Mixing Things up for a Sweater
words and photos by: Johanna Carter
I always admire those who are able to spin mountains of yarn for a big project, ready to knit a wonderful sweater or cardigan. It is a satisfying feeling when you finish all that work, especially if you started with washing and combing the wool or even raising your own sheep.
Mixing spinning and knitting
The typical way to work through a larger project is to spin all the singles first and ply them in a particular order so you get the yarn even throughout the whole project. I don’t have so many bobbins, but my bigger problem is that I am quite impatient and want to get on with knitting once I have an idea. And normally, my brain is full of ideas for fibre work and the limit is the time, as I am a musician and teacher. I can’t sit at the spinning wheel for a long time if I’m not on holiday, so during the school year I mostly knit, and during the holidays I can dye, spin, use my drum carder, and do lots of fibre work. The only time I was able to produce bigger quantities of yarn before I knitted them up was during the Tour de Fleece in the two years during the pandemic, when we did not go on holiday at the beginning of July.
I like to finish knitting one big project like a sweater or cardigan before I start the next one, or at least until I can’t carry it in my bag easily anymore, so I have an excuse to begin the next one. Sometimes it is good to have a second project on the go – I call it mindless knitting, where I don’t have to look very much – which I can keep my hands busy during Zoom or other meetings, which helps me listen.
Mixing colours and fibres
Usually I dye my yarn with plants which I collect in the woods or get from garden flowers. I also use cochineal and indigo, which I buy, to get lots of different colours. I really love the greens and blues I get from dyeing with indigo. I have lots of dyed wool, and all those colours give me inspiration for further projects.
Blending the wool on the drum carder I can get even more shades. I like to blend with fibres like silk, alpaca, or plant fibres, and I love sari silk, to get those little bits of colour in my yarn.
When I have an idea for the next sweater, I start carding, and then I can begin to spin. Once I have spun enough yarn – say, for one day – I cast on and start knitting, usually top down, so I don’t have to decide too much in advance about length and width.
When I spin on my wheel, I have to sit at home, but while spinning I can read a book or talk to others during online meetings. I also like to spin on my spindles, and that works on a walk, or a museum visit. I take them on holiday as they don’t need much space, and when I spin for a lace shawl, I don’t even need much wool either. At home there are spindles all over the place; I can spin when I am waiting for the kettle to boil, when the computer is slow, when I am cooking. Like that I can make good use of a short time and the yarn still grows.
I can take my knitting almost everywhere, which is why I don’t want to wait to get started until I have spun all the yarn for a whole sweater. I knit at home, on the bus or train. The only thing I have to make sure of is to be one step ahead with the yarn.
I love to knit Fair Isle sweaters. My favourite method is to use only one bobbin, which I don’t even fill, because I need smaller quantities of lots of colours. Then I wind a ply ball and ply it on itself. For that I put my thumb through the ball, so I can tension the two singles with my fingers and they don’t get tangled, as long as my thumb (or a cardboard roll or a pencil) stays in the middle. I don’t have any leftovers from plying, and it is quick when I suddenly need more yarn.
I have never had problems with the yarn not being consistent enough throughout a project. I just know what yarn I want and my fingers seem to remember what to do. I am sure it is good advice to have a little card tied to the spinning wheel with a bit of the singles you are aiming for, so you can check and make sure you are spinning a consistent yarn.
Mixing breeds
There are so many different breeds, but some of my favourites are Shetland, BFL, and Jämtland – a Swedish breed. After dyeing them, I often forget what I have used, so when I do a new project it often turns out that I have used different breeds and fibres just to get the right colour. For the Fair Isle knitting I want to juggle lots of colours, which is more important to me than making a sweater out of only one breed.
Recently I made a pullover for my husband using about 12 different breeds and colours, even mixing short and long draw. For me it was a breed experiment and a way to use up lots of smaller quantities of wool I had in my stash. For that sweater I used combed top without blending.
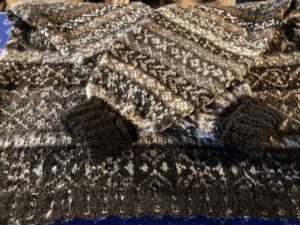
Mixing in knitting during the spinning process is a wonderful way for a spinner to avoid being overwhelmed during a sweater project.
My feeling is that some people don’t dare to start spinning for a bigger project because they get overwhelmed by the quantity they have to spin and then all the knitting there is to do, especially when you want to spin the yarn entirely on spindles. Mixing the spinning and knitting for the same project is more interesting; you get more variety and more freedom to choose what you want to do next as long as you don’t run out of yarn. It breaks the project down into smaller, less daunting parts. The only thing you might want to plan is to have enough fibre at the start, but even that is not necessary, there is always a sheep growing more wool.
Tweaking My E-Spinner for Angora
words and photos by Terry Clemo
“I’m not new at this spinning thing,” I think to myself. “Why am I having such a strange beginner experience with my new Ashford E-3 electric spinner?” After setting up my new machine, I start to play with some dyed wool. I didn’t think changing from a manual, foot-driven spinning wheel to a little electric spinner would be such a challenge. But it has been, and not for the reasons one might think. I’m not missing the treadling; in fact, I’m so happy to be able to put my legs up. I’m so much more comfortable now – hey, I can spin in bed!
“So what’s your problem,” you might ask. Well, I’m having trouble getting my spun yarn to wind on, and when I stop, the bobbin keeps turning and the single wraps around the bobbin and is going the wrong way. Ugh, now to unwind and correct the path of my spun single. I’ve not ever had the bobbin on my double treadle Lendrum do that before. “Hmmm, Lendrum bobbins are so little looking compared to the jumbo bobbins that came with the new E-3.” I’m not used to their weight turning around with the flyer either. So I slightly tighten up the Scotch tension to make a bit more resistance on the bobbin and try again. Same thing happens, so I add a tiny bit more tension, and the draw in of the single is starting to work, but just barely. Okay, now maybe I can get somewhere.
At the same time I’m playing with the speed controller of the flyer to see how it reacts with my takeup. It’s adding another variable to my dilemma. In comparison, both spinners are flyer-led and have Scotch tension, but why are they behaving so differently? Time for a cocktail. The DT Lendrum has the drive band on the flyer, and when I press the treadle I get the immediate response of the flyer turning. The E-3 has the centre spindle of the flyer resting in a keyed bushing that is the centre hub of the motor, so I have to turn up the speed dial to get it turning. As I’m playing with the speed control, I find it needs to be turned up almost to 15–20% to get the flyer to move when I have some resistance on the single and so that there is some torque force to be able to pull the single so it wants to wind on.
By now I’m using more flyer speed and more tension, and the bobbin stops after spinning. But now there’s too much pull for my liking and I can’t get the amount of twist into my single that I need before it wants to be swallowed by the orifice. Normally, I would back off the tension, but I can’t really; there doesn’t seem to be a sweet spot. I can’t fine tune this setup with the original heavy, stiff fishing line that came with the machine. And I’m not spinning with a grabby fibre or a short draw, which might help get this spinner working well.
Side journey through angora spinning
You see, my spinning journey flourished at the same time my love of very fuzzy rabbits was fulfilled. My first angora was an English that I named Flurry. She was “fur in a hurry”! Needless to say, pretty much all of my spinning has something to do with angora from rabbits.
My favorite thing is to spin angora from a cloud (which is basically a fluffed up, or carded, small handful of airy angora fibre, which can be organized or not); it can be so magical. I especially like how the tips of the individual fibres protrude and spiral out from the centre of the single when they are drawn out and not smoothed down. It’s exactly what blooming spun angora should look like. This texture is accentuated by the long draw.
Angora is a finicky fibre; the more you fuss with it – try to handcard it or blend it with itself or other fibres – the more likely you are to put more nepps in it than it had from off the rabbit. Since angora is so fine (in the range from 7–8 microns to mid-teens, with an average of 10–12 microns), it easily tangles. Also, the average staple length is 4–7 inches for the blanket of the rabbit, the longest fur from their back, and unless its harvested correctly, it can get new tangles in it. Angora bunnies also have some lovely textured fur on their chest, belly, and legs; it’s shorter at 2–3 inches or so and it’s not as dark as the top side colour, mostly. As you spin their fibre, there will be colour changes as you go because the colour varies on the bunny. This colour changing ability is quite beautiful and gives angora yarns their character.
Some angora spinners don’t mix the two basic types, mostly because of the length difference, but colour differences can be the main reason. For some of my spinning projects, having both can make the yarn more textured, and it will be fuzzier. My favourite way to spin is straight from the storage box, loose and fluffy whatever comes so I may end up with some shorter fibres mixed with longer silkier ones. So I try to fluff up and mix the two so I hold a couple of staple lengths at the base with my thumbs and fingers and I pull apart from so it separates into one layer in each hand. I lay it back on top of the other layer, hold the base end, pull it apart, and this time I put the new layer on the bottom. I’ll put many of these little bundles aside in a smooth container to spin later.
I like my angora spun with tiny slubs and uneven blending, and with a long draw technique that lends to loose airy preparations. So with my long draw technique, I need some tension to pull against to draft out the fibres as the twist is holding everything together just enough to be a thread.
Back to the e-spinner
So my secret is out, I’m a long draw girl. Now I get to play around with my new toy and translate this style of long draw to the e-spinner. I need to have very little take-up tension while I’m drafting so my single doesn’t prematurely feed onto the bobbin before it gets sufficient twist. The single when using short draft is basically always moving through the orifice, but not with a long draw. My long draw draft is about 14–16 inches, so there’s a lag in time before I can wind on. I don’t want the flyer to pull too hard and pull apart the newly forming single. I like to use a supported long draw. My right hand helps me control twist to the cloud of fiber and gives me something to pull (draft) against. I stop drafting to let my twist come into the single and I visually check for my chosen angle of twist and then slowly push the thread into the orifice, and the bobbin starts to wind the single and it seems to gather a bit of momentum till I stop. Leaving my leader out with extra twist building up in it and again having very little draw in, I start drafting out again.
So after all this is said, remember that I’m spinning Angora at 100 percent or about 20–25 percent in a blend with very fine wool (22 microns or less) and silk or maybe some alpaca or other fine fibres. Angora is very slippery, hence the very light takeup on the bobbin, and it lets me get more twist in my single. I usually spin from laceweight to fingering weight, so I’m spinning fine. My plies for my yarns are made of one or two singles of angora and the others are a blend of dyed wools, silks, and angora or dyed wool, all the while playing with colours. Depending on the project and how much angora I want, I can use different combinations of these, but I usually stick to 2 or 3 plies per yarn.
How do I fix my dilemma as to how to make this machine work the way I need it to?
Planning my attack, depending on how and what I wanted to spin, I could use cords of different materials for the brake band to give more slipperiness. I might try a finer nylon filament or the plastic coated stainless steel jewellery wire, some nylon threads, or high end fishing lines made of plies from titanium or other advanced materials. I also wanted to try adding a bit more drag to increase tension and help with spin-on of the bobbin, so I’ve tried cords that were a bit rough like hemp (thin and thick) and whatever else I could think of. I’ve even tried something similar to the traditional cotton. I tried the string that sealed the rabbit feed bags, which seemed to be more slippery than the usual cotton. It’s probably a form of polyester, which is more durable than the cotton. The diameter of a cord also comes into play. I need to be able to quickly snap different brake bands into place to find my favourite band.
I realized that if I wanted to experiment with different bands it wasn’t going to be so easy to untie knots attached to the springs. I decided to make different quick-connect brake bands. I used small lobster clasps approximately 10mm and crimps beads or tubes, 1.5mm size. I also had foldover crimp ends (with connector eye) in various sizes, which would close better with crimpers.
So far, my favourite band over the rabbit feed bag string was the plastic coated multi-filament beading wire. It’s quite fine and seems to give me varying degrees of tension that I didn’t have before. Like any journey, I’m still playing around with different cords and different fibre blends. There’s not enough time in a day or a week for that matter to ever have enough spinning time.
Terry Clemo has had soft spot for fuzzy animals from a very young age. It seemed to follow that her interests spanned to other fibre arts like knitting and sewing and other textural crafts while still a child. Her mother was an expert machine knitter and told her she needed to hand knit before she would give her any machine knitting lessons. With the lessons came a toolbox of techniques that opened up the door to designing her own knitting patterns. Working with her luscious angora, Terry makes batts, handspun yarns, and semi-precious beaded wire knitting jewellery such as shawl pins. You can find Terry on Facebook and Instagram and at various fibre events.
Did you know we also have a monthly PLY newsletter? Sign up here!
PLY Magazine believes that Black lives matter, as well as LBGTQI+ lives. Those most vulnerable and persecuted in our communities deserve our love and support. Please be good to each other.
Spin Together is coming in October
Spin Together is a week-long spinning competition taking place online and everywhere the week of October 2, 2021. A small group of indie dyers and fiber artists got together in 2019 to create a joy-filled spinning competition with a focus on creative spinning as well as yardage. The goal was to bring spinners from all around the world together for a team-based week of fun and camaraderie and an opportunity to spend a little more time spinning.
Now in its third year, Spin Together has yardage contests for spinners using spindles, spinning wheels, and e-spinners. There are also creative contests for Most Beautiful Skein and Wildest Art Yarn. Most of the teams are led by local yarn stores, guilds, and online yarn and fiber shops. New teams are being formed through August 30th, and then individual spinners can join teams throughout September. You can learn more and sign up on the website at www.spintogether.org.
There’s also a warm and friendly Facebook group at www.facebook.com/spintogether that is active all year long with new and experienced spinners helping each other out and sharing what they make.
Did you know we also have a monthly PLY newsletter? Sign up here!
PLY Magazine believes that Black lives matter, as well as LBGTQI+ lives. Those most vulnerable and persecuted in our communities deserve our love and support. Please be good to each other.
Handspinning Touchscreen Gloves
words and photos by Christie Schulze
Alberta winters can be brutally cold, which makes having a good pair of mittens or gloves an absolute necessity. After trying several pairs of gloves claiming to be compatible with touchscreens that either did not work as advertised or were nowhere near warm enough (seriously, how am I supposed to scroll through Insta while waiting for the bus without losing a thumb to frostbite?), I decided that if I wanted touchscreen gloves, I would have to make my own.
I researched my fiber options. I found some conductive thread and purchased it with the intention of holding it double with my yarn when knitting the end of the fingers, but when it arrived it was much thicker than I realized – nearly the same size as my fingering weight yarn – and a light beige colour that was going to contrast significantly against my darker yarn. Thankfully, one of the great advantages to being a handspinner is being able to make exactly the yarn you need.
I took a closer look at the conductive thread to see how it was made. It appeared to be a metallic strand plied with cotton. I had stumbled across a listing for spinnable stainless steel fibre on Etsy some years back and bought it as a novelty. Knowing it was conductive, I started my experiments there.
A previous bad experience told me that I didn’t want to just spin the stainless steel by itself and ply it with my wool. I had previously worked with a commercial yarn made of two plies of wool and one of stainless steel. The yarn was lovely and looked amazing, but as I worked with it, the strand of stainless steel seemed like it was cutting through the wool. I had to splice that yarn with great frequency – and what was meant to be a gift for my mother-in-law to wear to my wedding ended up being finished closer to our third anniversary. I decided to try blending the stainless steel into wool.
As so often happens with my fibre arts experiments, I experimented on my partner first by making him a pair of gloves. In my defense, he had asked for a pair of gloves in orange and grey, which seemed perfect colour-wise for blending in some stainless steel. Plus, the fibre I had set aside for my own gloves was a limited edition colourway from a dyer no longer dyeing – I wasn’t about to experiment with that!
I blended the stainless steel into the grey shade of wool for the gloves. I had no idea what ratio I should start with for my blend, so I decided on an 80/20 wool/stainless steel blend, thinking anything higher than that for the stainless steel might noticeably impact the warmth. I weighed my fibres and blended the stainless steel with the wool using hand cards. I rolled my fibre so as to keep the fibres as parallel as possible to maintain consistency with the rest of the commercially prepared top. My first experiment was a success: I had a yarn that could be used with a touchscreen!
I blended enough to use for the forefinger and thumb of each glove. Next came the true experiment. I knew the grey stainless steel blend would work with a touchscreen on its own, but I wasn’t sure if it would work when combined with the orange in the colourwork pattern. I made a small swatch and … success again! When knit together in the pattern, the yarn maintained its touchscreen properties, and my partner was able to swipe through his phone in comfortable warmth.
It’s been about a year since I made those gloves, and they have held up to the Alberta winters. I also made a hat to match! As for my own gloves, they’re still in the queue. I’ll get to them right after I finish this shawl…
Fibre used:
Grey – 50/50 Merino/Corriedale commercial top from Hilltop Cloud in the Storm colourway, blended with 20% stainless steel fibre (purchased from Divinity Fibers)
Orange – 100% Corriedale commercial top from Ashford (purchased from Stash Lounge) in Orange, Pumpkin Pie, and Nutmeg colourways, blended on a hackle.
Pattern: Deep in the Forest Mittens by Tuulia Salmela, adapted to gloves by me.
Christie Schulze is a handspinner living in the foothills of the Canadian Rockies. She holds a Master Handspinner Certificate from Olds College. Wool is her fibre of choice, but she’s always open to a good experiment. She can be found around the internet as madebyxie and documents her fibre adventures at madebyxie.ca.
Did you know we also have a monthly PLY newsletter? Sign up here!
PLY Magazine believes that Black lives matter, as well as LBGTQI+ lives. Those most vulnerable and persecuted in our communities deserve our love and support. Please be good to each other.
Leave a Reply
Want to join the discussion?Feel free to contribute!