Mixing Things up for a Sweater
words and photos by: Johanna Carter
I always admire those who are able to spin mountains of yarn for a big project, ready to knit a wonderful sweater or cardigan. It is a satisfying feeling when you finish all that work, especially if you started with washing and combing the wool or even raising your own sheep.
Mixing spinning and knitting
The typical way to work through a larger project is to spin all the singles first and ply them in a particular order so you get the yarn even throughout the whole project. I don’t have so many bobbins, but my bigger problem is that I am quite impatient and want to get on with knitting once I have an idea. And normally, my brain is full of ideas for fibre work and the limit is the time, as I am a musician and teacher. I can’t sit at the spinning wheel for a long time if I’m not on holiday, so during the school year I mostly knit, and during the holidays I can dye, spin, use my drum carder, and do lots of fibre work. The only time I was able to produce bigger quantities of yarn before I knitted them up was during the Tour de Fleece in the two years during the pandemic, when we did not go on holiday at the beginning of July.
I like to finish knitting one big project like a sweater or cardigan before I start the next one, or at least until I can’t carry it in my bag easily anymore, so I have an excuse to begin the next one. Sometimes it is good to have a second project on the go – I call it mindless knitting, where I don’t have to look very much – which I can keep my hands busy during Zoom or other meetings, which helps me listen.
Mixing colours and fibres
Usually I dye my yarn with plants which I collect in the woods or get from garden flowers. I also use cochineal and indigo, which I buy, to get lots of different colours. I really love the greens and blues I get from dyeing with indigo. I have lots of dyed wool, and all those colours give me inspiration for further projects.
Blending the wool on the drum carder I can get even more shades. I like to blend with fibres like silk, alpaca, or plant fibres, and I love sari silk, to get those little bits of colour in my yarn.
When I have an idea for the next sweater, I start carding, and then I can begin to spin. Once I have spun enough yarn – say, for one day – I cast on and start knitting, usually top down, so I don’t have to decide too much in advance about length and width.
When I spin on my wheel, I have to sit at home, but while spinning I can read a book or talk to others during online meetings. I also like to spin on my spindles, and that works on a walk, or a museum visit. I take them on holiday as they don’t need much space, and when I spin for a lace shawl, I don’t even need much wool either. At home there are spindles all over the place; I can spin when I am waiting for the kettle to boil, when the computer is slow, when I am cooking. Like that I can make good use of a short time and the yarn still grows.
I can take my knitting almost everywhere, which is why I don’t want to wait to get started until I have spun all the yarn for a whole sweater. I knit at home, on the bus or train. The only thing I have to make sure of is to be one step ahead with the yarn.
I love to knit Fair Isle sweaters. My favourite method is to use only one bobbin, which I don’t even fill, because I need smaller quantities of lots of colours. Then I wind a ply ball and ply it on itself. For that I put my thumb through the ball, so I can tension the two singles with my fingers and they don’t get tangled, as long as my thumb (or a cardboard roll or a pencil) stays in the middle. I don’t have any leftovers from plying, and it is quick when I suddenly need more yarn.
I have never had problems with the yarn not being consistent enough throughout a project. I just know what yarn I want and my fingers seem to remember what to do. I am sure it is good advice to have a little card tied to the spinning wheel with a bit of the singles you are aiming for, so you can check and make sure you are spinning a consistent yarn.
Mixing breeds
There are so many different breeds, but some of my favourites are Shetland, BFL, and Jämtland – a Swedish breed. After dyeing them, I often forget what I have used, so when I do a new project it often turns out that I have used different breeds and fibres just to get the right colour. For the Fair Isle knitting I want to juggle lots of colours, which is more important to me than making a sweater out of only one breed.
Recently I made a pullover for my husband using about 12 different breeds and colours, even mixing short and long draw. For me it was a breed experiment and a way to use up lots of smaller quantities of wool I had in my stash. For that sweater I used combed top without blending.
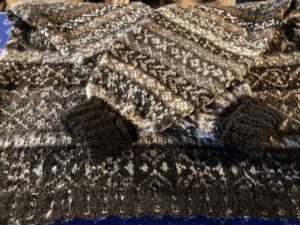
Mixing in knitting during the spinning process is a wonderful way for a spinner to avoid being overwhelmed during a sweater project.
My feeling is that some people don’t dare to start spinning for a bigger project because they get overwhelmed by the quantity they have to spin and then all the knitting there is to do, especially when you want to spin the yarn entirely on spindles. Mixing the spinning and knitting for the same project is more interesting; you get more variety and more freedom to choose what you want to do next as long as you don’t run out of yarn. It breaks the project down into smaller, less daunting parts. The only thing you might want to plan is to have enough fibre at the start, but even that is not necessary, there is always a sheep growing more wool.
Trying harder to support BIPOC
Many of you are aware of the talks happening on racism in the fiber community. If you’re not aware, please make yourself aware now. It’s important stuff, some of the most important stuff, in fact. And it does impact you, even if you think it doesn’t. Especially if you think it doesn’t. I know it’s hard to be called out. I know we’re all fragile beings that, I hope, go through life trying to do our best to be good people. And if that’s true about you, like it’s true about me, this is gonna be hard. Yes, it’s hard, but realize it’s the right thing and the company you’re in is huge. HUGE. If we all try, we can make a difference.
I know that some of you might say “but I just want to knit and be happy” or “I just came for the fiber/knitting/spinning” but that’s just not how life is. I’m sorry. I wish it could be that easy for everyone but it’s not. And until it is that easy for everyone, it can’t be that easy for anyone. Believe me, BIPOC (Black and Indigenous People/Person(s) of Color) just want to knit and be happy too, they just came for the fiber/spinning/knitting too but the color of their skin combined with a history fraught with injustice and a present rife with hate and fear, makes that an impossibility. Can you imagine? Really, can you imagine? We think we can, but the truth is, we can’t. We can’t imagine what it’s like to be different than we are, not really. We have to listen and believe when others tell us how it is for them.
It’s up to us to help make the fiber community safe and welcoming for BIPOC. Not being actively racist is not enough. You’ve got to actively be inclusive. You’ve got to actively be anti-racist. You’ve got to actively seek out BIPOC as designers, as spinners, as dyers, as companions. And I hear you again, “But why? Isn’t it more fair if I just purchase their wares when and if they appeal to me? That seems less racist, just taking race out of it.” Except that’s not actually feasible in the world we live in. It’s not. You are far less likely to see their work, their designs, their dyed fiber, their spun yarn because of our current paradigms. For now, we’ve gotta do a little work to make the world a better and safer place.
And don’t just make a change real quick because it’s being talked about in this moment. Make a change, yes, but keep doing it. We’ve gotta change ourselves, train ourselves. The world has trained us for far too long to think other and different means negative and/or invisible, we need retraining. It’s hard work and it’s ongoing work. It’s easier to settle into our comfortable lives and “just knit” or “just spin” but don’t. Work to make the world better. That’s what we’re here for, my friends. That discomfort you’re feeling about this subject, dig into that. Examine your feelings of defensiveness, your impulse to silence this conversation, your desire to have this conversation on your own terms, your need to say “you’re just here for the fiber”. LISTEN to the voices of BIPOC in our community before you brush this conversation aside.
PLY will be doing just that. The work. PLY welcomes and encourages BIPOC to write, to design, to model, but we need to do more. We don’t do enough. We made a decision on day one to actively seek and feature BIPOC models. But we are going to do more. We are going to actively seek BIPOC as writers, spinners, designers, dyers, and teachers.
I hope you’ll take this in with the love and peace with which it’s written. I’m white and I’m at fault. I try and will continue to try to be a better ally. I hope you’ll join in listening and fighting for what’s right.
jacey
The Power of Colour!
Colour and Power
Words and Graphics by Katie Weston
As handcrafters and spinners, colour is vitally important. The colour you choose to dye, spin, knit, or weave impacts your final work, your feelings about it, and others’ interpretations of it. This has long been true of colour, which has often been associated with power, as humans have used certain colours to signify position and status. Roman Emperors limited access to Murex Purple so only those in a position of power could wear that shade. In Medieval Europe, the Sumptuary Laws limited what people could wear according to their position in society. Peasants wore a dull earthy colour, whereas only nobles could wear a bright saturated colour such as scarlet.
Most modern colour rules would dictate that Elizabeth I, famously a redhead, really shouldn’t have worn a bright orange-red such as scarlet. However, the power of the colour was far more important to Elizabeth. During her time as a princess, she regularly wore scarlet, amplifying her message that she was the heir to her sister Mary I. Once she became Queen, however, she changed her message; scarlet was still a colour associated with promiscuity, and that was not the message the Virgin Queen wished to send. Instead, she dressed her ladies and retainers in scarlet to act as a symbolic backdrop to the paler colours she adopted in her own clothing.
Language of Colour
In addition to the colours themselves, the language we use to describe colour reveals a lot about the way a culture thinks about the world. Homer famously described the sea as being wine-dark. He uses the expression many times throughout his epics, The Iliad and The Odyssey, to describe the colour of the Aegean sea. This sea is very much the same blue colour as all the other bodies of water across the planet. So why doesn’t Homer describe it as being blue?
Well, for starters, the Ancient Greeks didn’t have a single word to signify blue.
Homer gives the sky the non-blue descriptive treatment as well: big, starry, or of iron or bronze. The sea is also described as whitish (polios), blue-grey (glaukos), almost black (kuaneos), and on occasion it’s even described as being purple (porphureos). So given the dominance of blue in the Greek landscape, why is there no word for blue?
Describing the June sky above the Aegean as the same colour as that Aegean sea in December during a storm does seem a little limiting. Instead, the Greeks used far more descriptive language; when the sea is described as wine-dark, it doesn’t mean the sea was the colour of red wine. Wine-dark is used in Greek literature to describe darkened blood, a cloud, a tree, and the glint of metal. It’s not actually a colour description as we would recognise today. Wine-dark doesn’t mean red; it has more to do with the lustre or superficial effect than anything related to a spectrum of shades. It’s a very different way of thinking about colour than the one we presently use.
How the Greeks perceived colour as a continuum from light to dark.
The Colour Spectrum
The Greeks created their spectrum on a different basis than ours, where light or dark were far more important than the actual hue[1] of a colour. Colours were arranged on a spectrum from white to black. Yellow was considered to be so light as to merge into white, with red and green being mid-tones and with blue being seen as a shade of black at the darkest end. This way of perceiving and describing colours is by no means unique to the Ancient Greeks, and blue is not the only colour missing from their vocabulary. Yellow is also absent, as it is in some Slavic languages, Ainu from Northern Japan, Daza from Nigeria, and the language used by the Mechopdo, in what is now California. Each uses the same word within their language to describe what Western languages call blue and yellow. The use of the same word for blue and green is even more common. The Celtic languages use the word glas to describe a shade the colour of a mountain lake; it covers every colour from a brown-ish green to blue. In Japanese, awo can mean blue, green, or even dark depending on the context.
This way of looking at colour is not something unique to the Greeks. In nearly all cultures, the linguistic distinction between light and dark happens first. After that, the word for red tends to be used, then yellow, then green, then blue. There are of course many exceptions to this, but broadly speaking, the distinction between light and dark is something most cultures develop long before any need to give specific hues a single name.
The modern colour wheel in which opposite colours are said to be complementary. However, when viewed in greyscale, some of the colours are revealed as lacking contrast, so they do not tend to stand out from one another.
Colour Value
In Western culture, our modern spectrum is a comparatively recent development. For example, a Medieval painter was unconcerned about portraying a colour accurately; the significance of the colours were far more important, especially when used to portray awe and respect. Pigments were costly, so the use of certain colours displayed the wealth of a patron. Vast expanses of ultramarine, vermillion, and gold were not important for colour accuracy – they were important for prestige and power. But those Medieval artists also understood colour theory and how to further enhance the brilliance of a particular shade. The Italian Leon Battista Alberti wrote De Pictura, a technical painting guide, in 1435 for any would-be artist. He offered this advice on the placement of colours: “If red stands between blue and green, it somehow enhances their beauty as well as its own. White lends gaiety, not only when placed between green and yellow, but almost to any colour. But dark colours acquire a certain dignity when between light colours, similarly light colours may be placed to good effect among dark.”
What’s amazing is how this nearly 600 year-old advice could actually come out of any book you might read today. When thinking about colourwork knitting, the interactions of colours in a warp and weft, or whether to ply 2 different hand-dyed colourways together, the impact of light next to dark is just as important as the hue of the chosen yarns.
Light and dark are crucial for colour combinations, and we are often advised to take a photograph and switch the colours to greyscale. To enhance one another, the colours should be different shades of grey. In a way, this idea reverts back to the Ancient Greek way of thinking about colour. Colours of a similar value[2] will blend together, even if they are quite different hues. Colours that are different in value will stand out from one another.
Colour can often leave people running scared. They’ve been told long-ago, often in childhood, that 2 shades don’t go together or that a certain colour doesn’t suit them and they should never wear it. Our modern Newtonian method of describing colours and how they relate can lead to a very narrow way of looking at the materials we work with. The modern colour wheel theory says opposite shades will contrast with one another but fails to take into account the advice given by Alberti – sometimes it’s about more than opposites; you need to add some light or dark to give real power to your colours. Equally, don’t let colours have too much power over you. Channel your inner Elizabeth I, and go ahead and dye, spin, knit, weave, and wear the colour you love.
Colours are affected by the shades that surround them. The yellow box in the centre of all these colour swatches is the same shade.
[1] Hue describes the actual colour of any given shade. So in our modern lexicon, red, green, orange, purple, etc.
[2] Value describes how light or dark a colour is.
Katie Weston lives in the hills of Snowdonia, Wales. She spends her day dyeing spinning fibre in every colour of the rainbow, so it’s perhaps a little understandable that she’s obsessed with describing it, and the history of colour. She’s the author of the book A Guide to Spinning Hand Dyed Fibre.
Leave a Reply
Want to join the discussion?Feel free to contribute!