Mixing Things up for a Sweater
words and photos by: Johanna Carter
I always admire those who are able to spin mountains of yarn for a big project, ready to knit a wonderful sweater or cardigan. It is a satisfying feeling when you finish all that work, especially if you started with washing and combing the wool or even raising your own sheep.
Mixing spinning and knitting
The typical way to work through a larger project is to spin all the singles first and ply them in a particular order so you get the yarn even throughout the whole project. I don’t have so many bobbins, but my bigger problem is that I am quite impatient and want to get on with knitting once I have an idea. And normally, my brain is full of ideas for fibre work and the limit is the time, as I am a musician and teacher. I can’t sit at the spinning wheel for a long time if I’m not on holiday, so during the school year I mostly knit, and during the holidays I can dye, spin, use my drum carder, and do lots of fibre work. The only time I was able to produce bigger quantities of yarn before I knitted them up was during the Tour de Fleece in the two years during the pandemic, when we did not go on holiday at the beginning of July.
I like to finish knitting one big project like a sweater or cardigan before I start the next one, or at least until I can’t carry it in my bag easily anymore, so I have an excuse to begin the next one. Sometimes it is good to have a second project on the go – I call it mindless knitting, where I don’t have to look very much – which I can keep my hands busy during Zoom or other meetings, which helps me listen.
Mixing colours and fibres
Usually I dye my yarn with plants which I collect in the woods or get from garden flowers. I also use cochineal and indigo, which I buy, to get lots of different colours. I really love the greens and blues I get from dyeing with indigo. I have lots of dyed wool, and all those colours give me inspiration for further projects.
Blending the wool on the drum carder I can get even more shades. I like to blend with fibres like silk, alpaca, or plant fibres, and I love sari silk, to get those little bits of colour in my yarn.
When I have an idea for the next sweater, I start carding, and then I can begin to spin. Once I have spun enough yarn – say, for one day – I cast on and start knitting, usually top down, so I don’t have to decide too much in advance about length and width.
When I spin on my wheel, I have to sit at home, but while spinning I can read a book or talk to others during online meetings. I also like to spin on my spindles, and that works on a walk, or a museum visit. I take them on holiday as they don’t need much space, and when I spin for a lace shawl, I don’t even need much wool either. At home there are spindles all over the place; I can spin when I am waiting for the kettle to boil, when the computer is slow, when I am cooking. Like that I can make good use of a short time and the yarn still grows.
I can take my knitting almost everywhere, which is why I don’t want to wait to get started until I have spun all the yarn for a whole sweater. I knit at home, on the bus or train. The only thing I have to make sure of is to be one step ahead with the yarn.
I love to knit Fair Isle sweaters. My favourite method is to use only one bobbin, which I don’t even fill, because I need smaller quantities of lots of colours. Then I wind a ply ball and ply it on itself. For that I put my thumb through the ball, so I can tension the two singles with my fingers and they don’t get tangled, as long as my thumb (or a cardboard roll or a pencil) stays in the middle. I don’t have any leftovers from plying, and it is quick when I suddenly need more yarn.
I have never had problems with the yarn not being consistent enough throughout a project. I just know what yarn I want and my fingers seem to remember what to do. I am sure it is good advice to have a little card tied to the spinning wheel with a bit of the singles you are aiming for, so you can check and make sure you are spinning a consistent yarn.
Mixing breeds
There are so many different breeds, but some of my favourites are Shetland, BFL, and Jämtland – a Swedish breed. After dyeing them, I often forget what I have used, so when I do a new project it often turns out that I have used different breeds and fibres just to get the right colour. For the Fair Isle knitting I want to juggle lots of colours, which is more important to me than making a sweater out of only one breed.
Recently I made a pullover for my husband using about 12 different breeds and colours, even mixing short and long draw. For me it was a breed experiment and a way to use up lots of smaller quantities of wool I had in my stash. For that sweater I used combed top without blending.
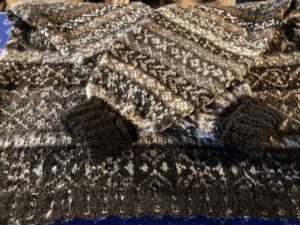
Mixing in knitting during the spinning process is a wonderful way for a spinner to avoid being overwhelmed during a sweater project.
My feeling is that some people don’t dare to start spinning for a bigger project because they get overwhelmed by the quantity they have to spin and then all the knitting there is to do, especially when you want to spin the yarn entirely on spindles. Mixing the spinning and knitting for the same project is more interesting; you get more variety and more freedom to choose what you want to do next as long as you don’t run out of yarn. It breaks the project down into smaller, less daunting parts. The only thing you might want to plan is to have enough fibre at the start, but even that is not necessary, there is always a sheep growing more wool.
Send Us Your Tips
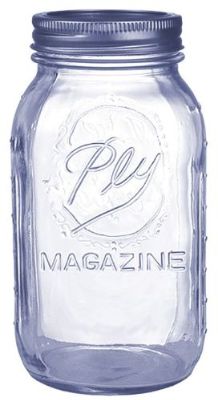
We often spin yarns to cover the heads and hands of kinds, what is the best handspun for these high-wear but low-care projects? Blends, structures, fibers?
Share your tip by going to our Tip Jar submission page.
We share tips in every issue of PLY; these tips will for the Head and Hands Winter 2021 issue.
The person who submits our favorite tip will get a prize from us! It’s our way of saying thanks for sharing your wisdom with the PLY readers.
Did you know we also have a monthly PLY newsletter? Sign up here!
PLY Magazine believes that Black lives matter, as well as LBGTQI+ lives. Those most vulnerable and persecuted in our communities deserve our love and support. Please be good to each other.
3D-Printing Spinning Tools
words and photos by Sissel Brun Ellevseth
When the Coronavirus cancelled our plans for summer vacation, I decided to invest the airfare refund in a 3D printer. The initial thought was to print fun stuff for the kids, useful things for the house, and bobbins for my EEW Nano and other tools for spinning and weaving. The printer is useful for all sorts of projects. Where I earlier had to make things of wood or metal, I can draw up my project on the computer and some hours later the finished thing is ready. Now, I must admit, it not always quite as easy as that. There have been a lot of trials and errors, a lot of hours cursing the computer for not understanding what I want it to do for me in the design program, and the occasional spaghetti incidents.
A lot of finished designs for spinners are available on sites like Thingiverse, ranging from simple drop spindles to entire plans for electric spinners. On Thingiverse, all files are free to use, and some you can even print for sale. Just be sure the designer has released the design with such a license. It is never fun to find your design being sold on Etsy by someone else if your intent is just to share designs for personal use.
The first 3D-printed spindles I saw in a spinning forum was Chivampi’s dealgan back in 2016. I had never even seen a spindle like that, and 3D-printing itself was quite new to me. The dealgan spindle is of Scottish origin from the 18th century and doubles as a nostepinne if you wind your yarn right. A dealgan is an easy to print, easy to use spindle (once you get your leader attached), and the spindle can be used just as is, straight from the printer. You can find a couple more dealgan designs on Thingiverse too if you should want a little more curved look. There are often many different options on a theme, and it is always encouraged to post makes and adaptions to a design; just remember to be nice and credit the designer if you use an existing design as a template.
Another fun and easy printed spindle project is Scott Snyder’s little Mayan paddle spindle. The design requires a 22mm bearing and a stick to get going, but if you have some of those fidget spinners lying around, you can easily pop out a bearing from the center of one. Since you now have a fidget spinner with no spinner action in sight, why not check out Scott’s other designs and print up a top whorl fidget spinner adaptor? Find a dowel and a hook and you will have two cool new spindle toys to play with.
Some of you might like a small distaff to help manage the wool while spindling. Verdrus uploaded a nice finger distaff a while back. I printed this design in wood-filament which is plastic containing real wood fibers. A print in wood filament can be sanded and oiled like real wood. I find this filament needs a lot of sanding and finishing while other plastic filaments are much easier to use, like the most common in use polylactide (PLA) family.
PLA comes in a wide array of colors and finishes. It prints on fairly low temperatures and can be used on the simplest of printers. PLA is a renewable thermoplastic and a polymer. It is “processed” from the starch of plants such as corn, sugar cane, and sugar beet, making it environmentally friendly and sustainable. It will not stand well for heat so it should not be used for things that will need to withstand the heat from the sun.
Now that you have made your spindles, you might need a niddy-noddy to skein your yarn? You have several designs to choose
from, like this quite easy to print, one-yard niddy-noddy from Sarahspins.
Are you going to knit with your yarn? Check out the sock blockers, stitch markers, yarn bobbins, and even several yarn ball winder designs available out there. Some even have full plans to motorize the winder. Now, not all designs available will hold water. There are incomplete files and downright awkward designs, but there are also perfect designs. You just have to go exploring. Be aware though, time flies when you’re down the rabbit hole… Other than Thingiverse, several other sites offer printing files both for free and for payment. Yeggi.com and stlfinder.com are useful search engines that will help you search multiple sites at once.
You can also find a lot of different bobbins and some other wheel accessories for various wheels to print too, like for the EEW e-spinner family. In addition to the EEW community’s designs, Maurice Ribble – the inventor of the EEW e-spinners – has made all design files for bobbins and accessories available to print and customize the spinners. He even allows people with 3D-printers to print and sell his designs. The EEW Nano has a lot of gadgets to choose from like battery boxes, various lazy kates, bobbins and yarn guides. With the new EEW 6.0 with its big bobbin capacity, I expect we are going to see some very cool bobbin designs in the future.
For the much smaller Nano, you have a lot to choose from if you want to buy finished fancy bobbins. Swedish Wool and Yarns as well as Snyder Spindles on Etsy sell fun bobbins, as do Snortimers Hub and Theresa Ehlers from their own web shops, and there are others out there offering the standard bobbins Maurice has designed.
Designing for 3D-printing can be done in various programs. I like Fusion360, which is free for personal use with limited functionality. It is quite an advanced program, and I don’t need the limited functions for my designs in any case, so the light version is good for me. One other commonly used program from the same developer is Tinkercad, a simpler program which also is free to use. Any design program will take some time to learn to use, but when you master designing on the computer there is little limit on what you can make. My husband is my best customer, often coming home with ideas of what I could make to hang this and that to the walls in his home brewery. I have also repaired toys for the kids by replacing a water tank in a loved fire truck, rebuilding the trailer hitch on a small car model, and making tons of Among Us miniatures for the tween.
I find the 3D-printer especially useful for making band weaving heddles in all sizes imaginable, and I have made loads of the different Turkish spindles on Thingiverse to gift my friends who are interested in spindling.
3D-printing as a hobby is both fun and challenging. A lot of resources are available online to master both designing and how to perfect your prints, and a lot of forums are available online to get answers to problems. There are a lot of different printers available in all price ranges, so if you are in the market for a printer, be sure to use your time to choose the right one. If you don’t want to invest in a printer yourself, some libraries have printers and will let you use them, sometimes for a fee. Also, if you have a Makerspace community in your area, go check them out! Makerspaces usually have printers and all the other cool toys and tools, and Makerspace people are usually super cool people.
Did you know we also have a monthly PLY newsletter? Sign up here!
PLY Magazine believes that Black lives matter, as well as LBGTQI+ lives. Those most vulnerable and persecuted in our communities deserve our love and support. Please be good to each other.
Spinners During Lockdown
Thanks so much, everyone, for sharing your experiences of spinning during lockdown. We’ve shared responses throughout the past few months in the newsletter and blog. Here’s the final collection of responses.
“I have been spinning on my wheel to calm my mind if it was too frazzled to knit. I have also ordered fibre online from producers I hadn’t tried before, such as the fabulous Countess Ablaze. It’s a pity many producers haven’t been able to restock their shops or send out to customers easily, but I had a good time spinning what I could get, and planning the projects to make with the finished yarns.” ~Mickey T., UK “For Christmas received an e-spinner so learning to spin on a wheel since I have been using spindles. Love listening to audio books while I spin. Very relaxing while I spin fiber samples, learning as I go.” ~Marilou, Murrysville, PA
“Around the start of the pandemic, I had been in a spinning slump for a while. But once I was working from home, it was much easier to get a little spinning done here and there, not to mention the time gained from not commuting. My mojo came back, and over the summer I found myself (finally!) finishing processing my first fleece, a Jacob that I split into three groups by color, combed and spun. In the fall I made a great big comfy shawl out of that yarn that’s the perfect thing to wrap up in on chilly mornings.” ~Daisy F. W., Columbus, OH
“On my electric wheel.” ~Jessica P., Clifton, TN
“Sitting in my recliner with my 3 mini dachshunds. I use my Hansen pro and have been working on an order of lace weight 100 percent vicuna. Mostly I’ve been spinning exotics the last few months to restock my online stores. The luxury yarns such as qiviut, mink, and cashmere seem to sell out pretty quickly. Next up is to tackle the mountain of French Angora fiber from my bunnies, then back to exotics.” ~Gayle P., Coos Bay, Oregon
“Yak/silk dyed by Greenwood Fiberworks on support spindles and BFL gradients on my wheel from The 100th Sheep.” ~Katrina K., Colorado
“I mostly used a drop spindle and spun infrequently. Once the pandemic measures were in place, I didn’t have the bandwidth to work on my usual lace projects. Spinning was a simpler more soothing , stress relieving activity. I took up support spindling for even more ease on the body. I’ve really embraced the spinster life. My collection of spindles has gotten a little out of control and I’ve been experimenting with lots of different fibers. Spinning has definitely (for now) overtaken knitting as my #1 hobby.” ~Marilyn E., Dallas, TX
“A friend who lives near a bison farm sent me a big bag of fiber. She’s not a spinner, and she said ‘it’s not much, sorry’ but it’s an overstuffed 2-gallon ziploc bag! It’s now all been washed and I’ve been chipping away at it as I binge-watch TV. Some of it is too short for me to manage and some of it is coarse, so it’s like hunting for treasure in this big bag, but I’m finding lovely, soft fiber about 1-1.5″” long and cleaning out the grit with a dog flea comb because my carders made a mess of it. If nothing else this pandemic has taught me patience and given me the time for projects like this. I am spinning it on a fairly light spindle and the spinning goes beautifully, it’s the prep that’s taking forever, but it’s destined to be the weft for a scarf that will go to the friend who send me the fiber.” ~Anne S., Los Angeles, CA
“More than usual. Over 5,5 kg 2 ply yarn and total in singles over 29000 meters. Part of it from my own sheep’s wool.” ~Sanne H., Sweden
“I was lucky enough to be able to take a full-day breed study class with Devin Helmen last winter in which I learned about the Shave ’Em to Save ’Em program. So I embarked upon that last summer and have been using it as DIY professional development – I’m shooting for completing 15 breeds by Labor Day 2021 (just finished #5 this morning).” ~Lindsey S., Stanwood, WA
“Non stop . Actually when I’m not working!” ~Susan B., Port Sydney, Ontario
“I started spinning around 3 years ago, but hadn’t touched my wheel in 18 months, my hands were constantly sore especially my fingers, and it was almost impossible to draft and or spin, then I moved from a hardwater area to Lincolnshire lockdown 3 arrived and although my hands were constantly being washed they started to heal, I seemed to be reading about other peoples spinning tales, questions and seeing beautiful yarns being created, inspiration all around so I dug the wheel out of its cupboard (Ashford Joy 2) and tried spinning some Jacobs to see if I could still do it. In my stash I have merino, Jacobs silk, Polwarth, amazing how much you can acquire I am now on Merino/silk the days fly by as my wheel spins away, I am by no means perfect, but getting more consistent, but most of all I am enjoying myself, its very therapeutic, and the days fly by looking forward to when I can sit in the garden and spin, for now I am in the living room, trying not to take over the whole room! How am I spinning in one word, happily.” ~Sandra M., Lincolnshire
“Going back to basics – drop spindle-and learning new spinning methods – takli and supported spindle.” ~Christi, Nebraska
“Before the pandemic I had a monthly spinning meetup at a yarn shop in Ontario, once the pandemic hit we could not longer meet in person so now each week on Sunday at 11:00am we meet virtual and spin together. It is a fun way to relieve stress and chat with other spinners while working on projects and having a show and tell session. Conversation is often lively and humorous but also supportive and caring as each of us have had our own struggles with the pandemic. Some of the spinning group requested that we start a breed study to help pass the time and continue learning about spinning and sheep fibre. Each month I distribute a fleece to all and we wash, process, discuss and spin our portion of the fleece. Each of these events give us something to look forward to and keeps our group open and sharing information about sheep and spinning and fibre. It is a wonderful supportive group that allows us laughter and relief. We are thankful for each other as it helps keeps us grounded and sharing about our spinning adventures.” ~Jane S., Ontario, Canada
“Our guild, Treadles to Threads has had a drop-in casual spinning group on Monday afternoons at various member’s homes. When we were locked down we went to Zoom. There are usually 10-15 people who meet up including some who have moved away. We share what we are working on, get help from each other on spinning and knitting, etc. Our guild is working on a Jacob Sheep project using the yarn to knit one of two sheep related hats. Jacob Sheep have white, brown, black and gray wool. We have a member who has a flock of these sheep. Deb Robson gave a presentation to our guild (via Zoom) this year and we decided to use the Jacob Sheep wool as part of primitive breeds. We have been busy and in touch with each other and our fiber crafts!” ~Joan A. Walnut Creek
“If anything the pandemic changed my daily routine from having time to pick what I wanted to do to having to be more creative with my time. I became the full time caregiver to my two grandsons, which included virtual school. I’m working on my level II Master spinner certification from Olds College so I’m spinning lots of camelids and fine wools. We also acquired our first flock of Finn sheep (in the fall of 2020) on our small homestead. I’m fitting spinning in where ever I can (during zoom school for the boys), in between animal chores and now gardening. I’ve also enjoyed more zoom spin ins with friends from school and joined other spin groups with zoom! I do enjoy that I have these outlets to see others and spin at the same time!” ~Wendy C., Rochester, WA
“Constantly, but finally used some of my stash and actually knitted 2 sweaters!!” ~Susan S., Marshall, NC
“I’ve spun my remaining North Ronaldsay roving … a joy for the senses.” ~Sharon G., Kentucky
Did you know we also have a monthly PLY newsletter? Sign up here!
PLY Magazine believes that Black lives matter, as well as LBGTQI+ lives. Those most vulnerable and persecuted in our communities deserve our love and support. Please be good to each other.
Leave a Reply
Want to join the discussion?Feel free to contribute!