Mixing Things up for a Sweater
words and photos by: Johanna Carter
I always admire those who are able to spin mountains of yarn for a big project, ready to knit a wonderful sweater or cardigan. It is a satisfying feeling when you finish all that work, especially if you started with washing and combing the wool or even raising your own sheep.
Mixing spinning and knitting
The typical way to work through a larger project is to spin all the singles first and ply them in a particular order so you get the yarn even throughout the whole project. I don’t have so many bobbins, but my bigger problem is that I am quite impatient and want to get on with knitting once I have an idea. And normally, my brain is full of ideas for fibre work and the limit is the time, as I am a musician and teacher. I can’t sit at the spinning wheel for a long time if I’m not on holiday, so during the school year I mostly knit, and during the holidays I can dye, spin, use my drum carder, and do lots of fibre work. The only time I was able to produce bigger quantities of yarn before I knitted them up was during the Tour de Fleece in the two years during the pandemic, when we did not go on holiday at the beginning of July.
I like to finish knitting one big project like a sweater or cardigan before I start the next one, or at least until I can’t carry it in my bag easily anymore, so I have an excuse to begin the next one. Sometimes it is good to have a second project on the go – I call it mindless knitting, where I don’t have to look very much – which I can keep my hands busy during Zoom or other meetings, which helps me listen.
Mixing colours and fibres
Usually I dye my yarn with plants which I collect in the woods or get from garden flowers. I also use cochineal and indigo, which I buy, to get lots of different colours. I really love the greens and blues I get from dyeing with indigo. I have lots of dyed wool, and all those colours give me inspiration for further projects.
Blending the wool on the drum carder I can get even more shades. I like to blend with fibres like silk, alpaca, or plant fibres, and I love sari silk, to get those little bits of colour in my yarn.
When I have an idea for the next sweater, I start carding, and then I can begin to spin. Once I have spun enough yarn – say, for one day – I cast on and start knitting, usually top down, so I don’t have to decide too much in advance about length and width.
When I spin on my wheel, I have to sit at home, but while spinning I can read a book or talk to others during online meetings. I also like to spin on my spindles, and that works on a walk, or a museum visit. I take them on holiday as they don’t need much space, and when I spin for a lace shawl, I don’t even need much wool either. At home there are spindles all over the place; I can spin when I am waiting for the kettle to boil, when the computer is slow, when I am cooking. Like that I can make good use of a short time and the yarn still grows.
I can take my knitting almost everywhere, which is why I don’t want to wait to get started until I have spun all the yarn for a whole sweater. I knit at home, on the bus or train. The only thing I have to make sure of is to be one step ahead with the yarn.
I love to knit Fair Isle sweaters. My favourite method is to use only one bobbin, which I don’t even fill, because I need smaller quantities of lots of colours. Then I wind a ply ball and ply it on itself. For that I put my thumb through the ball, so I can tension the two singles with my fingers and they don’t get tangled, as long as my thumb (or a cardboard roll or a pencil) stays in the middle. I don’t have any leftovers from plying, and it is quick when I suddenly need more yarn.
I have never had problems with the yarn not being consistent enough throughout a project. I just know what yarn I want and my fingers seem to remember what to do. I am sure it is good advice to have a little card tied to the spinning wheel with a bit of the singles you are aiming for, so you can check and make sure you are spinning a consistent yarn.
Mixing breeds
There are so many different breeds, but some of my favourites are Shetland, BFL, and Jämtland – a Swedish breed. After dyeing them, I often forget what I have used, so when I do a new project it often turns out that I have used different breeds and fibres just to get the right colour. For the Fair Isle knitting I want to juggle lots of colours, which is more important to me than making a sweater out of only one breed.
Recently I made a pullover for my husband using about 12 different breeds and colours, even mixing short and long draw. For me it was a breed experiment and a way to use up lots of smaller quantities of wool I had in my stash. For that sweater I used combed top without blending.
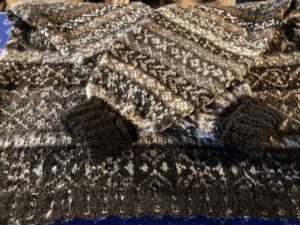
Mixing in knitting during the spinning process is a wonderful way for a spinner to avoid being overwhelmed during a sweater project.
My feeling is that some people don’t dare to start spinning for a bigger project because they get overwhelmed by the quantity they have to spin and then all the knitting there is to do, especially when you want to spin the yarn entirely on spindles. Mixing the spinning and knitting for the same project is more interesting; you get more variety and more freedom to choose what you want to do next as long as you don’t run out of yarn. It breaks the project down into smaller, less daunting parts. The only thing you might want to plan is to have enough fibre at the start, but even that is not necessary, there is always a sheep growing more wool.
Spin Together is coming in October
Spin Together is a week-long spinning competition taking place online and everywhere the week of October 2, 2021. A small group of indie dyers and fiber artists got together in 2019 to create a joy-filled spinning competition with a focus on creative spinning as well as yardage. The goal was to bring spinners from all around the world together for a team-based week of fun and camaraderie and an opportunity to spend a little more time spinning.
Now in its third year, Spin Together has yardage contests for spinners using spindles, spinning wheels, and e-spinners. There are also creative contests for Most Beautiful Skein and Wildest Art Yarn. Most of the teams are led by local yarn stores, guilds, and online yarn and fiber shops. New teams are being formed through August 30th, and then individual spinners can join teams throughout September. You can learn more and sign up on the website at www.spintogether.org.
There’s also a warm and friendly Facebook group at www.facebook.com/spintogether that is active all year long with new and experienced spinners helping each other out and sharing what they make.
Did you know we also have a monthly PLY newsletter? Sign up here!
PLY Magazine believes that Black lives matter, as well as LBGTQI+ lives. Those most vulnerable and persecuted in our communities deserve our love and support. Please be good to each other.
Handspinning Touchscreen Gloves
words and photos by Christie Schulze
Alberta winters can be brutally cold, which makes having a good pair of mittens or gloves an absolute necessity. After trying several pairs of gloves claiming to be compatible with touchscreens that either did not work as advertised or were nowhere near warm enough (seriously, how am I supposed to scroll through Insta while waiting for the bus without losing a thumb to frostbite?), I decided that if I wanted touchscreen gloves, I would have to make my own.
I researched my fiber options. I found some conductive thread and purchased it with the intention of holding it double with my yarn when knitting the end of the fingers, but when it arrived it was much thicker than I realized – nearly the same size as my fingering weight yarn – and a light beige colour that was going to contrast significantly against my darker yarn. Thankfully, one of the great advantages to being a handspinner is being able to make exactly the yarn you need.
I took a closer look at the conductive thread to see how it was made. It appeared to be a metallic strand plied with cotton. I had stumbled across a listing for spinnable stainless steel fibre on Etsy some years back and bought it as a novelty. Knowing it was conductive, I started my experiments there.
A previous bad experience told me that I didn’t want to just spin the stainless steel by itself and ply it with my wool. I had previously worked with a commercial yarn made of two plies of wool and one of stainless steel. The yarn was lovely and looked amazing, but as I worked with it, the strand of stainless steel seemed like it was cutting through the wool. I had to splice that yarn with great frequency – and what was meant to be a gift for my mother-in-law to wear to my wedding ended up being finished closer to our third anniversary. I decided to try blending the stainless steel into wool.
As so often happens with my fibre arts experiments, I experimented on my partner first by making him a pair of gloves. In my defense, he had asked for a pair of gloves in orange and grey, which seemed perfect colour-wise for blending in some stainless steel. Plus, the fibre I had set aside for my own gloves was a limited edition colourway from a dyer no longer dyeing – I wasn’t about to experiment with that!
I blended the stainless steel into the grey shade of wool for the gloves. I had no idea what ratio I should start with for my blend, so I decided on an 80/20 wool/stainless steel blend, thinking anything higher than that for the stainless steel might noticeably impact the warmth. I weighed my fibres and blended the stainless steel with the wool using hand cards. I rolled my fibre so as to keep the fibres as parallel as possible to maintain consistency with the rest of the commercially prepared top. My first experiment was a success: I had a yarn that could be used with a touchscreen!
I blended enough to use for the forefinger and thumb of each glove. Next came the true experiment. I knew the grey stainless steel blend would work with a touchscreen on its own, but I wasn’t sure if it would work when combined with the orange in the colourwork pattern. I made a small swatch and … success again! When knit together in the pattern, the yarn maintained its touchscreen properties, and my partner was able to swipe through his phone in comfortable warmth.
It’s been about a year since I made those gloves, and they have held up to the Alberta winters. I also made a hat to match! As for my own gloves, they’re still in the queue. I’ll get to them right after I finish this shawl…
Fibre used:
Grey – 50/50 Merino/Corriedale commercial top from Hilltop Cloud in the Storm colourway, blended with 20% stainless steel fibre (purchased from Divinity Fibers)
Orange – 100% Corriedale commercial top from Ashford (purchased from Stash Lounge) in Orange, Pumpkin Pie, and Nutmeg colourways, blended on a hackle.
Pattern: Deep in the Forest Mittens by Tuulia Salmela, adapted to gloves by me.
Christie Schulze is a handspinner living in the foothills of the Canadian Rockies. She holds a Master Handspinner Certificate from Olds College. Wool is her fibre of choice, but she’s always open to a good experiment. She can be found around the internet as madebyxie and documents her fibre adventures at madebyxie.ca.
Did you know we also have a monthly PLY newsletter? Sign up here!
PLY Magazine believes that Black lives matter, as well as LBGTQI+ lives. Those most vulnerable and persecuted in our communities deserve our love and support. Please be good to each other.
Send us your announcements!
Do you have or know about a new product, event, fiber, or tool you think the spinning community should know about? Tell us all about it here and we’ll share it on the blog or in the newsletter.
Did you know we also have a monthly PLY newsletter? Sign up here!
PLY Magazine believes that Black lives matter, as well as LBGTQI+ lives. Those most vulnerable and persecuted in our communities deserve our love and support. Please be good to each other.
Leave a Reply
Want to join the discussion?Feel free to contribute!