Mixing Things up for a Sweater
words and photos by: Johanna Carter
I always admire those who are able to spin mountains of yarn for a big project, ready to knit a wonderful sweater or cardigan. It is a satisfying feeling when you finish all that work, especially if you started with washing and combing the wool or even raising your own sheep.
Mixing spinning and knitting
The typical way to work through a larger project is to spin all the singles first and ply them in a particular order so you get the yarn even throughout the whole project. I don’t have so many bobbins, but my bigger problem is that I am quite impatient and want to get on with knitting once I have an idea. And normally, my brain is full of ideas for fibre work and the limit is the time, as I am a musician and teacher. I can’t sit at the spinning wheel for a long time if I’m not on holiday, so during the school year I mostly knit, and during the holidays I can dye, spin, use my drum carder, and do lots of fibre work. The only time I was able to produce bigger quantities of yarn before I knitted them up was during the Tour de Fleece in the two years during the pandemic, when we did not go on holiday at the beginning of July.
I like to finish knitting one big project like a sweater or cardigan before I start the next one, or at least until I can’t carry it in my bag easily anymore, so I have an excuse to begin the next one. Sometimes it is good to have a second project on the go – I call it mindless knitting, where I don’t have to look very much – which I can keep my hands busy during Zoom or other meetings, which helps me listen.
Mixing colours and fibres
Usually I dye my yarn with plants which I collect in the woods or get from garden flowers. I also use cochineal and indigo, which I buy, to get lots of different colours. I really love the greens and blues I get from dyeing with indigo. I have lots of dyed wool, and all those colours give me inspiration for further projects.
Blending the wool on the drum carder I can get even more shades. I like to blend with fibres like silk, alpaca, or plant fibres, and I love sari silk, to get those little bits of colour in my yarn.
When I have an idea for the next sweater, I start carding, and then I can begin to spin. Once I have spun enough yarn – say, for one day – I cast on and start knitting, usually top down, so I don’t have to decide too much in advance about length and width.
When I spin on my wheel, I have to sit at home, but while spinning I can read a book or talk to others during online meetings. I also like to spin on my spindles, and that works on a walk, or a museum visit. I take them on holiday as they don’t need much space, and when I spin for a lace shawl, I don’t even need much wool either. At home there are spindles all over the place; I can spin when I am waiting for the kettle to boil, when the computer is slow, when I am cooking. Like that I can make good use of a short time and the yarn still grows.
I can take my knitting almost everywhere, which is why I don’t want to wait to get started until I have spun all the yarn for a whole sweater. I knit at home, on the bus or train. The only thing I have to make sure of is to be one step ahead with the yarn.
I love to knit Fair Isle sweaters. My favourite method is to use only one bobbin, which I don’t even fill, because I need smaller quantities of lots of colours. Then I wind a ply ball and ply it on itself. For that I put my thumb through the ball, so I can tension the two singles with my fingers and they don’t get tangled, as long as my thumb (or a cardboard roll or a pencil) stays in the middle. I don’t have any leftovers from plying, and it is quick when I suddenly need more yarn.
I have never had problems with the yarn not being consistent enough throughout a project. I just know what yarn I want and my fingers seem to remember what to do. I am sure it is good advice to have a little card tied to the spinning wheel with a bit of the singles you are aiming for, so you can check and make sure you are spinning a consistent yarn.
Mixing breeds
There are so many different breeds, but some of my favourites are Shetland, BFL, and Jämtland – a Swedish breed. After dyeing them, I often forget what I have used, so when I do a new project it often turns out that I have used different breeds and fibres just to get the right colour. For the Fair Isle knitting I want to juggle lots of colours, which is more important to me than making a sweater out of only one breed.
Recently I made a pullover for my husband using about 12 different breeds and colours, even mixing short and long draw. For me it was a breed experiment and a way to use up lots of smaller quantities of wool I had in my stash. For that sweater I used combed top without blending.
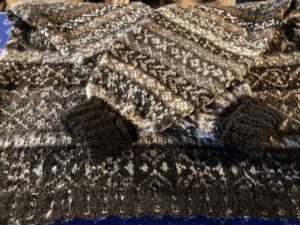
Mixing in knitting during the spinning process is a wonderful way for a spinner to avoid being overwhelmed during a sweater project.
My feeling is that some people don’t dare to start spinning for a bigger project because they get overwhelmed by the quantity they have to spin and then all the knitting there is to do, especially when you want to spin the yarn entirely on spindles. Mixing the spinning and knitting for the same project is more interesting; you get more variety and more freedom to choose what you want to do next as long as you don’t run out of yarn. It breaks the project down into smaller, less daunting parts. The only thing you might want to plan is to have enough fibre at the start, but even that is not necessary, there is always a sheep growing more wool.
Following in the steps of a 2,000 year old spinner
We’re so happy to have Christina Pappas back on the blog today, to take us on a journey back in time as she tries to walk in the footsteps of some ancient textile producers.
In my last post, I talked a little about how archaeologists use objects to learn about the distant past:
“You look at a handmade textile and you see not just a pretty object, but the hours at the loom or knitting needles, the fiber drafting at the wheel, the alchemy at the dye pot, even the shepherds with their flocks. You can see all the steps and decisions that went into creating that object, all the places where one path or another was chosen. Archaeologists are constantly trying to trace back those paths, to see those moments when a decision had to be made and why. The whys are how we learn about culture in the distant past. We can look to the past and see when and why spinning one kind of fiber over another was chosen, what changes were happening that led to that decision, and what were the ramifications of that decision….”
All the steps and decisions that go into making something are known as a production sequence. One of the ways we can learn about a production sequence from the past is to actually make the object ourselves; to try to recreate the steps that went into crafting something to understand how that process fits into everyday life.
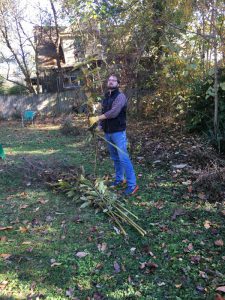
Harvesting Joe Pye Weed this past September. This was a plant used for fiber in prehistoric Kentucky. These plants are destined to become yarn for my project.
For example, let’s think about a woven wool shirt. What are all the steps to make it? Cutting the fabric and sewing the garment are steps, but we need to look all the way back to the very beginning if we are going to understand the entire production sequence. So we have to think about the sheep, processing the fleece, spinning the yarn, weaving, and then finally cutting and sewing the garment. That’s a lot!
Now, imagine the same process over 1,000 years ago in a Viking settlement. What technology was available to you? What other kinds of chores and activities were going on every day? How would the need to make a wool shirt fit into daily life? By trying to make a wool shirt exactly the way a Viking would have, we can estimate the time and effort needed and get a glimpse into the value placed on this work in their society. Similar experiments and studies into Viking sailcloth have shown how labor-intensive its manufacture was and how valued that process would have been. (This, this, and this are just a few examples of these projects.)
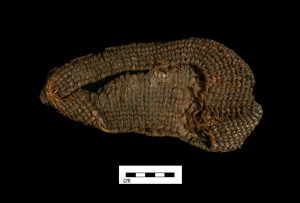
A slipper form a cave in Kentucky. This will be the slipper we will try to replicate.
At the University of Kentucky, we have a collection of prehistoric textiles from dry caves and rock shelters that are around 2,000 years old. These include fragments of shawls, bags, mats, and slippers. They are in various states of preservation but all are made from plant fibers. I know the structure of the yarns and the types of weaves used to make each object, but I’m not sure how they were made. How were the plants processed into yarn? How was the yarn spun? How easy was it to dye the yarns? How long did it take to weave a bag or make a pair of slippers? We know only a little about the process of making these textiles, but I think I can change that.
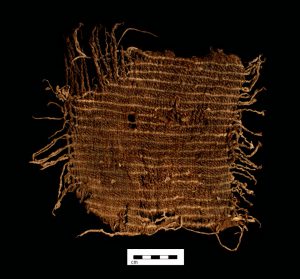
A fragment of a bag from a Kentucky rockshelter. Complete objects, like bags, are very rare from archaeological sites. We will look at this fragment, as well as a few others, as we make our bag.
Over the next several months, I’m going to try to replicate two different kinds of textiles, a slipper and a small bag. I’m going to start at the very beginning with gathering the plants and how to process them for fiber. I’ll be experimenting with different ways of spinning the fiber and how the yarn I make matches up with the archaeological examples. There will be the weaving of each object and a ‘field test’ to make sure they can function as they are supposed to. In the end, we’ll compare my replicas with the originals and see what we’ve learned. I’m definitely not the first person to try this sort of project with archaeological textiles, and we’ll talk about the projects that have come before me. I’ll be checking in on the PLY blog periodically to document my progress, and I’ll report on both my successes and my failures. This is science folks; I expect there to be some failure along the way.
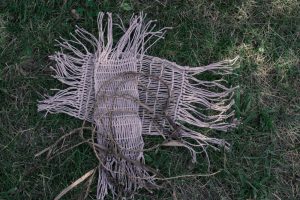
A few examples of yarn and textiles I’ve made to learn about how prehistoric fabrics were constructed.
Next time, we’ll get to know the two objects I’m going to be replicating. We’ll take a look at their yarn and weave structure and make some guesses about what was done to produce each object. That will serve as our roadmap for the whole process. Stay tuned!
Chris Pappas is an archaeologist by day and a fiber fanatic by night who is happiest when she can be both at the same time. She lives in Kentucky with her husband, adorable baby girl, and two crazy beagles.
My Favorite Way to Get Spinning Done
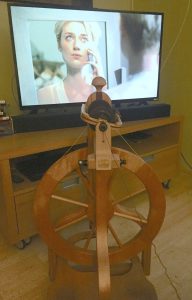
Have you watched the Night Manager?
It seems like at the beginning of the new year every spinner I know has the goal of spinning more.
Me included! This year I want to spin 10 new-to-me-dyers and make 12 things for myself (some handspun some not).
I have a favorite trick to get myself to spin more, it works for me every time. I get hooked on a TV show.
More specifically, I get hooked on a TV show and only let myself watch it when I spin.
I am amazed how much I get done because I want to see that next episode (and the one after that).
I just finished watching The Crown (and yarn for a cowl, a hat and another 4 ounces of fiber spun) and I am just starting and am quite taken with Mozart in the Jungle (lots of swatching,yarn for another hat and I’m about to start some lace spinning).
How do you trick yourself into spinning more?
Save
Save
Don’t rely on the USPS to forward PLY!
I know, I know, you look at the USPS website and it promises that it will forward your periodicals (magazines) to you, at no cost, for 60 days. But it’s a lie. Or at the very least, it is likely to be a lie. I know that every once in a while they get forwarded but there seems to be no good way to predict which will and which won’t. So, I can’t explain why but I can tell you what is really likely to happen to your magazine when you move and rely on the USPS to forward your PLY Magazine to you. There are 3 different scenarios, each more gruesome than the last.
The first one is that they take the plastic wrapper (either the whole thing or just snip off your address), write on your new address, put it in an envelope and mail it to PLY with a postage due of .57 (for the mailing of the plastic with your new address). And then they shred the magazine.
The 2nd and slightly more common one is that they print a label with your new address right on top of the plastic wrapper (or stamp “can’t forward”), photocopy the whole thing, mail the photocopy to me with postage due of .57. And then they shred the magazine.
The 3rd and most common is that they open the plastic wrap, tear the cover off the magazine (or sometimes, just the part that says PLY, put both the plastic (either with your new address or with a stamp that says “can’t forward”) and the cover of the magazine in an envelope and mail both to me with postage due of $1.17. And then they shred the rest of the magazine.
About a month after we ship each issue I get somewhere between 50 and 200 of these. It breaks my little heart and it keeps you from getting your magazine! And the costs of it all is starting to really add up. If you’re interested, here’s how it breaks down: if we reship it to you, we can’t reship your original mag because the PO has shredded it, so the original printing of the mag – $5, plus the $1 periodical shipping is gone and now it’s another $5 (new issue’s printing cost) plus now that we can’t use periodical postage (that only works for the initial shipping, from the printer), the new shipping cost is $6 because the magazine is so heavy! Plus the postage due for the USPS shipping me the notice that you didn’t get the magazine is either .57 or $1.17. So when you work it out, that one issue costs PLY $11-$12 extra to get it to you, which is exactly or a little more than what each domestic subscription brings in above the cost of the 4 mags (printing and shipping). And since we rely on that $12 from each subscription to pay all the bills and salaries, it’s rough.
Plus, you don’t get your magazine (or you don’t get it in a timely fashion).
Plus, they shred the magazine!
So please please please don’t rely on the USPS, log in to your PLY account on the subscribe page (choose resubscribe or change address) using your (previous) zip code and mag code (on the label of your magazine) or, if you don’t have that, your email and password. If you don’t have either, email us at contact.us@plymagazine.com and we’ll help!
Let’s put an end to senseless shredding together!
Leave a Reply
Want to join the discussion?Feel free to contribute!