fibers. There is a revival in commercial flax here in the United States. Small farms across the country produce rare and interesting breeds of sheep.
Buying new tools is trickier, but luckily, our biggest imported tool names tend to be in places that are impacted less by the tariffs. We also have an amazing number of independent woodworkers here in the United States that produce and repair fiber tools, if you know where to look and who to ask.
And always, make use of your stash! Every fiber artist has one (or is in the process of building one). I can’t count the number of times I’ve complained that I have too much fiber. This may be a good impetus to use some of it!
SCENE: Upcoming Events
You are SCENE! Feast your eyeballs on these upcoming fiber events submitted by our readers!
July 11 – 13: Wyoming Sheep & Wool Festival, Buffalo, Wyoming
July 19 – 20: Fiber U, Lebanon, Missouri
July 25 – 26: Fiber Christmas in July, Kellyville, Oklahoma
July 26 – 27: Prairie City Fiber Fest, Prairie City, Oregon
PLY strives to bring together the global spinning community and give a voice to spinners everywhere. Is there an upcoming event you’d like to share? Do you have or know of a new product, fiber, or tool you think the community should know about? If so, fill out this form!
Once a month, we’ll feature SCENE content on the blog and social media.
What are you waiting for? Let us know what’s cool, hep, lit, fire in your fiber world!
What’s in this issue? Summer 2025 – Tension!
Tension is one of those elements we use all the time while we spin. We’ve got a whole issue packed full of great information on how tension figures into and impacts your spinning!
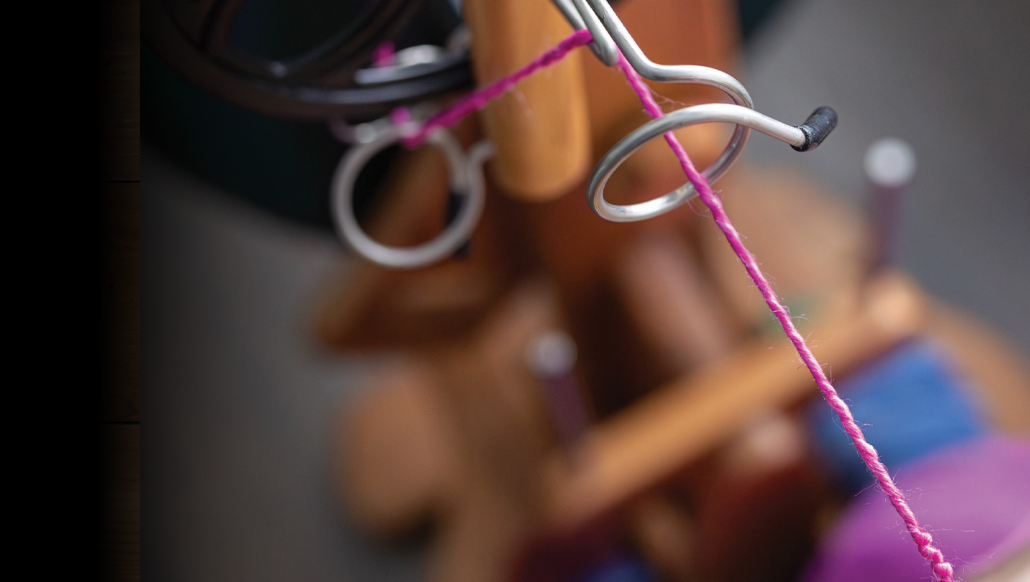
Wheel tension and wheel systems: How do they work and which works best for what type of yarn? James Perry and Heavenly Bresser teach us about break bands and drive bands respectively. Maggie Casey has broken down how tension operates in different wheel drive systems.
Tensile strength is all about how much tension a fiber can be put under before it breaks. Jill Duarte treats us to a look at how she accomplishes no-nep carding on the drum carder.
How about visual tension? Why do some colors seem to vibrate and explode when they are next to each other? Dia Patrece Robinson and Emily Wohlscheid have our backs when it comes to color. They talk about different methods to obtain a swirled colorway.
Tension can be good for yarn, but bad for our bodies. Andrea Deck talks to us about the science of stress relief and Andrea Lui has us covered for hand care with an article focused on proactive care and avoiding hand strain.
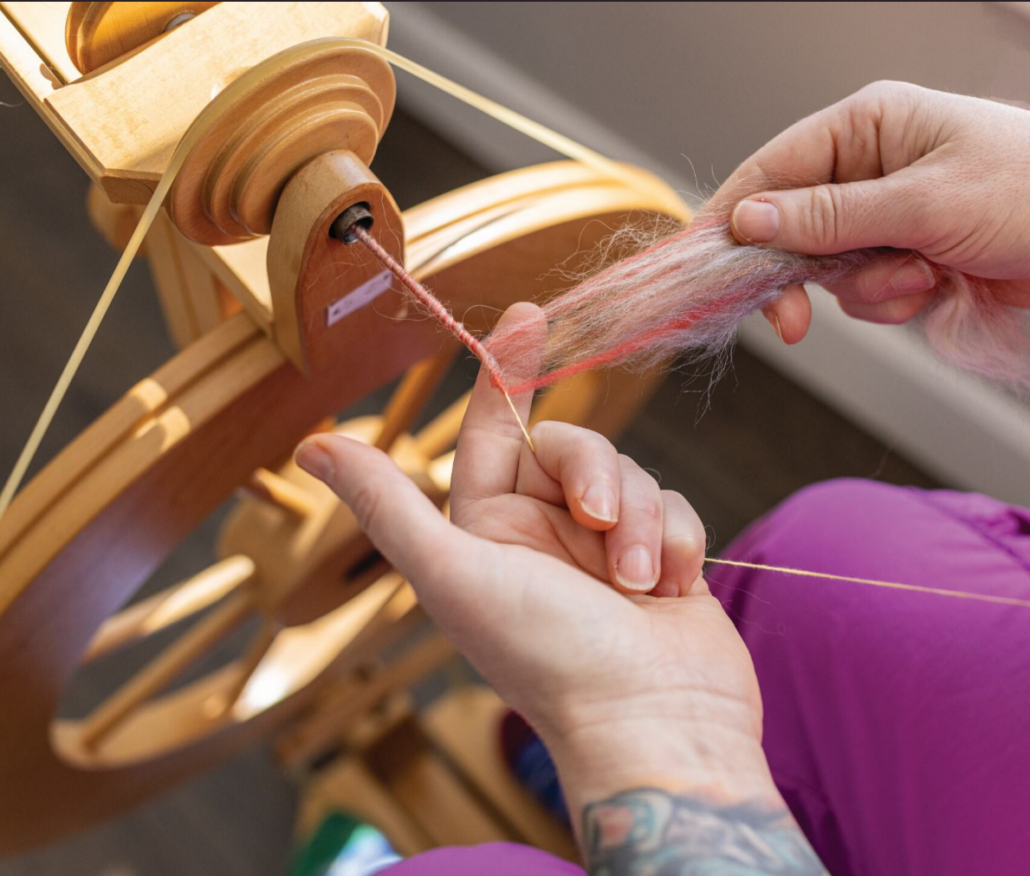
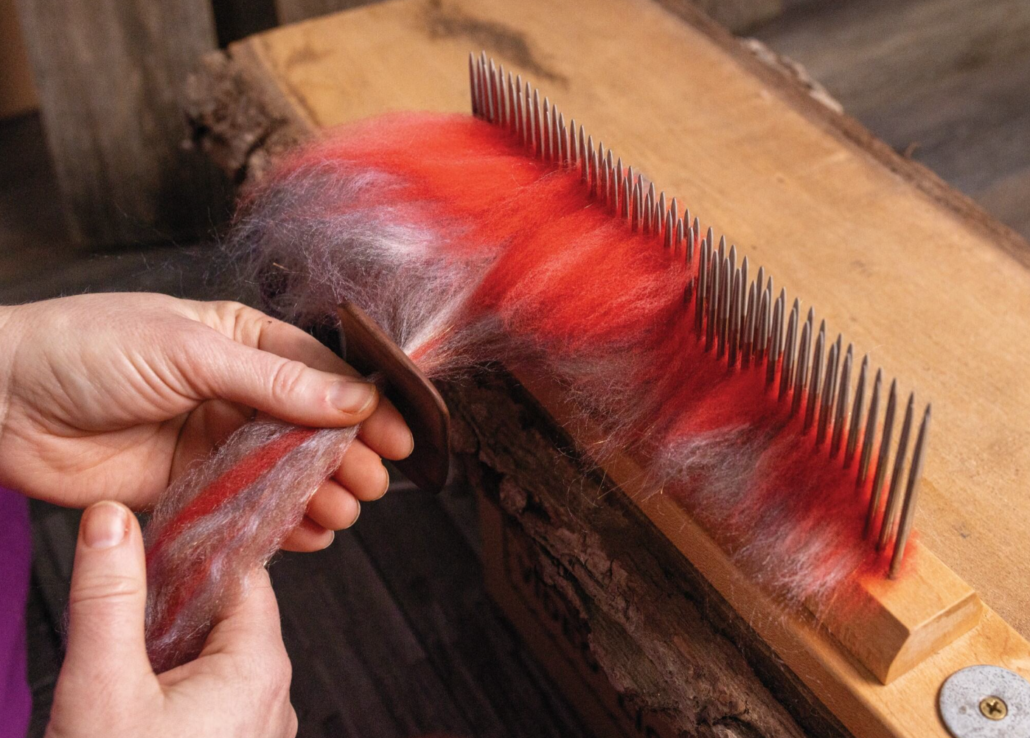
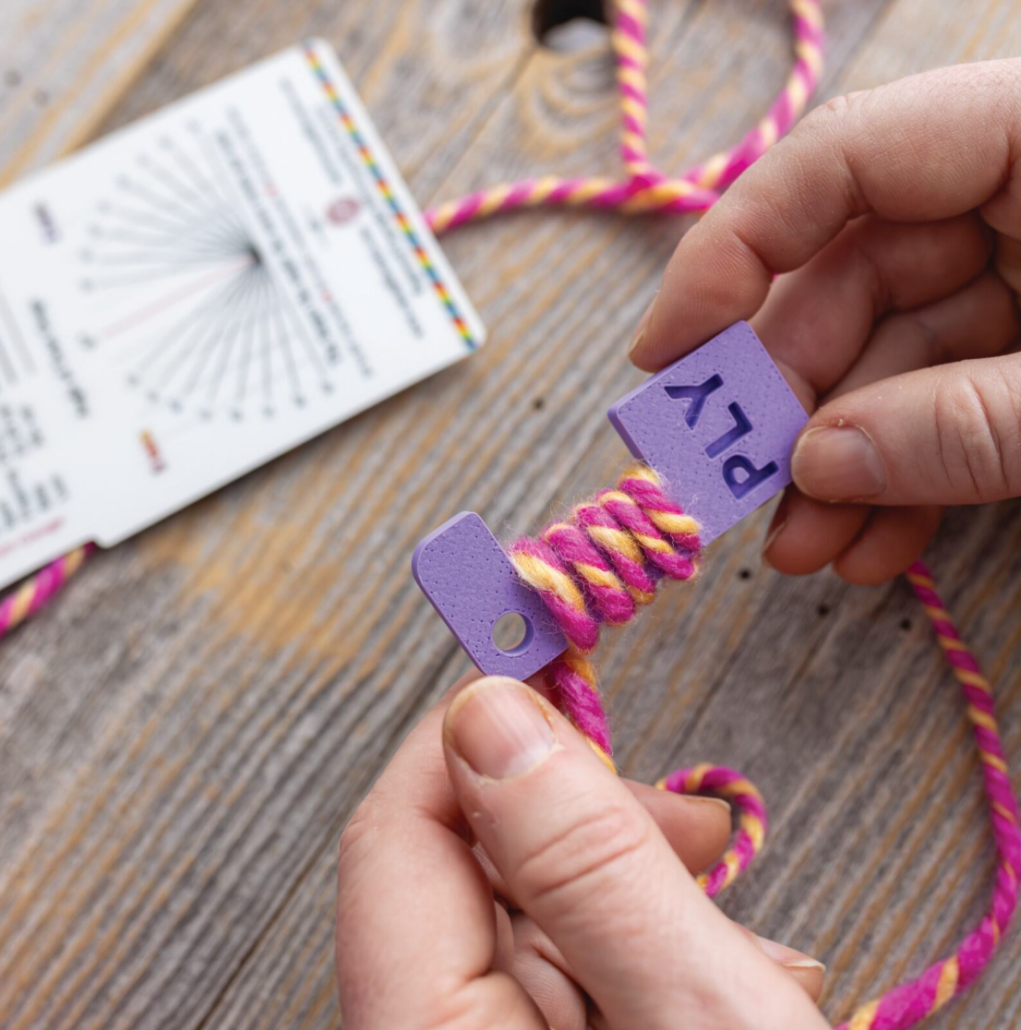
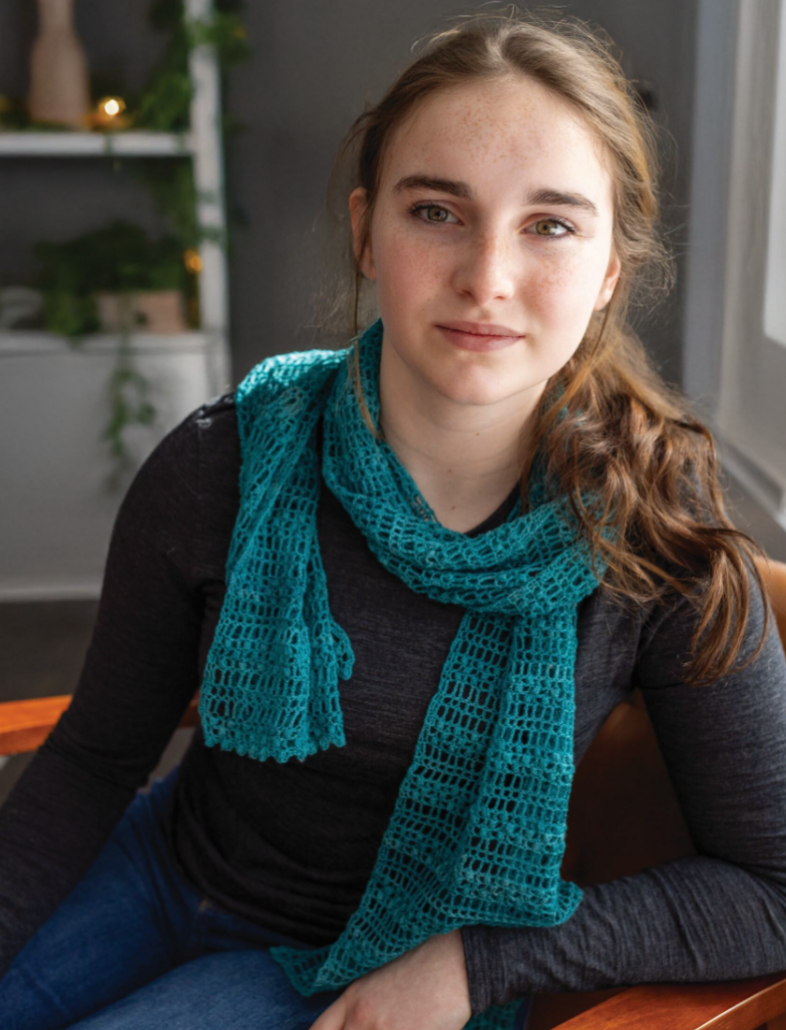
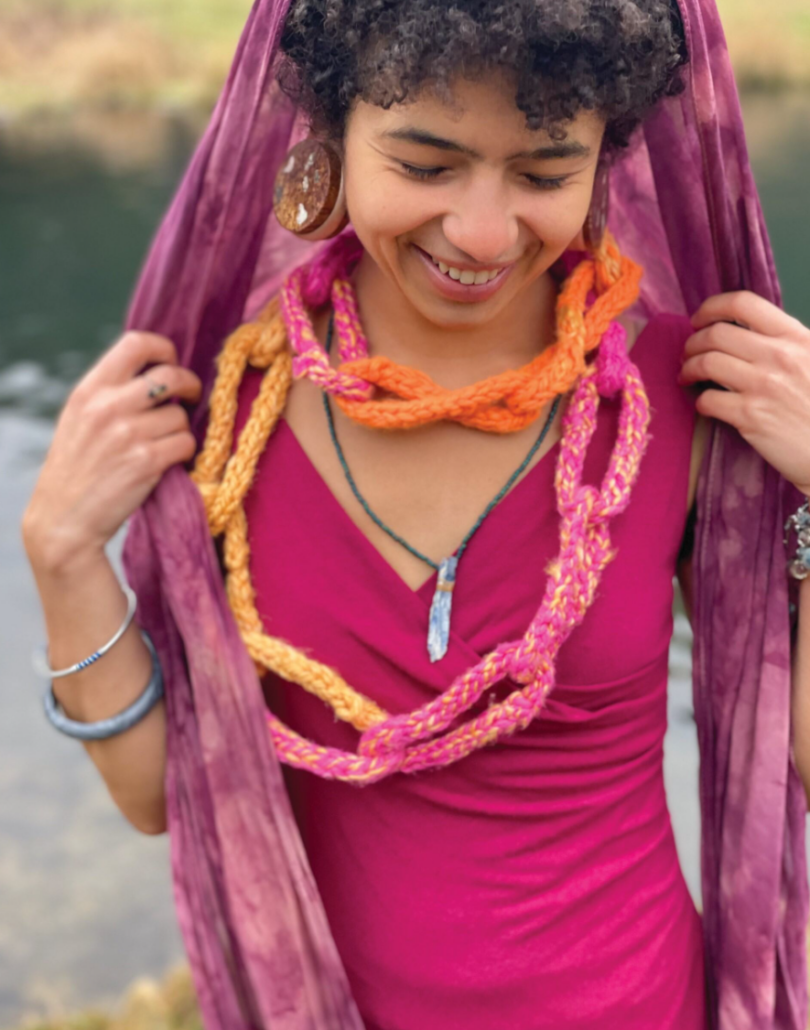
Guys, there is all this and so, so much more and so many AMAZING writers! If you haven’t already gotten your copy, you can order it here.
Leave a Reply
Want to join the discussion?Feel free to contribute!